Produkcja wyrobów betonowych i żelbetowych. Metody wytwarzania wyrobów i konstrukcji żelbetowych
Jedzenie do przemyślenia. Jak.
W fabrycznej produkcji wyrobów żelbetowych powszechnie stosuje się trzy główne metody produkcji: przepływ kruszywa, przenośnik i stół. Odmianą metody ławkowej jest metoda kasetowa.
Metoda przepływu agregatowego wytwarzanie konstrukcji charakteryzuje się podziałem procesu technologicznego na: pojedyncze operacje lub ich grupy; wykonywanie kilku różnych rodzajów operacji na jednostkach uniwersalnych; obecność swobodnego rytmu w przepływie; przenoszenie produktu z poczty na pocztę; formy i produkty przemieszczają się od stanowiska do stanowiska w losowych odstępach czasu, zależnych od czasu trwania operacji na danym stanowisku pracy, który może wahać się od kilku minut (np. smarowanie form) do kilku godzin (dotwardzanie formowanych wyrobów).
Metoda przepływu agregatowego różni się także tym, że formy i produkty nie zatrzymują się na wszystkich stanowiskach linii produkcyjnej, a jedynie na tych, które są w danym przypadku niezbędne. Metoda agregatowo-przepływowa organizacji produkcji charakteryzuje się możliwością przypisania do jednej linii produkcyjnej produktów różniących się nie tylko standardowymi rozmiarami, ale także designem. Szansę tę stwarza obecność na linii produkcyjnej urządzeń uniwersalnych.
Międzyoperacyjny transfer produktów na tych liniach odbywa się za pomocą pojazdów dźwigowych i transportowych. Do przyspieszonego utwardzania betonu metodą przepływu kruszyw zwykle stosuje się komory okresowe lub ciągłe.
Niewielka objętość każdej sekcji komory pozwala spędzić minimum czasu na załadunku i rozładunku produktów oraz duża liczba takich sekcji stwarza warunki do ciągłego dostarczania uformowanego wyrobu do komory utwardzania.
Technologię kruszywa przepływowego charakteryzuje duża elastyczność i zwrotność w zastosowaniu urządzeń technologicznych i transportowych, w trybie obróbki cieplnej, co jest istotne przy wytwarzaniu dużej gamy wyrobów.
Linia produkcyjna obejmuje: formierkę z układarką betonu; instalacja do przygotowania i ogrzewania elektrycznego lub mechanicznego naprężenia zbrojenia; zgnić; komory utwardzające; obszary strippingu, chłodzenia produktów, ich wykańczania lub wykańczania, kontroli technicznej; stanowisko do czyszczenia i smarowania form; obszary bieżącego składowania zbrojenia, elementów osadzonych, izolacji, magazynowania form zapasowych, ich wyposażenia oraz bieżących napraw; stanowisko do testowania gotowych produktów.
Na liniach do produkcji kruszywa produkowane są pale, poprzeczki, bloki fundamentowe, rury o swobodnym przepływie, płyty wielodrutowe, podpory jednopustowe i pale, które formowane są na platformie wibracyjnej w pojedynczych formach z formami pustymi bez mechanizmów wibracyjnych. Panele wielopuste są również formowane na słupach przy użyciu kształtowników pustych wyposażonych w mechanizmy wibracyjne. Rury ciśnieniowe i bezciśnieniowe, kolumny puste, dreny, podpory linii energetycznych i oświetleniowych - na wirówkach walcowych i walcowych oraz taśmowych w postaci rozłącznej i jednoczęściowej. Rury ciśnieniowe formowane są przy użyciu specjalnego sprzętu do wibrohydroprasowania. Zewnętrzne panele ścienne, ekrany loggi i ciągi schodów formowane na stole udarowym w formach stalowych i niemetalowych. Pomieszczenia blokowe i kabiny sanitarne - w jednostkach specjalnych i z wykorzystaniem technologii próżniowej.
Dzięki większemu podziałowi procesu technologicznego na poszczególne procesy elementarne, zgodnie z jednym rytmem, możliwa jest ciągła organizacja produkcji. Linia produkcyjna wyposażona jest w niezbędne pojazdy. Technologia ta nazywana jest metodą półprzenośnikową. Metoda ta znajduje szerokie zastosowanie przy formowaniu na platformie wibracyjnej z osłoną załadunkową pojedynczych lub grupowych form płyt stropowych i pokryć, a także płaskich i żebrowanych paneli, słupów i poprzeczek.
Poniżej znajdują się przykłady wytwarzania różnych wyrobów żelbetowych z wykorzystaniem technologii przepływu kruszywa.
Linia technologiczna do produkcji słupów, poprzeczek i pali składa się ze słupów, na których następuje czyszczenie i smarowanie form, układanie zbrojenia naprężonego oraz układanie i zagęszczanie mieszanki betonowej. Obróbka cieplna produktów odbywa się w komorach wgłębnych. W wyrobach gotowych wycina się zbrojenie prętów i przenosi naprężenia na beton, po czym na wózkach samojezdnych transportuje je do magazynu wyrobów gotowych.
Większość krajowych fabryk stosuje metodę kruszywa do produkcji podkładów w formach dziesięciomiejscowych (pięć podkładów na długości dwóch nitek o łącznej długości do 14,26 m) typu S-56 (beton strunowy), które są wykonane z betonu o wytrzymałości 50 MPa, a jako Do zbrojenia sprężającego stosuje się drut okresowy o wysokiej wytrzymałości o średnicy 3 lub 5 mm.
Gotowy pakiet sznurka montowany jest za pomocą trawersu na przenośniku rolkowym i podawany do słupka napinającego na formie. Są napinane w dwóch etapach. W pierwszym etapie zbrojenie jest napinane do 30% wartości projektowej, po czym w formie montowane są przepony rozdzielające i obejmy wzmacniające. W drugim etapie pod ogrodzeniem pakiet sznurków zostaje naprężony siłą 380 kN i wytrzymywany przez 4 minuty. w celu rozluźnienia naprężeń wewnętrznych, następnie siłę naprężenia usuwa się do wartości standardowej (360 kN) i mocuje specjalnymi śrubami.
Po naprężeniu zbrojenia forma za pomocą suwnicy zostaje przeniesiona na stanowisko formierskie, gdzie za pomocą betoniarki zasypywana jest mieszanka betonowa, która ulega zagęszczeniu. Następnie formę przenosi się na inną platformę wibracyjną, a beton dalej zagęszcza się przy użyciu obciążnika. Następnie zdejmuje się przepony i uchwyty podkładek oporowych, a formę za pomocą suwnicy podaje do komory parowej typu wykopowego, gdzie beton utwardza się w trybie 3 + 4 + 2 godzin w temperaturze 85°C i wilgotności co najmniej co najmniej 95%.
Po odparowaniu forma jest podawana za pomocą dźwigu na słup w celu usunięcia zacisków kotwiących i przeniesienia naprężeń na beton. Wytrzymałość musi wynosić co najmniej 35 MPa. Forma przenoszona jest za pomocą dźwigu na hydrauliczną przechyłkę dźwigniową, która obraca dwa pasma podkładów o 180° na przenośnik płytowy, a forma wysyłana jest na stanowisko w celu oczyszczenia smaru, zamontowania przepony itp. Pasma podkładów docierają na stanowisku rozbioru, a następnie do układania w stosy, umieszczane są w workach po 20 podkładów (5 rzędów po 4 podkłady w każdym) w celu dojrzewania przez 8 godzin i wysyłane do magazynu wyrobów gotowych. Proces technologiczny przebiega według wzoru zamkniętego, w rytmie 10 – 12 minut. dokonywać.
Do produkcji żelbetowych rur walcowanych wibracyjnych ze spiralnym zbrojeniem krzyżowym Stosuje się metodę wibrohydroprasowania. Żelbetowe rury ciśnieniowe wykonywane są o średnicach 800 i 1200 mm, długości użytkowej 5000 mm dla ciśnienia obliczeniowego 0,5; 1,0; 1,5 MPa.
Do przygotowania rur metodą wibracyjno-hydroprasowania stosuje się specjalnie zaprojektowane formy. Forma składa się z osłony zewnętrznej i rdzenia. Obudowa może być wykonana z dwóch lub czterech elementów, mocowanych za pomocą śrub z kalibrowanymi sprężynami. Formularz składa się z dwóch etapów. W pierwszej kolejności montowana jest forma zewnętrzna za pomocą śrub z kalibrowanymi sprężynami, następnie następuje jej czyszczenie, smarowanie i uszczelnianie połączeń.
Forma wewnętrzna to metalowy rdzeń z dwiema ściankami, z których jedna (zewnętrzna) posiada perforację. Na rdzeń nakładana jest gumowa osłona.
W przygotowanej formie montuje się spiralną ramę wzmacniającą. Pierścienie podporowe są wzmocnione na końcach formy. Przez otwory pierścieni przeprowadza się pręty zbrojenia podłużnego, które napręża się za pomocą podnośników hydraulicznych. Montaż dwóch części formy (zewnętrznej i rdzenia) odbywa się na stanowisku kompletacyjnym. Następnie na górze formy instalowany jest pierścień centrujący. Przygotowana forma podawana jest za pomocą dźwigu na słup formierski. Deskowanie odbywa się przy użyciu betoniarki mostowej wyposażonej w mobilne bunkry. Po zagęszczeniu wibracyjnym forma kierowana jest na stanowisko hydroprasowania i obróbki cieplnej. Ciśnienie w układzie hydraulicznym wzrasta do 2-3 MPa przy temperaturze wody do 60 - 70°C.
Pod ciśnieniem hydraulicznym wody, która przedostaje się przez perforowane ścianki rdzenia, gumowa osłona rozszerza się (jednocześnie dociskając mieszankę betonową) i poruszając się, wypycha formę zewnętrzną, skręcaną kalibrowanymi sprężynami. Rozciąga zbrojenie spiralne, tworząc jego naprężenie wstępne.
Obróbkę cieplną parą przeprowadza się pod poszyciem płótna przez 5-7 h. Po zakończeniu obróbki cieplnej należy zdjąć pokrycie płótna, usunąć rdzeń, odciąć końce zbrojenia, przenosząc naprężenia na beton, następnie szlifować gniazdka. Gotowe rury dostarczane są do jednostki hydrotestów. Przed wysłaniem rur do magazynu wyrobów gotowych są one impregnowane ciekłym szkłem sodowym.
W skład wyposażenia modernizowanych linii, oprócz produkowanych seryjnie, wchodzą: instalacje do produkcji listwy rozdzielającej z płatkami harpunowymi oraz do produkcji zszywek w kształcie litery U; maszyna do nawijania ram spiralno-krzyżowych; urządzenie do zaciskania zszywek, do realizacji metody zbrojenia spiralno-krzyżowego, pełniące funkcję zbrojenia spiralnego i podłużnego. Wydajność linii wynosi od 10 do 15 tys. m3 rocznie (w zależności od średnicy rur).
Rury żelbetowe ciśnieniowe o średnicy 1200 - 2000 mm produkowane są metodą wirowania w technologii trzystopniowej. Rury żelbetowe ciśnieniowe, produkowane metodą walcowania odśrodkowego, przeznaczone są do układania rurociągów o różnym przeznaczeniu komunalnym, stosowanych w instalacjach kanalizacyjnych i innych.
Rury żelbetowe ciśnieniowe kielichowe powstają w technologii trójstopniowej. Najpierw wykonuje się rdzeń żelbetowy ze zbrojeniem naprężonym lub stalowym cienkościennym cylindrem i mieszaninę zagęszcza się przez wirowanie. W drugim etapie, po parowaniu i stwardnieniu wodnym rdzenia, nawija się na niego zbrojenie sprężone. W trzecim etapie rdzeń z nawiniętym wzmocnieniem pokryty jest warstwą ochronną zaprawa cementowa metodą torkretową lub natryskową.
Metoda przenośnikowa charakteryzuje się następującymi cechami: maksymalny podział procesu technologicznego na operacje wykonywane na odrębnych stanowiskach pracy; przenoszenie form i produktów od słupka do słupka w ustalonym rytmie.
Produkty podczas przetwarzania są przenoszone przez pulsujący przenośnik, który automatycznie stwarza warunki dla pełniejszej synchronizacji. Przenośnikowy sposób organizacji produkcji charakteryzuje się wymuszonym rytmem, tj. ruch formowanych wyrobów odbywa się w ścisłej kolejności przez te same stanowiska formierskie, z określoną prędkością ruchu. Wymaga to, jako warunku koniecznego, kompleksowej mechanizacji operacji przy użyciu automatycznych urządzeń technologicznych. Do transportu międzyoperacyjnego zazwyczaj wykorzystywane są pojazdy zmechanizowane. pojazdy typ liniowy - przenośniki wózkowe, składające się z określonej liczby wózków paletowych, które poruszają się za pomocą łańcucha trakcyjnego po torach kolejowych.
Równolegle do linii formowania, ale zwykle w odwrotny kierunek prowadzona jest obróbka cieplno-wilgotnościowa produktów. W zależności od rodzaju urządzenia do obróbki cieplnej produktów, linie przenośnikowe wykonywane są z komorami wielopoziomowymi, szczelinowymi, wgłębieniowymi oraz z urządzeniami pakującymi do bezdętkowej obróbki cieplnej produktów w termoformach. Linie mogą się również różnić w zależności od sprzętu formierskiego. Z reguły każda linia transportowa specjalizuje się w produkcji jednego rodzaju produktu.
Metoda przenośnikowa do produkcji wyrobów żelbetowych pozwala osiągnąć kompleksową mechanizację i automatyzację procesów technologicznych wytwarzania produktów, znaczny wzrost wydajności pracy i wzrost wydajności gotowych produktów przy najbardziej kompletnym i efektywnym wykorzystaniu technologii sprzęt. Zastosowanie tej metody jest racjonalne w przypadku masowej produkcji wyrobów w ograniczonym asortymencie przy minimalnej liczbie standardowych rozmiarów.
Głównie panele ścienne produkowane są metodą przenośnikową..
Linia produkcyjna do produkcji paneli ścian zewnętrznych składa się z piętnastu słupów i jest przenośnikiem zamkniętym pionowo. Na jego górnej kondygnacji znajdują się stanowiska technologiczne: rozbiórki, czyszczenia i smarowania form wózków, układania zbrojenia i osadzonych elementów, układania i zagęszczania mieszanki betonowej, wykończenia powierzchni. Obróbka cieplna wyrobów realizowana jest w dwóch wariantach: w podziemnych otworach szczelinowych lub w komorach ciągłych montowanych w podłodze.
Linia przenośników dwużyłowych przeznaczona jest do produkcji jedno- i trójwarstwowych płyt ścian zewnętrznych w zakładach KPD. Linia przenośników dwupasmowych obejmuje urządzenia podwieszane na wiadukcie, podziemne komory szczelinowe oraz manipulatory portalowe. W jednym ciągu ruchu z linią główną znajduje się przenośnik wykańczający.
Do produkcji paneli ściany wewnętrzne Do transportu płyt koleją jednoszynową wykorzystują linię kasetowo-przenośnikową. Linia jest przenośnikiem zamkniętym poziomym do formowania płyt w sposób pionowy, formowanie i utwardzanie wyrobów odbywa się w formie wielomiejscowej kasety. Przygotowanie komór formierskich odbywa się na wyspecjalizowanych stanowiskach wyposażonych w automatyczne instalacje do czyszczenia i smarowania paneli. Na linię dostarczane są gotowe objętościowe klatki wzmacniające. Panele transportowane są za pomocą wózków podnośnikowych po torze jednoszynowym. Przygotowanie komór formierskich odbywa się na pierwszej zmianie, formowanie na drugiej. Dostarczenie i rozmieszczenie wysoce mobilnej mieszanki betonowej odbywa się za pomocą pompy do betonu, co znacznie obniża koszty pracy podczas formowania. Forma kasety wielomiejscowej ma jeden obrót dziennie.
Linia do prasowania walcowego przeznaczona jest do produkcji szerokiej gamy wyrobów z betonu piaskowego do produkcji kamieni bocznych, kamieni trawnikowych itp.
Zaciskanie odbywa się za pomocą obrotowego walca z wielokrotnym wlewaniem pod niego mieszanki betonowej. Kiedy pod walec dostanie się nowa porcja mieszanki betonowej, zagęszczone warstwy rozsuwają się na boki i do góry, układając je w koncentryczne okręgi. W miarę napływu nowych porcji mieszanki ich grubość maleje, rozciągają się, pozostając nierozłącznymi. Cząsteczki mieszaniny znajdujące się w warstwach przemieszczają się względem siebie, a warstwy przesuwają się jedna ku drugiej. Następuje rodzaj wzajemnego mielenia warstw, podczas którego mieszanina staje się gęstsza.
Formowanie przebiega w następujący sposób. Najpierw wałki wprawia się w ruch obrotowy, następnie pod wałki przesuwa się formę i pod nie wylewa się mieszankę betonową, którą rozwałkowuje się na całej szerokości i grubości wyrobów.
Linia stanowi zautomatyzowany poziomo zamknięty przepływ przenośnikowy z pełnym zakresem operacji technologicznych: odbiór; pośrednie magazynowanie i transport mieszanki betonowej; formowanie produktu; obróbka cieplna produktów; przygotowanie formularzy; pakowanie gotowych produktów; transport paczek z gotowymi produktami do magazynu produktów.
Oprócz głównych operacji technologicznych na każdym etapie wykonywany jest szereg operacji pomocniczych: repozycjonowanie produktów po wstępnej obróbce cieplnej; przesuwanie produktów na palecie; kontrola jakości gotowych produktów.
Linia produkcyjna obejmuje: system automatycznego sterowania urządzeniami, zestaw urządzeń do kontroli jakości wyrobów gotowych, system automatyki do regulacji procesu obróbki cieplnej, awaryjne urządzenia blokujące oraz zestaw urządzeń mechanicznych.
Metoda ławkowa produkcja wyrobów żelbetowych charakteryzuje się następującymi głównymi cechami: cały proces produkcyjny odbywa się w stałych formach lub na specjalnych stojakach; produkty pozostają nieruchome podczas przetwarzania, a praca i wyposażenie technologiczne przechodzi z jednej formy do drugiej; Do każdego stojaka lub formy przypisany jest jeden lub więcej produktów jednorodnych technologicznie.
Klasyfikacja rodzajów produkcji stołowej opiera się na szeregu czynników: liczbie standardowych rozmiarów produktów przypisanych do stoiska; sposób rozmieszczenia konstrukcji na stojaku; cechy konstrukcyjne instalacja ławki; trwania cyklu produkcyjnego.
W zależności od ilości stałych standardowych wymiarów produktów, instalacje ławkowe dzielimy na specjalistyczne (kasety do produkcji biegów schodów i podestów, stojaki do produkcji belek podsuwnicowych, kratownic wielokątnych itp.) i uniwersalne (produkcja różnorodnych technologicznie produkty jednorodne).
Na stoisku produkty można ustawiać pionowo, poziomo, sekwencyjnie, pojedynczo lub w opakowaniach, co wpływa na cechy konstrukcyjne instalacji stoiska. W zależności od konstrukcji, instalacje ławkowe mogą być stacjonarne lub składane. Instalacje stacjonarne wykonujemy w formie form metalowych, żelbetowych i matryc betonowych o gładkiej polerowanej powierzchni. Składane formy metalowe i żelbetowe występują w postaci odłączanych kaset grupowych i stojaków formierskich.
Stojak na tace różni się od stojaka podłogowego tym, że jest nieco zagłębiony w stosunku do poziomu podłogi, co umożliwia przykrycie go pokrywkami w celu podgrzania produktów. Głębokość stojaka jest przyjmowana w zależności od grubości formowanych produktów. Zgodnie z metodą zbrojenia stojaki są dwojakiego rodzaju: pakowane i przeciągane.
W przypadku stojaków na opakowania zbrojenie (wiązki opakowań z zaciskami na końcach) montuje się w osobnej instalacji, a następnie przenosi i umieszcza w uchwytach stojaków lub form. Na stanowiskach przeciągających drut zbrojeniowy odwijany jest ze zwojów zamontowanych na jednym końcu stanowiska i rozciągany na całej długości aż do drugiego ogranicznika bezpośrednio na linii formowania.
Stosując stojaki na opakowania, zaleca się wytwarzanie wyrobów o stosunkowo małych wymiarach poprzecznych i zwartym rozmieszczeniu zbrojenia w przekroju. Wyroby liniowe o dużej wysokości lub szerokości, posiadające duży przekrój i wymagające indywidualnego lub grupowego wypełnienia przekroju drutem zbrojeniowym, zaleca się wytwarzanie na stanowiskach przeciągających.
W produkcji stanowiskowej do formowania wyrobów stosuje się następujące typy urządzeń: stacjonarne formy metalowe i żelbetowe, przeznaczone do formowania zakrzywionych i płaskich wielkogabarytowych cienkościennych konstrukcji; formy składane i nierozkładane metalowe i żelbetowe; stojaki grupowe, łączone w pakiety o znacznej długości, służą do produkcji belek zbrojonych naprężeniowo, płyt żebrowych, podkładów itp.; stojaki betonowe o powierzchni polerowanej do formowania różnego rodzaju konstrukcji wielkogabarytowych w formach zarówno ze zbrojeniem konwencjonalnym, jak i naprężeniem zbrojenia.
Długie produkty liniowe ze zbrojeniem naprężonym są formowane na długich stojakach o długości 75 m i więcej, a także na krótkich stojakach o długości równej jednemu produktowi i szerokości równej dwa lub więcej.
Stanowiska długie służą do jednoczesnej produkcji kilku identycznych wyrobów w formach ustawionych jedna za drugą i tworzących jedną linię formierską. Na tej linii układanie i napinanie zbrojenia oraz betonowanie i utwardzanie wyrobów odbywa się natychmiastowo na całej długości stoiska.
Rodzajem krótkich stojaków są metalowe formy energetyczne, na których wykonywane są wyroby sprężone.
Poniżej znajdują się przykłady wytwarzania różnych wyrobów żelbetowych metodą stołową.
Metoda produkcji kaset, Będąc zasadniczo metodą laboratoryjną, wyróżnia się jako odrębna grupa.
Istotą tej metody jest to, że formowanie wyrobów odbywa się w pozycji pionowej w stacjonarnych, rozbieralnych formach kasetowych z blachy grupowej, w których wyroby przetrzymywane są do czasu uzyskania przez beton określonej wytrzymałości. Ogniwo robocze biorące udział w produkcji produktu przemieszcza się z jednej instalacji kasetowej na drugą, co przy odpowiedniej liczbie form pozwala na ciągły przepływ produkcji.
Metodą kasetową wykonuje się wewnętrzne panele ścienne nośne, panele podłogowe, płyty balkonowe i inne wyroby żelbetowe o wymiarach odpowiadających wymiarom przedziałów instalacji kasetowych. W instalacjach kasetowych ruchome mieszanki betonowe o zanurzeniu stożka 7-9 cm i większym przy maksymalnym uziarnieniu kruszywa 20 mm.
Produkty są wytwarzane w następujący sposób. Po oczyszczeniu, nasmarowaniu i złożeniu zespołów kaset, w komorach formierskich instalowane są klatki wzmacniające i osadzone części. Następnie są wypełnione mieszanką betonową. Mieszankę betonową zagęszcza się poprzez wibrację. W zależności od konstrukcji zabudowy kasety drgania mieszanki betonowej mogą być przenoszone przez ramę zbrojeniową, grzebień wibracyjny, drgania wewnętrznych ścianek działowych, a także drgania dna komory formy kasetowej. Po zagęszczeniu wierzchnią powierzchnię wyprasek wygładza się i pokrywa przykryciami, matami lub foliami polimerowymi, aby zapobiec odparowaniu wilgoci z betonu podczas obróbki cieplnej.
Instalacje ze składanym rdzeniem przeznaczone są do formowania i obróbki cieplnej elementów objętościowych szybów wind, odcinków kolektorów i przejść dla pieszych. Cykl produkcyjny produktu trwa 6 godzin.Jednocześnie można formować dwa elementy szybów windowych, dwie sekcje kolektorów lub jeden odcinek przejść dla pieszych.
Charakterystyczną cechą instalacji do produkcji elementów objętościowych jest obecność składanych rdzeni, które pełnią funkcje wewnętrznych elementów budujących formę. W stanie roboczym konfiguracja rdzeni odpowiada kształtowi i wymiarom wewnętrznego obrysu produktu. Na tym stanowisku odbywa się formowanie i obróbka cieplna produktów. Zagęszczanie mieszanki betonowej odbywa się za pomocą zamontowanych wibratorów. Po zakończeniu obróbki cieplnej rdzeń jest wyjmowany z produktu za pomocą dźwigu, a jego elementy formujące (ściany) składają się automatycznie. Kinematyka mechanizmu rdzenia zapewnia swobodne usuwanie elementów szalunkowych przymocowanych do jego ścianek z wyrobu podczas rozszalowania.
Instalacja składa się z rdzenia osadzonego na amortyzatorach i wyposażonego w wibratory, szalunku zewnętrznego zamontowanego na ramie zamykającej rdzeń oraz trawersy dociskowej dźwigni.
Instalacja ta działa w następujący sposób: mieszankę betonową umieszcza się w przygotowanej formie przy jednoczesnym wibrowaniu. Po obróbce cieplnej produktu na rdzeniu za pomocą dźwigu instaluje się trawers dociskowy, palce wkłada się w oczka zewnętrznych paneli i włącza się cylinder hydrauliczny, który obraca dźwignie trawersu przez pręty. Dźwignie obracają się i jednocześnie podnoszą panele zewnętrzne, a one z kolei podnoszą ramę. Rama dociska produkt podnosząc go na wysokość 160 mm. Produkt oddziela się od rdzenia. Następnie zdemontuj trawersę w odwrotnej kolejności, otwórz boki zewnętrzne, a następnie za pomocą dźwigu wyjmij produkt z rdzenia i zainstaluj go na przenośniku wykańczającym. Technologia ciągłego formowania wyrobów betonowych i żelbetowych
Formowanie ciągłe charakteryzuje się tym, że procesy układania, zagęszczania i kształtowania mieszanki betonowej realizowane są jednocześnie w lokalnej objętości (formierce), która wraz z częściami roboczymi maszyny porusza się w sposób ciągły względem formy, podstawę lub paletę, po której przejściu pozostaje w pełni uformowany produkt.
Metoda ciągłego formowania ma następujące zalety: wysoką wydajność, która pozwala zmniejszyć zużycie energii podczas formowania 3-4 razy; wysoki stopień jednorodności i zagęszczenia betonu w całej objętości wyrobu; wysoki stopień jakości powierzchni formowanego produktu; minimalne odchylenia w wymiarach uformowanego produktu; pełna mechanizacja i automatyzacja procesu formowania.
Maszyny do formowania ciągłego, które wykorzystują śruby, tłoki, stemple i wirniki do pompowania mieszanki betonowej do maszyny formierskiej poruszającej się pod działaniem sił wtrysku, nazywane są wytłaczarkami. Maszyny i urządzenia do formowania ciągłego znajdują zastosowanie w procesach produkcyjnych stołowych, przepływowych i przenośnikowych.
Technologia ta stała się powszechna w produkcji wyrobów żelbetowych na długich stojakach (100 - 150 m). W technologii tej produkowane są płyty kanałowe, dwu- lub trójwarstwowe płyty ścian zewnętrznych, belki, płatwie, poprzeczki itp. Z reguły wszystkie te produkty są wstępnie naprężone. Jako zbrojenie sprężające stosuje się drut lub splotki o dużej wytrzymałości.
Wytłaczarka to maszyna do formowania płyt kanałowych w długich stojakach. Rama wytłaczarki wyposażona jest w cztery koła, które toczą się po szynach przyspawanych do palety stojaka. Rama wyposażona jest w osprzęt elektryczny, przekładnie z silnikami elektrycznymi, zbiornik na mieszankę betonową, płytę wibracyjną oraz płytę stabilizującą z obciążnikiem. Wewnątrz ramy znajdują się puste kształtowniki i boczne przesuwne boki. Wspornikowa część robocza kształtki pustej składa się ze śruby dociskowej i końcówki stabilizującej. Podstawa świdra ma kształt stożkowy, a średnica zewnętrzna zwojów świdra odpowiada średnicy pustych przestrzeni. Dlatego wysokość zwojów jest zmienna i maleje w kierunku cylindrycznej części ślimaka. Wewnątrz ślimaka znajduje się jednowałowy, niewyważony wibrator połączony wałem z silnikiem elektrycznym. Każde dwie sąsiednie śruby mają prawy i lewy kierunek linii śrubowej i obracają się w przeciwnym kierunku.
Na płycie wibracyjnej zamontowano współosiowo dwa wibratory wysokiej częstotliwości. W obszarze zasobnika pomiędzy ślimakami znajdują się przegrody i dna, które otaczają po obrysie zwoje ślimaka. Wytłaczarka zamontowana jest na szynach. Do leja odbiorczego ładowana jest sztywna mieszanka betonowa o W/C = 0,28 - 0,34.
Do nieprzerwanego dostarczania mieszanki betonowej stosuje się bunkry samobieżne, które dostarczają beton z betoniarni po torach podwieszonych na całej długości palety. Z tych zbiorników mieszanka betonowa przekazywana jest do półportalowych dystrybutorów betonu, które bezpośrednio ładują beton do maszyny formierskiej. Można zastosować także dystrybutory do betonu mielonego, które poruszają się po warsztacie po tych samych torach kolejowych, po których pracuje formierka. Częścią roboczą takiego dystrybutora betonu jest łyżka podnoszono-uchylna.
Mieszanka betonowa pod wpływem własnej masy opada na zwoje ślimaków, które wpychają ją do komory formierskiej. Poziomy nacisk wywierany przez ślimaki działa na ślimaki, ściany boczne i płyty górne. W tym przypadku krawędzie natarcia płyty wibracyjnej i płyty stabilizującej są podniesione. Kąt pochylenia płyty wibracyjnej wynosi 3-4°. Kąt nachylenia płyty stabilizującej wynosi 1-2° i jest regulowany wagowo. Krawędzie spływu tych płyt znajdują się na poziomie desek bocznych, a ich położenie determinuje wysokość formowanego produktu. W ten sposób pod wpływem nacisku i wibracji mieszanka betonowa formuje się i zagęszcza. Powstała pozioma siła reakcji porusza maszynę z prędkością 1-1,5 m/min. Proces formowania odbywa się w sposób ciągły, a wytłoczony pas betonowy o zadanym przekroju pozostaje za wytłaczarką na stojaku.
Aby uzyskać wymaganą czystość dolnej powierzchni płyt i zwiększyć pewność przyczepności zbrojenia sprężającego do betonu, po nasmarowaniu palety stojaków wypełnia się wodą do grubości 6-10 mm do wysokości boku fazowania. Dlatego w dolnej części płyty przy grubości 20 - 30 mm mieszanka betonowa podczas formowania staje się bardziej plastyczna.
Technologia produkcji na długich stojakach jest następująca. Na hali produkcyjnej mieści się 4-5 pasów standów o szerokości 1,2 - 4,5 m w zależności od rodzaju produktu. Na każdej listwie przed formowaniem przeprowadza się operacje czyszczenia i smarowania posadzki, ułożenia i naprężenia zbrojenia. Każdy pas stojaka jest czyszczony i smarowany za pomocą specjalnych urządzeń, które przemieszczają się po stojaku za pomocą przenośnika linowego. Ten sam przenośnik służy do układania i rozprowadzania zbrojenia splotów ze stacjonarnych lub ruchomych uchwytów kręgów. Napinanie i zwalnianie siły rozciągającej zbrojenia odbywa się za pomocą podnośników grupowych zamontowanych na każdej listwie stojaka.
Następnie na początku taśmy umieszcza się maszynę formującą. Pas betonowy formowany jest w sposób ciągły na całej długości stoiska. Podczas procesu formowania bezpośrednio za maszyną rozwijana jest blacha, która przykrywa świeżo uformowany beton i zapobiega parowaniu wody. Obróbka cieplna uformowanego pasa betonu odbywa się poprzez pompowanie podgrzanego oleju do rejestrów lub za pomocą grzejników elektrycznych umieszczonych pod pokładem.
Po obróbce cieplnej taśma betonowa jest cięta na produkty o wymaganej długości. Początek i koniec paska z reguły nie mają wyraźnego kształtu przekroju poprzecznego na długości 0,5-1 m. Dlatego odcinki te są odcinane i marnują się wraz z zamocowanymi końcami zbrojenia sprężającego do przystanków stoisk.
Cięcie listwy betonowej odbywa się za pomocą specjalnej maszyny, która wyposażona jest w tarczową piłę diamentową oraz system mycia i chłodzenia wodą.
Zdejmowanie produktów z pasa stoiska i podawanie ich na wózek w celu zabrania do magazynu odbywa się za pomocą specjalnych chwytaków do rowków wytłoczonych na powierzchniach bocznych lub za pomocą przyssawek próżniowych. Do produkcji rur i wyrobów rurowych szeroko stosuje się formowanie walcowe ze szczególnie sztywnych mieszanek. Główną częścią maszyny formierskiej jest głowica rolkowa, która jest zamontowana na obrotowym drążku podnoszącym. Głowica rolkowa składa się z obudowy z walcem wygładzającym, swobodnie obracających się walcowych rolek osadzonych na osiach w obudowie, tarczy rozprowadzającej oraz łopatek odrzucających na górnych pokrywach rolek.
Kiedy głowica walca się obraca, mieszanka betonowa spada na tarczę rozprowadzającą, jest wyrzucana przez łopatki w stronę ścianek formy i opada pod walce. Rolki pod wpływem siły tarcia obracają się wokół swoich osi i rozwałkują spadającą pod nie mieszankę betonową. Nadmiar mieszanki betonowej jest ściskany przez walce.
Proces formowania odbywa się w sposób ciągły z prędkością 0,6-1,5 m/min. Prędkość obrotowa głowicy 5- i 6-walcowej wynosi 40 - 80 obr/min. Tym samym każda elementarna objętość słupa mieszanki betonowej w kierunku promieniowym poddawana jest pulsacyjnemu ściskaniu z częstotliwością 200 - 480 na minutę, co umożliwia usunięcie powietrza o współczynniku zagęszczenia co najmniej 0,98. Technologia wytwarzania wyrobów z betonu komórkowego
Proces przygotowania mieszanki betonu komórkowego obejmuje szlifowanie surowy materiał do wymaganej dyspersji: wapno - 550-600 m²/kg, spoiwo wapniowo-piaskowe i wapienno-żużlowe - 450-550 m²/kg, spoiwo łupkowo-zolowe 300-400 m²/kg, sucha mieszanka: wapno + piasek - 330- 360 m²/kg, wapno + popiół lotny – 500-600 m²/kg, popiół z łupków bitumicznych + piasek – 300-400 m²/kg; piasek - 140-300 m²/kg;
Przygotowanie zawiesiny aluminiowej lub wodnego roztworu środka spieniającego; - dozowanie surowców w wymaganych ilościach; - mieszanie dozowanych składników surowej mieszanki w specjalnie zaprojektowanych mieszadłach.
Mielenie surowców do betonu komórkowego odbywa się według jednego z następujących schematów technologicznych: - oddzielne mielenie na sucho spoiwa (wapno, żużel, popiół lub piasek) i mielenie na mokro reszty piasku; - połączone mielenie na sucho wszystkich składników (z wyjątkiem poroforu i w niektórych przypadkach cementu portlandzkiego); Szlifowanie spoiny zalecane jest w przypadku, gdy zawartość wilgoci w składniku krzemionkowym (np. popiół z elektrowni cieplnej) jest niska i uniemożliwia jej wstępne podsuszenie.
W przypadku stosowania wapna o niestabilnych właściwościach, w homogenizatorach pneumomechanicznych stosuje się uśrednianie spoiwa na jego bazie. Uśrednianie i magazynowanie osadów piaskowych odbywa się w basenach osadowych. Przyjmuje się obliczoną gęstość osadów: przy technologii wibracyjnej i udarowej – 1700 kg/m3; w technologii wtrysku - 1600 kg/m3. Jako składnik gazotwórczy stosuje się zawiesinę wodno-aluminiową, która przygotowywana jest z proszku lub pasty aluminiowej – w specjalnej instalacji zapewniającej zabezpieczenie przeciwwybuchowe.
Wodne roztwory środków spieniających produkowane są na bazie klejącego mydła kalafoniowego, środka spieniającego PO-6, żywicy-saponiny i wielu innych substancji, w tym syntetycznych na bazie alkilofenoli. Piana przygotowana z dowolnego roztworu spieniającego do produkcji betonu piankowego musi spełniać następujące wymagania: stopień rozszerzalności - co najmniej 15 dm3/kg; współczynnik wykorzystania - nie mniej niż 0,75. Jakość pianki finalnie sprawdzana jest podczas produkcji prototypów betonu piankowego, który powinien charakteryzować się wysokiej jakości strukturą makroporowatą, dużą wytrzymałością i mrozoodpornością.
Do dozowania lepiszczy, osadów i wody stosuje się dozowniki wagowe wyposażone w elektroniczne urządzenia tensometryczne z dokładnością ±1% dla lepiszcza i ±2% dla składnika krzemionkowego.
Mieszankę betonu komórkowego przygotowuje się w mieszalniku hydrodynamicznym lub wibracyjnym. Kolejność załadunku surowców jest następująca: szlam piaskowy + woda + spoiwo lub woda + piasek suchy + spoiwo + dodatki. Po dwóch minutach mieszania wlać do mieszalnika określona ilość zawiesinę proszku aluminiowego i mieszaninę mieszano przez kolejne 1-2 minuty.
Mieszankę Pianobetonu sporządza się w mieszalniku, który składa się z generatora piany i urządzenia mieszającego. W generatorze piany pianę przygotowuje się z wodnego roztworu środka spieniającego, a w mieszalniku roztwór ze spoiwa, składnika krzemionkowego i wody. Przygotowaną pianę wlewa się do mieszalnika i miesza z zaprawą przez 1,5-2 minuty. Następnie mieszankę piankową wyładowuje się na tacę dozującą w celu wypełnienia form. Mieszanka Pianobetonowa powinna pozostać w pojemniku nie dłużej niż 30 minut.
Technologia formowania dobierana jest w zależności od asortymentu wyrobów i surowców zgodnie z przepisami technologicznymi. Formowanie wyrobów z betonu komórkowego można przeprowadzić według jednego ze schematów: przepływ kruszywa w poszczególnych formach; przepływ kruszywa z zmechanizowanym rozdrobnieniem masywu; przenośnik z zmechanizowanym cięciem drewna litego.
Formowanie produktu obejmuje przygotowanie form, umieszczenie ich w formach klatki wzmacniające i osadzonych części, wypełnianie form mieszanką betonową, wstępne utwardzanie wyprasek. Przygotowanie form polega na ich oczyszczeniu, smarowaniu i podgrzaniu do temperatury 40°C.
W przypadku metod wibracyjnych i udarowych formowanie wyrobów odbywa się odpowiednio na platformach wibracyjnych i udarowych przez 10 ± 2 minuty. „Garb” jest odcinany mechanicznie, gdy warstwa wierzchnia osiągnie wytrzymałość plastyczną 0,01-0,015 MPa lub walcowanie wyrobów o wytrzymałości plastycznej 0,015-0,02 MPa. Podnoszenie form z produktami lub szykami odbywa się za pomocą przegubowych poprzeczek lub specjalnych uchwytów, które zapobiegają odkształcaniu się form.
Przy produkcji drobnych bloków i paneli wykorzystuje się je do wycinania masywów. różne kompleksy agregaty rozdrabniające typu „Universal-60”, „Vibroblok” itp. Mieszankę odpadową uzyskaną z rozcięcia „wierztu”, rozbioru masywów wykorzystuje się ponownie poprzez wpompowanie „wierztu” zmieszanego z wodą do mieszalnika.
Utwardzanie wyprasek w poszczególnych formach lub masach uzyskanych w wyniku cięcia odbywa się w autoklawie lub w komorach parowych z wykorzystaniem ogrzewania elektrycznego.
Stripping po wyładunku produktów z autoklawu lub komory parowej przeprowadza się, gdy różnica temperatur pomiędzy powierzchnią produktów a otaczającym powietrzem nie przekracza 40°C. Czas chłodzenia wyrobów wielkogabarytowych w formach przed strippingiem powinien wynosić co najmniej 4 godziny.
W przedsiębiorstwach zajmujących się produkcją wyrobów z autoklawizowanego betonu komórkowego znajdują się wydziały: odbioru surowców, szlifowania, zbrojenia, mieszania betonu, formowania, autoklawowania, rozbiórki i wykańczania wyrobów, a także magazyn wyrobów gotowych.
W przedsiębiorstwach produkujących wyroby z betonu komórkowego nieautoklawizowanego znajdują się wydziały: przyjęcia surowców, mieszania betonu, formowania, parowania i rozbierania wyrobów oraz magazyn wyrobów gotowych.
Produkcja wyrobów żelbetowych obejmuje następujące podstawowe operacje: przygotowanie form, montaż i mocowanie zbrojenia, naprężanie zbrojenia dla wyrobów sprężonych, układanie i zagęszczanie mieszanki betonowej, wykańczanie powierzchni otwartych, obróbkę cieplną i wilgocią, zdejmowanie wyrobów, obróbka gotowych produktów.
Metody wytwarzania wyrobów i konstrukcji żelbetowych
DO Kategoria:
Fabryki i asortymenty wyrobów żelbetowych
Metody wytwarzania wyrobów i konstrukcji żelbetowych
We współczesnej hydrotechnice szeroko stosowane są prefabrykowane konstrukcje żelbetowe. Prefabrykaty betonowe i żelbetowe stosowane są przy wznoszeniu masywnych wysokich konstrukcji, przy budowie tuneli i podziemnych elektrowni wodnych, przepompowni i rurociągów wody walorowej. Zastosowanie prefabrykowanego żelbetu jest najważniejszym ogniwem industrializacji budownictwa i radykalnego ulepszania konstrukcji budowlanych. W przypadku stosowania prefabrykowanego betonu zbrojonego objętość właściwa żelbetu jest znacznie zmniejszona (nawet o 40% w porównaniu do wersji monolitycznej), ilość wymaganego siła robocza(do 50%) i obniżeniu kosztów jednostkowych (o 25-40%).
W warunkach powszechnego stosowania prefabrykatów żelbetowych czas budowy do uruchomienia pierwszych bloków hydraulicznych skraca się do 3,5-4,5 roku, czyli jest bliższy czasowi budowy dużych elektrowni cieplnych.
W tym względzie szczególne znaczenie mają przemysłowe metody masowej produkcji wyrobów i konstrukcji żelbetowych w specjalnych dużych zakładach przemysłowych o wydajności 150-200 tys. metrów sześciennych rocznie, obsługujących tereny przyległe lub na składowiskach odpadów zlokalizowanych bezpośrednio przy placach budowy.
Aby zapewnić budownictwo energetyczne z prefabrykatów, tworzona jest sieć potężnych przedsiębiorstw branży budowlanej oraz bazy regionalne i międzypowiatowe o promieniu działania do 800 km.
W zakładach prefabrykacji żelbetowej powstają zmechanizowane linie technologiczne:
a) do produkcji kodoin, poprzeczek i belek;
b) do produkcji fundamentów i innych konstrukcji masywnych;
c) do produkcji paneli, powłok i sufitów.
W tych przedsiębiorstwach istnieją trzy główne metody mechanizacji produkcji prefabrykatów betonowych i konstrukcje żelbetowe: ławka, jednostka przepływowa i przenośnik przepływowy.
Ryż. 225. Schematy technologiczne wytwarzania prefabrykowanych wyrobów i konstrukcji żelbetowych:
ławka; b - jednostka przepływowa; c - przenośnik przepływowy
W przypadku metody stołowej (ryc. 225, a) wszystkie operacje (formowanie, hartowanie, odpędzanie, obróbka powierzchni) podczas całego procesu wytwarzania produktów przeprowadzane są na stacjonarnych stojakach. Formy z wyrobem zarówno podczas procesu produkcyjnego, układania i zagęszczania mieszanki betonowej, jak i podczas utwardzania betonu pozostają na swoim miejscu, a zespoły produkcyjne i urządzenia technologiczne (mechanizmy formujące) są sekwencyjnie przemieszczane z jednej stacjonarnej formy, w której produkt jest formowany w inny. Sam produkt przesuwa się tylko 1 raz - podczas transportu do magazynu 3 gotowych produktów. Maszyny wykonujące operacje podawania form, zbrojenia i mieszanki betonowej, a także układania zbrojenia, betonowania i rozbierania, przemieszczają się z jednej formy z wytworzonym wyrobem do drugiej.
Metoda stołowa jest odpowiednia do produkcji dużych części, a także przy użyciu specjalnego sprzętu do formowania określonego rodzaju produktu (stół betonowy, kombajn betonowy, pionowe maszyny kasetowe itp.).
Metodę ławkową można przeprowadzić:
a) na gładkich platformach betonowych - do produkcji dowolnych części, ale głównie wielkogabarytowych części płaskich, w których efektywniej wykorzystuje się powierzchnię ogrzewanej podłogi;
b) w komorach parowych instalowanych podczas produkcji konstrukcji masywnych, których ogrzewanie na podłodze termicznej nie zapewnia niezbędnej obróbki cieplnej;
c) na specjalnych stojakach przeznaczonych do produkcji konstrukcji wzmocnionych naprężeniami - belek, płatwi, desek i paneli podłogowych.
Masa produktów formowanych metodą stołową zależy wyłącznie od udźwigu dźwigów.
Metoda kruszywa przepływowego do produkcji prefabrykowanych elementów żelbetowych (ryc. 225, b) charakteryzuje się tym, że operacje technologiczne wytwarzania produktu wykonywane są na różnych stanowiskach pracy. Według tego schematu formy 2 z wyrobami przemieszczane są ze słupa na słupek za pomocą pojazdów podnoszących z przystankami niezbędnymi do zakończenia każdej operacji. W tym przypadku twardnienie betonu nie następuje na miejscu formowania, ale w specjalnych komorach parowania. 5. Po obróbce cieplnej formy wraz z wyrobem przenoszone są na stanowisko szalunkowe, skąd gotowe wyroby transportowane są do magazynu wyrobów gotowych, oraz formy wracają do stanowiska formierskiego.
Metoda kruszywa przepływowego jest bardzo elastyczna i umożliwia najprostszą organizację produkcji różnych produktów: płyt, paneli, desek, płatwi, poprzeczek, kolumn itp. Aby przejść z produkcji jednego rodzaju produktu na inny, wystarczy wymagana jest wymiana form. Ze względu na opłacalność, elastyczność i łatwość rozwoju metoda ta jest szeroko stosowana w fabrykach prefabrykowanych elementów żelbetowych o dowolnej wydajności.
Ciężar wyrobów formowanych metodą agregatów przepływowych jest ograniczony udźwigiem dźwigów i platform wibracyjnych formujących.
W przypadku metody przenośnika przepływowego do produkcji prefabrykowanych elementów żelbetowych (ryc. 225, c) produkty i formy wózków przemieszczają się z jednego słupka na drugi wzdłuż przenośnika z wymuszonym rytmem określonym przez najdłuższą operację; jednocześnie maszyny przetwarzające te produkty i urządzenia pozostają na swoich miejscach, a formy wózkowe najpierw przechodzą przez stanowiska przygotowawcze, gdzie są czyszczone i smarowane.
Następnie docierają do głównych słupów, gdzie w ściśle określonej kolejności układane są zbrojenie i osadzone elementy, a także układana i zagęszczana jest mieszanka betonowa. Po przejściu wszystkich stanowisk produkt kierowany jest do ciągłych tunelowych komór parowych, gdzie jest poddawany działaniu pary i przemieszcza się bez przerwy. Po opuszczeniu komory i późniejszym wyciśnięciu z formy, wyrób trafia do magazynu wyrobów gotowych, a forma trafia na pocztę. Dla każdego rodzaju produktu zakład taki posiada wyspecjalizowaną linię przenośnikową.
Ciężar wyrobów formowanych wykorzystujących technologię przenośników przepływowych jest ograniczony udźwigiem dźwigów i formujących zagęszczarek wibracyjnych, a także mocą elementów trakcyjnych przenośnika.
W fabrykach działających metodą przenośnikowo-przepływową możliwe jest zastosowanie bardziej zaawansowanej technologii i linii automatycznych (walcownie, pionowe instalacje kasetowe), co jest najbardziej ekonomiczne.
Biorąc pod uwagę charakter prefabrykowanych konstrukcji żelbetowych stosowanych w budowie obiektów energetycznych, możliwą koncentrację prefabrykowanych przedsiębiorstw żelbetowych i wielkość ich produkcji, za najbardziej odpowiednie schematy technologiczne uważa się jednostkę przepływową i ławę przepływową.
Na ryc. 226 schematycznie przedstawia metodę przepływową budowy elektrowni wodnej z prefabrykowanego żelbetu.
Proces wytwarzania i montażu produktu składa się z odrębnych operacji. Każda operacja wykonywana jest w wyspecjalizowanych warsztatach lub zakładach. Przenośnik składający się z platform kolejowych z formami łączy pracę warsztatów i placów w jeden proces produkcji. Ov określa przepływ produkcji, przyspiesza wytwarzanie produktów i organizuje ogólny postęp pracy. Cykl przemieszczania platformy z formami rozpoczyna się od warsztatu przygotowania form do miejsca wytworzenia gotowego produktu w zakładzie zbrojeniowym, następnie do formierni produktu, miejsca obróbki cieplnej produktu i miejsca instalacji.
Po wyjęciu gotowego produktu na miejscu montażu platforma wraca do warsztatu przygotowania form i cykl się powtarza. Platforma porusza się po linii produkcyjnej za pomocą lokomotyw silnikowych lub spalinowych.
Produkcja prefabrykowanych wyrobów żelbetowych według dowolnego z omówionych powyżej schematów technologicznych składa się z następujących głównych procesów:
a) odbiór, magazynowanie i transport surowców;
b) produkcja armatury;
c) przygotowanie mieszanki betonowej;
d) części formierskie;
e) przyspieszenie hartowania części;
e) usuwanie i wykańczanie oraz
g) przechowywanie wyrobów gotowych.
Z całego kompleksu procesów składających się na produkcję wyrobów betonowych i żelbetowych najważniejsze jest formowanie; Przyjęta metoda formowania często determinuje sposób wykonania produktu jako całości.
Na proces formowania składają się następujące operacje technologiczne i transportowe: przygotowanie form (czyszczenie, smarowanie i montaż); układanie zbrojenia i osadzonych części lub zbrojenie napinające; ułożenie i rozprowadzenie mieszanki betonowej w formie oraz jej zagęszczenie; obróbka powierzchni czołowej wyrobów formowanych (wyrównywanie, wygładzanie itp.); usunięcie wykładzin tworzących puste przestrzenie i zwolnienie pokładowego wyposażenia form; zwalnianie palet lub form z produktów i zawracanie ich na początek przepływu.
Ryż. 226. Schemat metody przepływowej budowy elektrowni wodnej z prefabrykowanego żelbetu:
1 - warsztat przygotowania form; 2 - zakład wzmacniający; 3 - formownia wyrobów; 4 - obszary obróbki cieplnej produktów; 5 - miejsce instalacji; 6 - betoniarnia; 7 - magazyn kruszywa
Poszczególne operacje, w zależności od rodzaju produktów i przyjętych sposobów ich przygotowania, mogą zostać wyłączone z procesu technologicznego lub zmodyfikowane.
We współczesnej praktyce bierze się pod uwagę metodę zagęszczania i charakter sprzętu formierskiego.
Akceptowane są następujące metody formowania wyrobów:
1) wibrowanie, w razie potrzeby połączone z tłoczeniem, odkurzaniem i prasowaniem mieszanki betonowej;
2) prasowanie i walcowanie;
3) metoda odśrodkowa;
4) odlewanie bez zagęszczania;
5) metoda drukowana w matrycach.
Głównymi urządzeniami do mechanizacji formowania wyrobów są różnego rodzaju formy, urządzenia do ich czyszczenia i smarowania, a także maszyny do układania i rozprowadzania mieszanki betonowej w formach oraz do wykańczania powierzchni czołowej.
Najbardziej pracochłonną operacją wyrobów formierskich jest wkładanie mieszanki betonowej do formy i rozprowadzanie jej w niej. Operacje te we współczesnej praktyce wykonywane są zmechanizowane, przy użyciu samobieżnych betoniarek.
Te ostatnie, w zależności od przeznaczenia, dzielą się na:
a) kostki betonowe z podajnikami taśmowymi – do produkcji metodą przepływowo-przenośnikową;
b) kostki betonowe z obrotowym podajnikiem taśmowym – do metody produkcji ławkowej;
c) betoniarki z podajnikami taśmowymi i urządzeniami do rozprowadzania i wygładzania betonu - do produkcji metodą przepływową.
Układarka do betonu z podajnikiem taśmowym (ryc. 227) do instalacji przepływowo-przenośnikowych składa się z ramy samobieżnej, napędu ramy, podajnika taśmowego, napędu podajnika, amortyzatora do regulacji wielkości szczeliny wylotowej magazynu zbiornik, ręczny mechanizm sterowania przepustnicą, lej zasypowy, zespół zawieszenia linowego, napęd hydrauliczny i zdalne sterowanie. Napędzane są dwa koła ramy samobieżnej. Napęd ruchu ramy składa się z trzybiegowego silnika elektrycznego, przekładni, wału i dwóch napędów łańcuchowych. Podajnik taśmowy składa się z bębnów napędowych i napinających, gumowanego pasa bez końca oraz blachy nośnej. Przepustnica wykonana jest w formie osłony sektorowej zakrywającej wylot zbiornika akumulacyjnego. Mechanizm sterujący przepustnicą składa się z przekładni ślimakowej, wału napędowego, kół zębatych i zębatki.
Ryż. 227. Układarka do betonu z podajnikiem taśmowym do instalacji przepływowo-przenośnikowych
Aby umożliwić formowanie wyrobów o różnej szerokości, położenie ścianek zbiornika magazynowego można regulować za pomocą popychaczy hydraulicznych.
Wydajność tego typu kostek betonowych wynosi 20-50 m3/h. Prędkość jazdy 4-10 m/min. Moc silnika 6-10 kW.
Do układania betonu w formach montowanych na stojaku przedłużonym służy betoniarka z obrotowym podajnikiem taśmowym.
Na podporze wózka samobieżnego betoniarki (rys. 228) zamontowany jest napęd ruchu, napęd obrotu platformy oraz tor stanowiący powierzchnię nośną dla kół obrotnicy. Na ramie tego ostatniego znajduje się kosz przyjęciowy, napęd podajnika taśmowego, napęd podnoszenia wysięgnika podajnika oraz panel sterujący. Lej załadowczy podajnika taśmowego wyposażony jest w zasuwę, za pomocą której reguluje się grubość warstwy betonu na taśmie.
Zagęszczanie betonu metodą wibracyjną przeprowadza się za pomocą wibratorów powierzchniowych i głębokich oraz platform wibracyjnych, które są poziomymi platformami na elastycznych podkładkach, wprawianymi w ruch oscylacyjny za pomocą mechanizmów wibracyjnych. Formę z umieszczonym w niej wytworzonym wyrobem montuje się na poziomej platformie takiego wibratora i poddaje wraz z wyrobem drganiom.
Wibrokompresja to jednoczesne wibrowanie i prasowanie wypraski za pomocą płyty umieszczonej na powierzchni mieszanki betonowej lub wewnętrznych wkładek pneumatycznych. Prasowanie wibracyjne ma znaczną przewagę nad prasowaniem statycznym (bez wibracji), które wymaga cięższych i mocniejszych pras. Wielkość nacisku prasowania wynosi 5-15 KHJM2 (50-150 g/cm2) i zależy od twardości mieszanki betonowej.
Wibrostamping różni się od wibrokompresji tym, że formowany wyrób nie ma płaskiej, lecz wyprofilowanej powierzchni (biegi schodów, płyty żebrowane, podkłady itp.), dlatego profilowana jest również powierzchnia płyty dociskowej, tzw. wibrostempla. Stempel wibracyjny pod wpływem własnego ciężaru i zamontowanego na nim wibratora wciska pożądany relief w wypraskę i zagęszcza mieszankę betonową.
Ryż. 228. Układarka do betonu do zabudowy ławkowej z obrotowym podajnikiem taśmowym
Tłoczenie wibracyjne jest również stosowane w produkcji wyrobów figurowych. W takich przypadkach niezbędny jest zarys dna. powierzchnię uzyskuje się za pomocą matrycy.
Postępowym kierunkiem rozwoju masowej produkcji podobnych wyrobów i części jest przejście do formowania na specjalistycznych maszynach, w których forma lub jej elementy boczne i wkładki stają się integralną częścią samych maszyn formierskich. Podczas formowania wyrobów pustych, takich jak panele, deski tarasowe, bloki ścienne itp., do zagęszczania mieszanki betonowej stosuje się puste w środku, okrągłe lub owalne formy puste z mechanizmami wibracyjnymi we wnęce, zwane wkładkami wibracyjnymi. Wkładki wibracyjne osadzone są na trawersie, która podczas wkładania wkładek do formy i wyjmowania z niej wykonuje ruch posuwisto-zwrotny. W maszynach z wkładkami wibracyjnymi ruch grawera z wykrojnikami jest zwykle łączony z ruchem końca lub wzdłużnych boków formy o określoną wielkość.
Wkładka wibracyjna typu uniwersalnego (pusta forma) pokazana jest na rys. 229. Jest to owalny (okrągły) korpus, w którym wibratory są ułożone szeregowo. połączone ze sobą za pomocą wałów pośrednich ze sprzęgłami przegubowymi. Wały wibratorów wprawiane są w ruch obrotowy za pomocą silnika elektrycznego za pośrednictwem przekładni pasowej, która przenosi obrót na koło pasowe zamontowane na wale wibratora. Naciąg napędu pasowego odbywa się za pomocą rolki napinającej.
Maszyny formierskie współpracujące z wkładkami wibracyjnymi, w zależności od ilości wkładek, mają wydajność od 200 do 900 m? na zmianę. Moc zainstalowana silników elektrycznych waha się od 25 do 75 kW.
Opracowywana jest nowa technologia wytwarzania elementów wielkogabarytowych konstrukcji żelbetowych wykorzystująca dwie metody: metodę walcowania wibracyjnego lub metodę wibrokompresji oraz metodę kasetową w pionowych kasetach wielomiejscowych.
Metoda walcowania wibracyjnego, opracowana w ZSRR, jest szeroko stosowana w produkcji cienkościennych części wielkopłytowych ze wzmocnieniem naprężonym.
Na ryc. 230 przedstawia schemat instalacji do produkcji żeber płyty żelbetowe metodą walcowania wibracyjnego na walcarce zaprojektowanej przez N. Ya Kozlova.
Walcownia składa się z taśmy formującej z wykładzinami, łańcucha nośnego, urządzeń dozujących i mieszających, ślimaka, betoniarki ciągłej, ślimakowej układarki betonu, belki wibracyjnej, tarczy wibracyjnej, prostownicy, urządzenia kalibrującego, gumowana taśma uszczelniająca produkt w obszarze obróbki cieplnej, samotok najazdowy i wywrotka.
Mieszankę betonową przygotowuje się za pomocą urządzeń dozujących i mieszających. Przechodząc przez ślimak, zostaje zwilżony i wchodzi do ciągłego łopatkowego mieszalnika benzyny. Stąd mieszanina jest podawana na taśmę formującą. Panel uformowany jest na poruszającym się bez końca metalowym pasie, będącym szeregiem łańcuchów trakcyjnych, do których przymocowane są wykładziny. Pod łańcuchami znajduje się stała blacha zapobiegająca rozsypywaniu się betonu. Pomiędzy łańcuchami trakcyjnymi znajdują się łańcuchy nośne, na których opierają się podłużne żebra formowanej płyty. Zagęszczenie mieszanki i wypełnienie przestrzeni pomiędzy wkładami zapewnia belka wibracyjna.
Ułożony i zagęszczony beton, poruszając się za pomocą taśmy formującej, przechodzi pod wzornik żeber, który zbiera beton nad żebrami formowanej płyty w ilości niezbędnej do zagęszczenia podczas walcowania, a następnie opada pod urządzenie kalibrujące, gdzie jest ostatecznie walcowany . Urządzenie kalibrujące składa się z bębna i szeregu rolek otoczonych ciągłym pasem bez końca.
Ryż. 230. Schemat walcarki projektu N. Ya.Kozlova
Wkładki zapewniają powstawanie zagłębień w formowanym produkcie. Szczeliny pomiędzy wkładkami odpowiadają grubości żeber. Mieszankę betonową zagęszcza się pod naciskiem do 2500 kn/m2 (25 kg/om2). Belka rozdzielająca służy do oddzielenia jednego panelu od drugiego.
Ryż. 231. Kaseta zmechanizowana
Uformowany panel podawany jest pod taśmą uszczelniającą do strefy obróbki cieplnej, gdzie po dwóch godzinach w temperaturze 100°C płyty uzyskują wytrzymałość około 20 MN/m2 (200 kg/cm2). Następnie gotowy produkt podawany jest na przenośnik rolkowy z podwójnym ścinaniem, a następnie trafia na stanowisko kontroli jakości i montażu paneli.
Na podobnej instalacji walcowniczej można formować nie tylko gładkie przegrody, ale także panele ścian zewnętrznych, z jednej strony gładkie, a z przeciwnej użebrowane, dla czego dolny pas formujący musi mieć odpowiednią powierzchnię profilowaną i służyć jako matryca.
Do produkcji cienkościennych wyrobów żelbetowych metodą kasetową stosuje się pionowe przesuwne kasety metalowe lub żelbetowe (ryc. 231). Dzięki tej metodzie obróbka cieplna produktów odbywa się bezpośrednio w kasetach.
Proces technologiczny wytwarzania paneli w kasetach pionowych wygląda następująco. Po oczyszczeniu i nasmarowaniu powierzchni kaset, które są w stanie rozciągniętym, montuje się przygotowane wcześniej ramy i zabezpiecza osadzone w nich części metalowe (zaciski). Na siatkach ramy montowane są „w rozstawie” osadzone zaciski, zapewniające centralne położenie siatki wzmacniającej w ścianie panelu, po czym ścianki kasety przesuwane są do położenia odpowiadającego wymiarom produkowanej części. Następnie instaluje się specjalne dysze wibracyjne, które mocuje się do elementów siatki wzmacniającej płytę, a do kasety, jednocześnie do wszystkich przedziałów, wprowadza się mieszankę betonową, która podczas układania jest zagęszczana przez wibracje. Po ułożeniu mieszanki betonowej usuwa się dysze wibracyjne i zakłada się pokrywy przykrywające górne powierzchnie płyty.
Panele wygrzewane są przez 2 godziny w temperaturze 96-99°C, po czym produkt przebywa w instalacji kasetowej przez kolejne 4 h. Ze względu na dużą pojemność cieplną instalacji temperatura spada powoli (1-3 °C na godzinę). Po 4 godzinach kasety są rozsuwane. Gotowy panel za pomocą suwnic i wózków transportowych instalowany jest na stanowiskach wydziału wykończeń, gdzie eliminowane są drobne wady, po czym panele wysyłane są do obramowania do produkcji.
DO kategoria: - Fabryki i asortymenty wyrobów żelbetowych
Konstrukcje żelbetowe mogą być produkowane w fabrykach lub na składowiskach śmieci. Fabryki to przedsiębiorstwa, w których główne procesy technologiczne realizowane są w pomieszczeniach (sklepach). Składowiska to przedsiębiorstwa, w których w budynkach przygotowuje się wyłącznie mieszankę betonową i zbrojenie, wszystkie pozostałe procesy - formowanie, utwardzanie i wykańczanie wyrobów - przeprowadzane są na terenach otwartych - na stanowiskach lub w komorach parowych zlokalizowanych na świeżym powietrzu.
Proces technologiczny składa się z szeregu kolejno wykonywanych operacji: przygotowania lub dostarczenia mieszanki betonowej z masy celulozowo-papierniczej, wytwarzania zbrojenia do wyrobów żelbetowych, formowania, przyspieszania utwardzania wyrobów.
W zależności od podziału ogólnego procesu technologicznego formowania wyrobów na poszczególnych stanowiskach wyróżnia się technologie przepływowo-agregatowe, przenośnikowe i stołowe.
W metodzie produkcji kruszywa przepływowego forma i wyrób przenoszony jest wzdłuż strumienia z jednego stanowiska technologicznego na drugie za pomocą urządzeń dźwigowych (rys. 7.6.1).
Ryż. 7.6.1. Schemat technologiczny wytwarzania wyrobów żelbetowych metodą kruszywa przepływowego:
1 - miejsce rozładunku kruszywa; 2 - bunkry odbiorcze; 3 - pojemniki do przechowywania; 4 - magazyn cementu; 5 - galeria transportowa; 6 - pneumatyczne dostarczanie cementu; 7 - pojemniki na wodę, dodatki; 8 - betoniarnia; 9 - urządzenia do produkcji ram i elementów wzmacniających; 10 - jednostka do termicznego podgrzewania armatury; 11 - słupek wzmacniający; 12 - samojezdna układarka do betonu; 13 - jednostka do formowania produktów; 14 - obszar przechowywania produktów; 15 - komora do obróbki cieplnej i wilgotnościowej produktów; 16 - stanowisko do usuwania produktów; 17 - podnoszenie i transport produktów; 18 - wózek samobieżny; 19 - magazyn wyrobów gotowych. Ja - wiatraczek; II - bęben prostujący; III - wałek podający; IV - noże; V - wyłącznik krańcowy
Instalacje - zespoły składają się z maszyny formierskiej (najczęściej platformy wibracyjnej), maszyny do rozprowadzania mieszanki betonowej w formie (układarki betonowe), maszyny do układania formy na stanowisku formierskim (układarki szalunkowe). Uformowane produkty w formach są przenoszone za pomocą dźwigu do komór w celu obróbki cieplnej. Ostatnim etapem produkcji jest wypuszczenie produktów z komory i ich usunięcie. Po akceptacji przez dział kontroli jakości gotowe wyroby wysyłane są do magazynu, a wydane formy zwracane są na stanowisko formierskie.
Przy metodzie przenośnikowej proces technologiczny dzieli się na procesy elementarne, które realizowane są jednocześnie na odrębnych stanowiskach pracy. Forma i produkt przemieszczają się z jednego miejsca pracy na drugie, każde obsługiwane przez stałe połączenie (ryc. 7.6.2).
Ryż. 7.6.2. Schemat technologiczny metody przenośnikowej do wytwarzania wyrobów żelbetowych:
1 - stanowisko do rozładunku kruszywa; 2 - lej odbiorczy, 3 - lej zasypowy, 4 - galeria transportowa, 5 - lej zasypowy, 6 - mieszalnia, 7 - silos na cement; 8 - pojemnik na wodę; 9 - sprzęt do produkcji elementów wzmacniających i ram; 10 - wózek transportowy; 11 - czyszczenie form; 12 - smarowanie form; 13 - układanie zbrojenia; 14 - stanowisko formowania produktu; 15 - słupek wykończeniowy produktu; 16 - słupek do układania warstwy termoizolacyjnej; 17 - komora parowa; 18 - stanowisko rozbiórkowe i kontrolne; 19 - magazyn wyrobów gotowych
Głównym warunkiem realizacji produkcji przenośników jest rytm procesów, dla których czas ich trwania musi być taki sam. Następnie w regularnych odstępach czasu produkt jest jednocześnie przenoszony z jednego miejsca pracy (stanowiska) na drugie. Przy zmianie rodzaju produktów przenośniki wymagają ponownego wyposażenia.
Metodą stanowiskową procesy technologiczne przeprowadza się w stałych formach lub wyposażonych w tym celu stanowiskach na stanowiskach pracy. W trakcie procesu formowania i do czasu uzyskania przez beton wymaganej wytrzymałości produkty pozostają na swoim miejscu, natomiast urządzenia technologiczne i obsługujące je części robocze przechodzą z jednej formy do drugiej. Metoda ławkowa, choć prowadzi do mniejszego wykorzystania przestrzeni produkcyjnej w porównaniu do innych metod, ma szereg zalet, zwłaszcza przy wytwarzaniu konstrukcji sprężonych. Czas trwania cyklu technologicznego zależy od długości czasu przetrzymywania wyrobów na stojaku w celu uzyskania niezbędnej wytrzymałości i wynosi od 1 do 2 dni (rys. 7.6.3)
Ryż. 7.6.3. Schemat technologiczny konstrukcji produkcyjnych na stoiskach:
A - obszar przechowywania i przetwarzania surowców; B - obszar przygotowania betonu; C - strefa produkcji elementów wzmacniających; D - strefa formowania i przetwarzania produktów; E - powierzchnia składowania i dostarczania konstrukcji; 1 - stanowisko do rozładunku kruszywa; 2, 8 - bunkry odbiorcze; 3 - magazyny kruszywa; 4 - galeria przenośników; 5 - pojemniki na materiały eksploatacyjne; 6 - stacja przygotowania betonu; 7 - stacja rozładunku cementu; 9 - magazyn cementu; 10 - stoisko, 11 - magazyn wyrobów gotowych
1. Wstęp
2. Postanowienia ogólne
2.1. Skład przedsiębiorstwa
2.2. Charakterystyka produktu
2.3. Godziny pracy przedsiębiorstwa
2.4. Surowy materiał
3. Część technologiczna
3.5. Obliczenia technologiczne
3.6. Projekt BSO
3.7. Zapotrzebowanie produkcyjne na surowce i zasoby energetyczne
3.8. Magazyn wyrobów gotowych
3.9. Lista pracowników
3.10. Kontrola jakości produktu i dokładności procesu
6. Referencje
betoniarnia kolumna żelbetowa
1. Wstęp
Beton jest jednym z najstarszych materiały budowlane. Zbudowano z niego galerie labiryntu egipskiego (3600 p.n.e.), część Wielkiego Muru Chińskiego (III wiek p.n.e.), szereg budynków w Indiach. Starożytny Rzym i w innych miejscach. Jednak wykorzystanie betonu i żelbetu do budownictwa masowego rozpoczęło się dopiero w drugiej połowie XIX wieku po rozpoczęciu i organizacji produkcji przemysłowej cementu portlandzkiego, który stał się głównym spoiwem konstrukcji i wyrobów betonowych i żelbetowych.
Produkcja prefabrykatów żelbetowych zaczęła się intensywnie rozwijać w okresie powojennym w związku z rozwojem przemysłu i przemysłu inżynieria lądowa, co wymagało powszechnej industrializacji robót budowlanych.
Powszechne stosowanie prefabrykowanego żelbetu umożliwiło znaczne zmniejszenie zużycia metalu, drewna i innych tradycyjnych materiałów w budownictwie, radykalne zwiększenie wydajności pracy oraz skrócenie czasu budowy budynków i budowli. Rozwój budownictwa wymaga jednak dalszej poprawy wydajności i jakości produkcji oraz wykorzystania prefabrykatów żelbetowych.
2. Postanowienia ogólne
2.1. Skład przedsiębiorstwa
Produkcja wyrobów żelbetowych w fabrykach żelbetu odbywa się w warsztatach, które łącznie reprezentują produkcję prefabrykatów żelbetowych.
Główne warsztaty do produkcji wyrobów żelbetowych to:
1. Dział mieszania betonu
2. Formiernia
3. Pomieszczenia gospodarcze i biurowe
4. Magazyn cementu
5. Magazyn zbrojeń
6. Magazyn kruszywa
7. Magazyn wyrobów gotowych
8. Magazyn paliw i smarów
2.2. Charakterystyka produktu
W projekcie wszystkie obliczenia przeprowadzono przy użyciu kolumny gatunku K19a-1-1. Wyrób wytwarzany metodą stołową zgodnie z wymaganiami GOST 18979-73.
Kolumna wykonana jest z ciężkiego betonu klasy 300. Wymiary geometryczne kolumny wynoszą 9575 x 400 x 400 mm.
Charakterystykę produktu podano w tabeli 1.
Tabela charakterystyk produktu 1
2.3. Godziny pracy przedsiębiorstwa
Tabela 2
2.4. Surowy materiał
Surowce do przygotowania mieszanki betonowej
1) Cement portlandzki gatunek 400, spełniający wymagania GOST 10178-85, normalna gęstość zaczynu cementowego 27%;
2) Kruszywo wapienne, spełniające wymagania GOST 8267-93, frakcja 5-20, stopień wytrzymałości na kruszenie - 800, nasiąkliwość - 0,8%, mrozoodporność 150 cykli, zawartość ziaren słabych - 5%, zawartość ziaren łuszczących się - 23 %, zawartość ziaren pylistych, cząstek mułu i gliny – 2%;
3) Piasek spełniający wymagania GOST 8736-93, moduł miałkości Mk = 1,1; zawartość zanieczyszczeń w piasku nie powinna przekraczać 3%, zapotrzebowanie piasku na wodę wynosi 7%;
4) Woda używana do przygotowania mieszanki betonowej nie powinna zawierać szkodliwych zanieczyszczeń, które zakłócałyby normalne wiązanie i twardnienie cementu. Stosowana jest woda techniczna spełniająca wymagania GOST 23732-79. Całkowita zawartość soli nie przekracza 5000 mg/l, zawartość siarczanów w przeliczeniu na SO 4 nie przekracza 2700 mg/l. Wskaźnik wodorowy pH ˃ 4.
3. Część technologiczna
3.1. Studium wykonalności technologii i metody produkcji
W produkcji wyrobów żelbetowych można stosować różne organizacyjne metody produkcji: przepływowe, przenośnikowe, półprzenośnikowe, ławkowe, kasetowe.
Przy wyborze metody produkcji zazwyczaj przeprowadza się studium wykonalności (TES) przy zadanych kosztach wytworzenia linii.
Metoda produkcji kruszywowo-przepływowej – przy niskich kosztach kapitałowych pozwala na produkcję szerokiej gamy produktów. Operacje technologiczne wykonywane są sekwencyjnie na kilku stanowiskach pracy. Aby zachować konsystencję, forma jest przenoszona z jednego stanowiska na drugie za pomocą suwnicy. Metoda ta najlepiej sprawdza się w warunkach produkcji na małą skalę w fabrykach o średniej i małej wydajności.
Metoda produkcji przenośników - proces technologiczny dzieli się na procesy elementarne, które realizowane są jednocześnie na odrębnych stanowiskach pracy. Formy wraz z wyrobami przemieszczane są ze stanowiska na stanowisko za pomocą specjalnych urządzeń transportowych, każde stanowisko pracy obsługiwane jest przez przypisaną mu jednostkę. Charakterystyczny jest wymuszony rytm pracy, tj. równoczesny ruch wszystkich form po zamkniętym pierścieniu technologicznym z zadaną prędkością.
Metoda produkcji stołowa - produkty formowane są w formach stacjonarnych i utwardzane na miejscu formowania, natomiast urządzenia technologiczne i obsługujące je części robocze przemieszczają się z jednej formy na stole do drugiej. Technologia stołowa jest odpowiednia do produkcji wielkogabarytowych konstrukcji sprężonych o długości ponad 9 metrów dla budynków przemysłowych i cywilnych.
Metoda produkcji kasetowej - formowanie wyrobów odbywa się w pozycji pionowej w stacjonarnych, zdejmowalnych formach-kasetach z grupy metalowej, gdzie wyroby pozostają do czasu uzyskania przez beton wymaganej wytrzymałości. Podczas procesu produkcyjnego pracownicy przemieszczają się od jednej formy kasetowej do drugiej, organizując przepływ produkcji.
3.2. Tryby przetwarzania technologicznego
Produkcja słupów odbywa się metodą stołową w ujednoliconym standardowym przęśle UTP-1 według poniższego schematu funkcjonalnego nr 1. Operacje technologiczne tą metodą produkcji prowadzone są na jednym stanowisku.
W produkcji kolumn proces produkcyjny składa się z następujących operacji:
1. Rozformowanie za pomocą suwnicy;
2. Czyszczenie i smarowanie form specjalnymi smarami;
3. Wzmocnienie i montaż form;
4. Układanie i zagęszczanie mieszanki betonowej za pomocą betoniarki i wibratorów głębokich;
5. Obróbka cieplna i wilgociowa kolumn w temperaturze parowania 80 0;
6. Akceptacja i znakowanie kolumn QC odbywa się zgodnie ze standardami GOST 13015;
7. Wywóz kolumn do magazynu wyrobów gotowych na zasadach zgodnych z GOST 13015.
3.3. Podstawowa produkcja produktu
Schemat funkcjonalny produkcji kolumn
3.4. Charakterystyka urządzeń technologicznych
Suwnica
Rozdzielacz betonu 413-02
Głęboki wibrator IV-79
Wymiary końcówki wibracyjnej, mm: |
|
moc, kW | 0,8 |
Waga (kg | 15 |
Wanna samobieżna BVP-2
Pojemność, m 3 | 2,0 |
Ładowność, t | 5,0 |
Rozmiar otworu wylotowego, mm | 350x600 |
Wymiary, mm: |
|
Waga, t | 0,92 |
Całkowite wymiary instalacji ławki, mm - 12000x4000x70.
Wybrany sprzęt umieszczony jest w znormalizowanej rozpiętości 18 x 144 m. Transport odbywa się za pomocą suwnicy o udźwigu 15 ton.
Powiązanie pracy urządzeń przeprowadzono metodą graficzno-analityczną wykorzystując cyklogram pracy jednostek wiodących. Aby skonstruować cyklogram, najpierw obliczane są elementy cyklu.
Tabela 3
Operacja | Długość skoku, m | Prędkość, m/min | Czas, min |
Ruch mostu: | |||
Zdejmowanie pokrywy | 27,2 | 64 | 1,4 |
Usunięcie formularza | 10 | ||
Zawieszenie, przeniesienie 1 kolumny do magazynu | 9,6 | 40 | 1,2 |
Zawieszenie i przeniesienie drugiej kolumny do magazynu | 4,8 | 40 | 1,1 |
Montaż zbrojenia w pierwszej formie | 4,8 | 40 | 1,1 |
Montaż zbrojenia w drugiej formie | 9,6 | 40 | 1,2 |
Montaż form | 12 | ||
Przesuwanie się za wanną | 8 | 40 | 0,2 |
Wracając do kranu z pustą wanną | 5,6 | 40 | 0,2 |
Zamknięcie stoiska | 29,6 | 64 | 1,5 |
Ruch wózka: | |||
Przeniesienie pierwszej kolumny do magazynu | 20 | 32 | 0,6 |
Przeniesienie drugiej kolumny do magazynu | 14,4 | 20 | 0,5 |
Ruch pierwszego wzmocnienia | 5,6 | 32 | 0,2 |
Ruch drugiego zbrojenia | 11,2 | 32 | 0,4 |
Przesuwanie się za wanną | 30 | 32 | 0,9 |
Wykonany ręcznie: | |||
Czyszczenie i smarowanie form | 24 m2 | 15 | |
Rozdzielacz betonu 413-02 | |||
1. przejazd betoniarki po całej formie | 31,2 | 2,2 | 14,7 |
Drugi przejazd dystrybutora betonu | 31,2 | 2,2 | 16,2 |
Z cyklogramu wynika, że czas trwania cyklu formowania wynosi 77 minut.
3.5. Obliczenia technologiczne
1. Roczną produktywność, m3, określa się według wzoru:
P rok = N st * ∑V ed * K rev * V r
Gdzie P rok to roczna produktywność linii, m 3 / rok
∑V produkt – całkowita objętość produktów w komorze, m 3
K obr – przełożenie obrotów
W p – roczny wymiar czasu pracy – 253 dni.
Budujemy harmonogram prac w celu ustalenia liczby stoisk (N st) i ich wskaźnika obrotów (K obr).
Dla betonu klasy B 22,5 i grubości produktu 400 mm akceptujemy tryb TVO
T TVO = 11(3,5+5+2,5), wówczas liczba kamer:
N o. = 9 szt.,
= 1,33P rok = N st * ∑V ed * K rev * V r = 9 * 3,28 * 1,33 * 253 = 9933,19 m 3
2. Obliczanie magazynu wyrobów zbrojeniowych
Powierzchnia zapasu operacyjnego wyrobów zbrojeniowych na 4 godziny ciągłej pracy
, m 2 - ilość wyprasek na stojaku,A – zużycie stali na produkt,
q – szybkość składowania – 0,080 t/m2.
= 40 m 23. Obliczanie magazynu do przechowywania i chłodzenia produktów na 12 godzin

Gdzie V b.s. – objętość produktów w formie,
q izd – norma składowania, składowania na 1 m 2, przyjmujemy – 0,6.
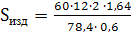
4. Obliczanie formularzy rezerwy.
Liczba formularzy rezerwowych wynosi 5% głównych:
Nf = 1,05(9 * 2) = 18,9
19Formularze rezerwowe – 1 szt.
q f = 0,8 t/m 3 Q f =q f * V artykuł = 0,8 * 1,64 = 1,312 t
∑Q f = 19 * 1,312 = 25 t
5. Dobór składu betonu.
Wybór materiałów:
Cement portlandzki według GOST 10178 dla klasy B 22,5 według SNiP 5.01.23 zalecany gatunek cementu M 400, R c = 400 kg/cm 2, R b = 300 kg/cm 3, ρ c = 3 g/cm 3, ρ n.ts. = 1,2 kg/dm3.
Zwykły kruszony kamień o gęstości nasypowej ρ n.p. = 1,4 kg/dm 3, ρ = 2,65 g/cm 3,
= 0,47Piasek – kwarc o module rozdrobnienia Mk = 2, ρ n.p. = 1,6 kg/dm 3, ρ p = 2,67 g/cm 3.
6. Obliczanie składu.
Z warunku wytrzymałościowego znajdujemy stosunek C/V
= 1,75Korzystając z tabeli, określamy przybliżone zużycie wody na 1 m 3 mieszanki betonowej. Zużycie wody wynosi B = 200 l.
Zużycie cementu wyniesie C = 200 * 1,75 = 350 kg.
1. Suma bezwzględnych objętości składników mieszanki betonowej wynosi 1 m 3 lub 1000 litrów.

2. Przestrzeń pomiędzy ziarnami tłucznia wypełnia się zaprawą cementowo-piaskową o zadanej ekspansji kruszywa grubego
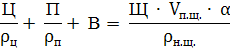
Określanie zużycia kruszonego kamienia


Współczynnik rozszerzalności kruszonych ziaren kamienia określa się w zależności od zużycia cementu i stosunku wody do cementu zgodnie z tabelą.
W/C = 200/350 = 0,57
Zużycie piasku określa się według wzoru
Suma bezwzględnych objętości składników mieszanki betonowej jest równa
Skład nominalny na 1 m 3 mieszanki betonowej
W wyniku obliczeń otrzymujemy nominalny (laboratoryjny) skład mieszanki betonowej na 1 m 3. Jednakże w warunkach produkcyjnych należy uwzględnić wilgotność kruszywa. Dlatego ponownie obliczamy zużycie piasku, kruszonego kamienia i wody zarobowej i określamy skład roboczy mieszanki betonowej.
Akceptujemy wilgotność piasku i tłucznia
W p = 5%, W p = 2%.
l.Gęstość mieszanki betonowej określa się według wzoru
W procesie przygotowania mieszanki betonowej za pomocą betoniarek o różnej pojemności, mieszanka ulega zagęszczeniu dzięki zastosowaniu grubego kruszywa. W rezultacie objętość przygotowanej mieszanki betonowej będzie mniejsza niż pierwotna objętość przed wymieszaniem składników.
Współczynnik wyjściowy β
3.6 Projekt BSO
Wyposażenie betoniarni dobierane jest na podstawie wydajności godzinowej lub zapotrzebowania zmianowego na mieszankę betonową. Projekt warsztatu w ten projekt nie jest brany pod uwagę, ponieważ zapotrzebowanie odlewni na mieszankę betonową będzie niskie. Ilość mieszanki betonowej zależy od średniej wydajności.
3.7 Zapotrzebowanie produkcyjne na surowce i zasoby energetyczne
Obliczając roczne zapotrzebowanie na surowce i materiały eksploatacyjne bierzemy pod uwagę możliwe straty produkcyjne podczas transportu mieszanki betonowej. Zapotrzebowanie na mieszankę betonową, m 3 /rok
P rok = P rok * P
gdzie P rok to roczna produktywność dwóch linii, m 3;
P - straty produkcyjne mieszanki betonowej – 1,5%
P rok = 9933,19 x 1,015 = 10082,19 m 3
Zapotrzebowanie produkcyjne na surowce i zasoby energetyczne
Tabela 4
Zapotrzebowanie na energię elektryczną produkcji
Tabela 5
Roczne zapotrzebowanie na energię elektryczną
P rok = 35,8 * 253 * 16 = 144918,4 kW
Zużycie energii elektrycznej na 1 m 3
Q = 144918,4/9933,19 = 14,6 kW/m3
3.8 Magazyn wyrobów gotowych
F=(P rok *N ho /(B p *g h))*K 1 *K 2
gdzie F to powierzchnia magazynu, m2;
A - stan towaru w magazynie (przyjmowany 10 dni);
g n - objętość produktów m 3 ułożonych na 1 m 2 powierzchni magazynu = 0,5
K 1 - współczynnik uwzględniający przejścia pomiędzy stosami produktów = 1,5
K 2 - współczynnik uwzględniający powierzchnię przejazdu pojazdu = 1,3
F=((9933,19*10)/(253*0,5))*1,5*1,3=1531,20 m 2
3.9 Lista personelu
Tabela 6
Nazwa zawodu | Liczba osób | |
1. zmiana | 2. zmiana | |
A. Pracownicy produkcyjni | ||
1. Formierka | 1 | 1 |
2. Operator dźwigu | 2 | 2 |
3. Operator układarki | 1 | 1 |
4. Parowiec | 1 | 1 |
Szalunki | 3 | 3 |
Wzmocnienie | 4 | 4 |
Czyszczenie, smarowanie | 2 | 2 |
Całkowity | 14 | 14 |
B. Pracownicy pomocniczy | ||
1. Ślusarz | 2 | 2 |
2. Elektryk | 1 | 1 |
3. Kontroler OTC | 1 | 1 |
4. Asystent laboratoryjny | 1 | 1 |
Całkowity | 5 | 5 |
B. Personel sklepu | ||
1. Kierownik warsztatu | 1 | - |
2. Mistrz zmiany | 1 | 1 |
3. Mechanik | 1 | - |
4. Energia | 1 | - |
5. Standaryzator | 1 | - |
6. Magazynier | 1 | - |
Całkowity | 6 | 1 |
Razem za warsztat | 25 | 20 |
Na trzeciej zmianie dyżur pełni 1 parowiec.
Łączna liczba pracowników wynosi 45 osób.
3.10 Kontrola jakości produktu i dokładności procesu
Przy produkcji prefabrykowanych wyrobów żelbetowych kontrola techniczna prowadzona jest na różnych etapach procesu technologicznego. W zależności od tego rozróżnia się kontrolę wejściową, operacyjną i akceptacyjną.
Kontrolę produkcji prowadzi personel techniczny sklepu, który odpowiada za zgodność z wymaganiami technologicznymi stawianymi produktom. Dział kontroli technicznej (QC) przedsiębiorstwa kontroluje jakość i odbiera gotowe produkty, sprawdza zgodność technologii Specyfikacja techniczna produkcja produktów.
Do zadań kontroli produkcji należy: kontrola jakości materiałów i półproduktów otrzymywanych przez przedsiębiorstwo – kontrola przychodząca; kontrola nad realizacją procesów technologicznych, prowadzona podczas wykonywania określonych operacji zgodnie z ustalonymi trybami, instrukcjami i mapy technologiczne- kontrola operacyjna; kontrola jakości i kompletności wyrobów, zgodności z normami i specyfikacjami technicznymi – kontrola odbiorów.
Kontrola wytrzymałości betonu
Podczas produkcji prefabrykowanych konstrukcji żelbetowych należy kontrolować projektowy stopień wytrzymałości betonu na ściskanie, wytrzymałość betonu na odpuszczanie i wytrzymałość na przenoszenie konstrukcji sprężonych.
Metody kontroli siły mogą się różnić. Stopień projektowy betonu określa się poprzez badanie próbek kontrolnych pod kątem zniszczenia, stopień odpuszczania lub przenoszenia określa się poprzez badanie próbek kontrolnych lub metodami nieniszczącymi.
Przy monitorowaniu wytrzymałości betonu metodami nieniszczącymi kontrolowane jest co najmniej 10% partii i co najmniej trzy próbki, a liczba kontrolowanych obszarów w partii musi wynosić co najmniej 9.
We wszystkich przypadkach kontroli siła przenoszenia musi wynosić co najmniej 50% przyjętej klasy projektowej. Jeżeli podczas badania próbek średnia wytrzymałość jest niższa od wymaganej, badania należy powtórzyć metodami nieniszczącymi. Jeżeli w tym przypadku wytrzymałość betonu jest niższa niż wymagana, należy prowadzić badania ciągłe metodami nieniszczącymi.
Kontrolując jakość osadzonych części i produktów wzmacniających, sprawdzane są wymiary geometryczne, wygląd i jakość połączeń spawanych. Wymiary geometryczne obejmują: wymiary, odległość pomiędzy prętami zewnętrznymi na długości, wysokości i szerokości wyrobów, odległość pomiędzy prętami, pomiędzy elementami osadzonych części i ich względnym położeniem, płaskość osadzonych części, wymiary spawanych połączeń, wielkość i ilość porów zewnętrznych oraz inne wady spawalnicze.
Po zbadaniu wygląd odnotować brak rdzy, zgorzeliny, śladów oleju, bitumu itp. Jakość złączy spawanych sprawdza się za pomocą badań mechanicznych lub badań ultradźwiękowych.
Przyjmowanie wyrobów zbrojeniowych odbywa się partiami o tej samej standardowej wielkości. Partia przyjmowana jest na podstawie wyników poboru próbek co najmniej trzech produktów. Standardy kontroli ustala GOST 10922-75.
Kontrola akceptacji
Kontrola odbioru prefabrykowanych wyrobów żelbetowych polega na sprawdzeniu ich wytrzymałości, sztywności i odporności na pękanie oraz odbiorze w oparciu o zestaw wskaźników jakości, na podstawie których podejmowana jest decyzja o zgodności wyrobu lub partii wyrobów z wymaganiami GOST.
Wytrzymałość, sztywność i odporność na pękanie sprawdza się zgodnie z GOST 8829-77 poprzez badanie próbek obciążenie zewnętrzne przed zniszczeniem lub przy użyciu metod nieniszczących. Próby obciążeniowe przeprowadza się przed rozpoczęciem masowej produkcji konstrukcji, przy zmianie technologii oraz podczas produkcji najbardziej krytycznych konstrukcji (formy, belki, płyty sprężone o rozpiętości większej niż 9 m). Do masowej produkcji wewnętrznych paneli ściennych budynki wielkopłytowe, płyty płaskie, kanałowe, żebrowane itp., a także konstrukcje, których badanie obciążeniowe jest trudne (np. słupy, prefabrykowane konstrukcje monolityczne), należy stosować metody nieniszczące.
Próby obciążeniowe konstrukcji należy wykonywać zgodnie z normami i rysunkami wykonawczymi na specjalnie wyposażonych stanowiskach, przy dodatnich temperaturach powietrza. Konstrukcja oraz urządzenia załadowcze montowane są na stojaku zgodnie ze schematem podanym na rysunkach wykonawczych. Warunki podparcia konstrukcji na podporach i trawersach rozdzielczych na konstrukcji muszą spełniać wymagania GOST 8829-77.
Podczas badań metodami nieniszczącymi decyzję o zgodności partii konstrukcji z wymaganiami wytrzymałości, sztywności i odporności na pękanie podejmuje się na podstawie danych i pojedynczych wskaźników jakości konstrukcji uzyskanych w procesie przychodzącym, kontrola operacyjna i odbiorcza.
Kontrolowane indywidualne wskaźniki jakości obejmują rodzaj, klasę, gatunek, właściwości mechaniczne stali zbrojeniowej, jakość wyrobów zbrojeniowych, średnicę, ilość i lokalizację zbrojenia, grubość warstwy ochronnej betonu, rozciąganie zbrojenia, wymiary geometryczne kształtowników, przenoszenie i odpuszczanie wytrzymałość betonu.
Wytrzymałość betonu w konstrukcjach określa się metodami nieniszczącymi. Sterowanie położeniem zbrojenia i grubością warstwy ochronnej bezpośrednio w konstrukcjach odbywa się metodą magnetyczną (za pomocą urządzeń typu IZS).
Wymiary geometryczne mierzone są z dokładnością ±1 mm.
Wyniki kontroli odbiorczej, dane kontroli przychodzącej i operacyjnej dotyczące wskaźników jakości są rejestrowane w specjalnych dziennikach.
Operacyjna kontrola jakości głównych procesów technologicznych.
Podstawowe operacje podlegające kontroli | Kompletny zestaw rysunków roboczych, specyfikacji, map | Stan formularzy. oprzyrządowanie, manometry, urządzenia napinające, wibratory | Przygotowanie mieszanki betonowej | Przygotowanie i smarowanie palet | Układanie mieszanki betonowej | HME i warunki hartowania | Rozbiórka. Przygotowanie do dostawy produktów, magazynowanie |
Skład kontroli | Dostępność dokumentacji technicznej (TU), rysunków roboczych itp. | 1. Wibracje podkładek wibracyjnych 2. Kalibracja manometrów 3. Tabele kalibracyjne 4. Stan techniczny urządzeń |
1. Dokładność dozowania 2. Czas mieszania 3. Spójność 4. Temperatura |
1. Zgodność kształtów z wymiarami projektowymi 2.Jakość czyszczenia i smarowania palet 3. Jakość emulsji |
1. Grubość warstwy 2. Czas zagęszczania wibracyjnego 3. Gęstość układania 4. Wytrzymałość betonu 5. Masa masowa |
Zgodność z określonym reżimem TVO | 1. Wygląd 2. Obecność wad 3. Zgodność lokalizacji produktów ze schematem magazynowania |
Miejsce kontroli | Sklep | Stanowiska formujące i napinające Laboratorium | Dozowniki. Betoniarki | 1. Po wyścigach taras 2. Miejsce montażu przed ułożeniem mieszanki betonowej |
odlewanie 4-5. Laboratorium |
parowanie |
Stacja striptizowa. Magazyn wyrobów gotowych |
Metoda i środki kontroli | Porównanie z listą projektów | Porównanie ze standardowymi manometrami i dynamometrami. Wibrograf. Paszport | 1. Obserwacja urządzeń 2. Sprawdzanie i kalibracja urządzeń 3. Pobieranie próbek i badanie 4.Termometr |
1. Zmierz taśmą mierniczą i poziomicą. 3. Pobieranie próbek i badanie |
1. Zmierz linijką 2. Stoper 3. Miernik gęstości 4-5. Pobieranie próbek i późniejsze badania |
automatyzacja i rozporządzenie UKB-1 |
1-2. Wizualny 3. Taśma miernicza stalowa, schemat |
Częstotliwość i zakres kontroli | Raz w miesiącu przy wytwarzaniu nowej partii wyrobów |
2.3. Po 6 miesiącach każde urządzenie 1.4. Miesięczny |
1. Raz na zmianę 2. Każdy pomiar 3-4,2 razy na zmianę i przy nowym składzie mieszanki |
1. Raz na kwartał. Kawałek po kawałku. 2. Raz na zmianę. Próbka 3. Raz w miesiącu |
1.2. Kawałek po kawałku. 3.5. Raz na zmianę. 4,5. Seria kostek kontrolnych |
W trakcie przetwarzanie godziny. Impreza w celi |
1.2. Kawałek po kawałku 3,2 razy na zmianę. |
Osoba nadzorująca operację | Inżynier VET | 1. Mistrz otwierania 2. Mechanik 3. Energia |
1-4. Asystent labolatoryjny 2. Operator |
1. Mistrz kontroli jakości 3. Asystent laboratoryjny |
1.2. Mistrz Kontroli Jakości 3-5. Asystent labolatoryjny |
Asystent labolatoryjny |
Brygadier |
Osoba odpowiedzialna za zapewnienie technologia pieczenia |
Kierownik działu | Kierownik działu Główny inżynier mechanik Główny inżynier energetyk |
Głowa laboratorium. Kierownik betoniarni - | Majster | Szef warsztaty Głowa laboratorium |
Głowa laboratorium. Kierownik elektrowni parowej | Majster |
4. Bezpieczeństwo i higiena pracy
Projektując i eksploatując przedsiębiorstwa prefabrykatów betonowych, aby zapewnić bezpieczne i normalne warunki sanitarno-higieniczne pracy, należy kierować się obowiązującymi przepisami bezpieczeństwa i higieny przemysłowej, a także przepisami bezpieczeństwa obowiązującymi w każdym danym dziale, które zawierają wymagania dla całego przedsiębiorstwa, jego poszczególnych warsztatów, procesów technologicznych, urządzeń transportowych i urządzeń wibracyjnych, przyczyniając się do obniżenia poziomu hałasu oraz poprawy sanitarno-higienicznych warunków pracy, a także regulowanych standardów naturalnych i Sztuczne oświetlenie pomieszczeń, ich ogrzewanie i wentylację.
Zapewnienie zdrowego i bezpieczne warunki praca jest przydzielona do administracji przedsiębiorstwa. Administracja ma obowiązek wdrożyć nowoczesne środki ostrzeżenie dotyczące środków bezpieczeństwa urazy przemysłowe oraz zapewniać warunki sanitarno-higieniczne zapobiegające występowaniu chorób zawodowych pracowników i pracowników.
Administracja zakładu jest zobowiązana do prowadzenia prac organizacyjnych w celu zapewnienia bezpiecznych i higienicznych warunków pracy (planowanie i finansowanie różnych środków ochrony pracy, instruowanie pracowników i pracowników w zakresie środków bezpieczeństwa i higieny przemysłowej). W prawie pracy szczególną uwagę zwraca się na przestrzeganie wymogów ochrony pracy już na etapie projektowania i rozwoju nowych przedsiębiorstw, maszyn i procesów technologicznych.
W warsztatach, w których ze względu na potrzeby technologiczne bramy w obiekcie są otwarte przez dłuższy czas i wykluczona jest możliwość zamontowania przedsionków i śluz powietrznych, należy przewidzieć montaż kurtyn powietrznych w następujących przypadkach:
a) przy bramach lokali otwartych na co najmniej 40 minut w ciągu jednej zmiany, a także w budynkach położonych na obszarach o przewidywanej temperaturze powietrza -20 C i niższej;
b) gdy niedopuszczalne jest obniżenie temperatury powietrza w lokalu w stosunku do wskazanej powyżej ze względu na warunki technologiczne lub sanitarno-higieniczne, niezależnie od czasu otwarcia bramy i przewidywanej temperatury powietrza zewnętrznego.
W budynkach produkcyjnych i pomocniczych, niezależnie od stopnia zanieczyszczenia powietrza, należy zapewnić wentylację naturalną lub wymuszoną. Aby zapobiec zanieczyszczeniu powietrza w pomieszczeniach pracy szkodliwymi emisjami i ich rozprzestrzenianiem się, należy podjąć następujące środki:
urządzenia, przyrządy, rurociągi i inne źródła znacznego wydzielania ciepła konwekcyjnego lub promieniowania muszą być izolowane termicznie;
sprzęt i urządzenia wytwarzające wilgoć podczas pracy powinny być bezpiecznie przykryte;
procesy charakteryzujące się znaczną emisją pyłów muszą być izolowane i prowadzone bez bezpośredniego udziału ludzi; sprzęt lub jego części będące źródłem emisji pyłu muszą być w miarę możliwości przykryte i uszczelnione;
Emisje technologiczne uwalniane z urządzeń w postaci pyłów, porów i szkodliwych gazów muszą zostać skutecznie oczyszczone przed uwolnieniem do atmosfery.
W formiearniach i innych pomieszczeniach, w których stosowane są mechanizmy wibracyjne, należy zwrócić szczególną uwagę na wyeliminowanie wpływu wibracji na pracowników i zmniejszenie poziomu hałasu.
We wszystkich przypadkach, gdy poziom hałasu i wibracji na stanowiskach pracy przekracza dopuszczalne wartości, należy podjąć działania mające na celu ich obniżenie do normalnego poziomu poprzez montaż izolacji akustycznej i wibracyjnej pomieszczeń, stanowisk pracy i maszyn oraz stosowanie środków ochrony indywidualnej pracowników:
a) montaż platform wibracyjnych i stołów wibracyjnych na masywnych fundamentach, odizolowanych od podłoża i na obwodzie za pomocą elastycznych uszczelek;
b) montaż maszyn z mechanizmami wibracyjnymi na wibroizolatorach sprężynowych lub gumowych;
c) izolacja paneli kontrolnych i kabin obserwacyjnych od działania mechanizmów wibracyjnych;
e) obowiązkowe mocowanie form na platformach wibracyjnych i stołach udarowych;
f) pokrycie platform wibracyjnych osłonami akustycznymi oraz zamontowanie wiaty dźwiękochłonnej pod stoły uderzeniowe i wyłożenie odbiorników materiałami dźwiękochłonnymi;
g) umieszczanie źródeł hałasu w izolowanych pomieszczeniach lub zakrywanie stanowisk pracy z mechanizmami wibracyjnymi obudową dźwiękochłonną;
h) terminowe przeglądy zapobiegawcze, naprawy i regulacja urządzeń wibracyjnych.
Jako ochronę osobistą przed wibracjami i hałasem należy stosować specjalne buty z grubą podeszwą z gumy gąbczastej, rękawiczki z piankową wyściółką i słuchawki wygłuszające (antyfony).
W cementowniach i betoniarniach do strącania pyłu stosuje się odśrodkowe odpylacze typu NIIOGAZ, które wychwytują od 70 do 90% pyłu. Docelowo powietrze oczyszczane jest z pyłów za pomocą filtrów tkaninowych FR-30, F^-60, FR-90.
Do indywidualnej ochrony pracowników przed wysokimi stężeniami pyłów zaleca się stosowanie półmasek F-45, F-46, szczelnych okularów ochronnych oraz odzieży ochronnej z tkaniny pyłoszczelnej.
Aby zapewnić bezpieczne warunki pracy i zapobiec urazom na głównych etapach technologicznych, należy przestrzegać następujących wymagań:
podczas obsługi maszyn prostująco-tnących oraz maszyn do czyszczenia i prostowania zbrojenia prętów należy podłączyć ich obudowę do lokalnego systemu zasysania;
Na prace spawalnicze uziemiać spawarki, izolować przewody, chronić oczy pracowników okularami i osłonami z filtrami świetlnymi, układać maty gumowe lub drewniane kraty na stanowiskach pracy, włączać wentylację wyciągową dla spawarek i zabezpieczać stanowiska spawalnicze ekranami ochronnymi;
Przy produkcji mieszanek betonowych należy przeprowadzać okresowe przeglądy profilaktyczne i naprawy instalacji wentylacyjnej, monitorować szczelność kabin sterujących mieszalników i dozowników, dobry stan instalacji alarmowej wskaźników poziomu, wyłączników dachowych i innych urządzeń automatyki, naprawiać mieszalniki po demontażu bezpieczniki z instalacji elektrycznej i zainstalowanie sygnału uniemożliwiającego włączenie maszyny. ;
Podczas napinania zbrojenia metodą elektrotermiczną należy układać i usuwać nagrzane pręty przy wyłączonym prądzie, włączać lampę sygnalizacyjną na czas działania prętów, instalować daszki ochronne na podporach form mocy;
Podczas formowania należy włączyć alarm dźwiękowy przy uruchamianiu betoniarek samojezdnych lub maszyn do rozbierania kaset, wykonywać zdalne sterowanie maszynami formierskimi, w tym kasetami z platform wibroizolowanych;
Podczas obróbki cieplnej należy zadbać o to, aby nie doszło do wycieku pary przez nieszczelności ścian komór, zaworów hydraulicznych komór i rurociągów, załadunek i rozładunek produktów z komór za pomocą trawersów automatycznych oraz zabezpieczenie pomostów spacerowych pomiędzy komorami dojrzewalniczymi.
Aby zapewnić spełnienie wymagań bezpieczeństwa pożarowego, konieczne jest:
Podczas stawiania tymczasowych budynków i konstrukcji należy zachować między nimi rezerwy ogniowe, aby uniknąć przeniesienia ognia;
Zapewnić dojazd wozu strażackiego do dowolnego obiektu zakładu;
Do gaszenia pożarów należy wykorzystywać sieci wodociągowe, dla których we wszystkich sieciach należy przewidzieć punkty poboru wody przeciwpożarowej;
Wszystkie obiekty należy wyposażyć w podstawowe środki gaśnicze.
We wszystkich pomieszczeniach produkcyjnych, domowych i administracyjnych, w przypadku pożaru, musi istnieć możliwość bezpiecznej ewakuacji ludzi poprzez wyjścia awaryjne.
5. Techniczne i ekonomiczne wskaźniki produkcji
Techniczną i ekonomiczną efektywność produkcji ocenia się za pomocą następujących wskaźników:
Roczna produktywność, m 3
Rok P = 9933,19
Powierzchnia produkcyjna, m 2
S = 18 x 144 = 2592
Usuwanie produktu z 1 m 2 powierzchni produkcyjnej, m 3 / m 2
C F =9933,19/1531,2 =6,49 m3/m2
Pojemność komór parowych, m 3;
ΣV K = (12*4*0,7)* 9 = 302,4
Usuwanie produktu z 1 m 3 komór parowych rocznie, m 3;
C k = 9933,19/302,4 = 32,85
Liczba pracowników produkcyjnych wynosi 30 osób;
Pracochłonność wytworzenia 1 m 3 produktów, osobogodziny;
T y = (30*16*253)/(9933,19*2)=6,11 m 3 /osobę
Całkowita masa wyposażenia technicznego, t
ΣM = (1,312 * 19)+15+15+6,4+0,015+0,92 =62,26
Specyficzne zużycie metalu do produkcji, kg/m 3 ;
U m = 62260/9933,19 = 6,27
Jednostkowe zużycie (na 1 m 3 produktu):
Cement -350 kg;
Stal – 521,8 kg;
Para - 300 kg;
Energia elektryczna – 14,6 kW/h.
6. Wykorzystana literatura
1. komp. Medwedko SV. Wytyczne na projekt kursu w dyscyplinie „Projektowanie przedsiębiorstw do produkcji materiałów, wyrobów i konstrukcji budowlanych”, VolgGASA. - Wołgograd, 2000. - 36 s.
2. wyd. Podręcznik K. V. Mikhailova „Produkcja wyrobów z betonu zbrojonego”, - wyd. 2, poprawione. i dodatkowe - M.: Stroyizdat, 1989. - 447 s., il.
3. Bazhenov Yu.M., Komar A.G. „Technologia wyrobów betonowych i żelbetowych”, podręcznik dla uczelni wyższych. - M.: Stroyizdat, 1984. - 672 s., il.
1. GŁÓWNE SCHEMATY TECHNOLOGICZNE PRODUKCJI
Wyroby i konstrukcje betonowe i żelbetowe produkowane są w specjalnych fabrykach lub na poligonach doświadczalnych. Na proces technologiczny składają się następujące sekwencyjne operacje: przygotowanie mieszanki betonowej, produkcja zbrojenia i klatek zbrojeniowych, zbrojenie wyrobów żelbetowych, formowanie, obróbka cieplno-wilgotnościowa oraz dekoracyjne wykończenie przednia powierzchnia produktów. Zewnętrzne panele ścienne w zależności od projektu mogą zostać poddane dodatkowej operacji – wmurowaniu w panel materiał termoizolacyjny podczas montażu pojedynczych skorup lub produktów formierskich.
Organizacja realizacji tych podstawowych operacji technologicznych i ich projekt techniczny w nowoczesna technologia prefabrykaty żelbetowe wykonywane są w trzech schematy obwodów, a cechą wiodącą jest sposób formowania produktów. Przedsiębiorstwa wyróżniają się także metodami formowania, na przykład instalacja kasetowa, instalacja przenośnikowa lub instalacja z technologią agregatów przepływowych. Wybierając technologię produkcji należy wziąć pod uwagę możliwość uzyskania jak najlepszej kontroli nad kształtowaniem się struktury mieszanki betonowej.
W oparciu o metodę i organizację procesu formowania można wyróżnić trzy schematy produkcji wyrobów żelbetowych.
1. Produkcja wyrobów w postaciach nieruchomych. Wszyscy technolodzy
operacje techniczne - od przygotowania form po rozbiórkę gotowych materiałów
naszych produktów – realizowane są w jednym miejscu. Ta metoda dotyczy
formowanie wyrobów na stojakach płaskich lub w matrycach, „forma
przechowywanie produktów w kasetach.
2. Wytwarzanie wyrobów w formach ruchomych. Indywidualne techno
logiczne operacje formowania lub oddzielny kompleks do ich przeprowadzania
są zatrudnieni na specjalistycznych stanowiskach. Ukształtuj, a następnie połącz produkt
z formularzem przenoszone są z postu na post w miarę realizacji poszczególnych zadań
operacje.
W zależności od stopnia rozbioru ogólnego kompleksu technologicznego wyrobów formierskich na poszczególnych stanowiskach rozróżnia się metody przenośnikowe, które charakteryzują się największym rozwarstwieniem, oraz metody agregatów przepływowych. Ten ostatni różni się tym, że wiele operacji (układanie zbrojenia i mieszanki betonowej, zagęszczanie mieszanki, a w niektórych przypadkach szereg innych) wykonuje się na jednym słupku. W przypadku metody przenośnikowej większość operacji formowania odbywa się na konkretnym stanowisku; tworzą linię produkcyjną.
3. Formowanie ciągłe, które pojawiło się stosunkowo niedawno, ale
wysoka wydajność pracy, minimalne zużycie metalu i nie
stosunkowo wysoki wolumen produkcji na jednostkę powierzchni produkcyjnej
oszczędzić przedsiębiorstwo. Prowadzona jest metoda ciągłego formowania produktów
odlewany jest na walcarce wibracyjnej.
2. WZMOCNIENIE WYROBÓW ZBETONOWYCH
W produkcji fabrycznej koszt zbrojenia stanowi około 20% kosztu wyrobów żelbetowych, dlatego organizacja prac zbrojeniowych w wytwórni prefabrykatów betonowych jest najważniejsza zarówno pod względem technicznym, jak i ekonomicznym. Rozróżnia się zbrojenie niesprężone (zwykłe) i sprężone wyrobów żelbetowych. Operacje zbrojeniowe i rodzaje zbrojenia dla każdej z tych metod mają wiele zasadniczych różnic.
Nienaprężone zbrojenie
Zbrojenie wyrobów żelbetowych zbrojeniem niesprężonym odbywa się za pomocą płaskich siatek i przestrzennych (objętościowych) ram wykonanych z prętów stalowych o różnych średnicach, zespawanych ze sobą na skrzyżowaniach. Istnieją okucia robocze (główne) i instalacyjne (pomocnicze). Zbrojenie robocze znajduje się w tych miejscach produktu, w których powstają naprężenia rozciągające pod obciążeniem; armatura je dostrzega. Zbrojenie montażowe znajduje się w ściśniętych lub nienaprężonych obszarach produktu. Oprócz tego rodzaju okuć stosuje się pętle i haczyki niezbędne przy operacjach załadunku, a także elementy osadzone, mocowania i połączenia elementów prefabrykowanych. Najniższe koszty pracy przy wzmacnianiu wyrobów i konstrukcji występują przy zastosowaniu ram zbrojeniowych o najwyższym stopniu gotowości, tj. Posiadających nie tylko zbrojenie główne, ale także zbrojenie pomocnicze ze spawanymi zawiasami, hakami i osadzonymi częściami. W tym przypadku operacje wzmacniające ograniczają się do zainstalowania gotowej ramy wzmacniającej w formie i jej zabezpieczenia.
Siatki i ramy zbrojeniowe produkowane są w zbrojowni wyposażonej w maszyny do cięcia, gięcia i zgrzewania. Proces produkcyjny zbudowany jest na zasadzie jednego przepływu technologicznego – od przygotowania stali zbrojeniowej do odbioru gotowego produktu.
Siatki i ramy wzmacniające wykonywane są zgodnie z rysunkami roboczymi, które wskazują długość i średnicę prętów, ich liczbę, odległości między nimi, miejsce spawania osadzonych części oraz położenie pętli montażowych. Konieczne jest bardzo dokładne zamontowanie i zamocowanie ramy w formie, ponieważ grubość warstwy ochronnej betonu w produkcie zależy od jego położenia. Jeżeli grubość tej warstwy będzie niewystarczająca, może dojść do korozji stali zbrojeniowej.
Pręty ze stali zbrojeniowej o średnicy do 10 mm dostarczane są do zakładu w kręgach (kręgach), a o większej średnicy - w prętach o długości 6-12 m lub długości mierzonej określonej w zamówieniu; drut wzmacniający jest dostarczany w zwojach, przy czym każda cewka składa się z jednego kawałka drutu.
Operacje wytwarzania zbrojenia są następujące: przygotowanie drutu i pręta stalowego – czyszczenie, prostowanie, cięcie, łączenie, gięcie;
montaż prętów stalowych w postaci siatek płaskich i ram;
produkcja objętościowych ram wzmacniających, w tym spawanie pętli montażowych, elementów osadzonych i zacisków.
Przygotowanie zbrojenia docierającego do zakładu w kręgach i kręgach polega na rozwijaniu, prostowaniu (prostowaniu), oczyszczaniu i cięciu na pojedyncze pręty o zadanej długości. Prostują i tną stal zbrojeniową na automatycznych maszynach do prostowania i cięcia.
Stal zbrojeniową pręty tnie się na pręty o określonej długości, a także łączy poprzez spawanie (w celu ograniczenia odpadów zbrojeniowych w przypadku, gdy długość elementów wzmacniających nie odpowiada długości produktu handlowego). Łączenie prętów odbywa się za pomocą zgrzewania doczołowego elektrycznego i tylko w niektórych przypadkach (w przypadku stosowania prętów o dużych średnicach) za pomocą zgrzewania łukowego. Zgrzewanie doczołowe kontaktowe odbywa się poprzez stopienie końców prętów w miejscach ich przyszłego połączenia prądem elektrycznym, gdy pręty są silnie ściśnięte i zespawane.
Przy produkcji pętli montażowych, zacisków i innych kształtowych elementów wzmacniających, stal zbrojeniowa z prętów i drutu jest po cięciu wyginana.
Siatki i ramy wykonane ze stalowych prętów zbrojeniowych łączone są metodą punktowego zgrzewania elektrycznego. Jego istota jest następująca. Kiedy mijasz prąd elektryczny przez dwa przecinające się pręty w punktach ich styku opór elektryczny jest największy, pręty nagrzewają się i po osiągnięciu stanu plastycznego są spawane. Silne ściskanie prętów również przyczynia się do wytrzymałości spoiny. Proces zgrzewania punktowego może trwać ułamek sekundy przy przyłożeniu prądu o natężeniu kilkudziesięciu tysięcy amperów. Zgrzewanie punktowe odbywa się za pomocą specjalnych zgrzewarek. Różnią się mocą transformatora, liczbą jednocześnie zgrzewanych punktów (urządzenia jedno- i wielopunktowe) oraz rodzajem urządzeń stosowanych do ściskania spawanych prętów.
Zgrzewarki umożliwiają tworzenie, w połączeniu z innymi maszynami i instalacjami, automatycznych linii produkcyjnych do produkcji siatek płaskich, zarówno gotowych elementów zbrojeniowych, jak i półproduktów do ram przestrzennych. Na ryc. 75 przedstawia automatyczną linię do zgrzewania szerokich oczek. W ofercie znajdują się uchwyty do zamieszek grupowych do zasilania wzdłużnego i poprzecznego, prawidłowe urządzenia, zgrzewarkę MTMS z urządzeniem do cięcia, nożyce pneumatyczne do poprzecznego cięcia siatki, słupki do zgrzewania osadzonych elementów oraz urządzenia do zacisków; Przewidziano elektromagnetyczny układ programowania zasilania prętów poprzecznych i dodatkowych podłużnych. Realizacja in-line wszystkich operacji produkcji siatki zbrojeniowej krajowej linii produkcyjnej znacznie zmniejsza pracochłonność procesu w porównaniu do modyfikacji siatki na przewodnikach, która zwykle wykonywana jest ręcznie.
Ramy zbrojenia przestrzennego wykonywane są głównie z siatek płaskich łączonych ze sobą za pomocą specjalnych zgrzewarek. Ramy można montować w pozycji poziomej i pionowej. Dla wygody łączenia węzłów za pomocą szczypiec do zgrzewania punktowego stosuje się pionowy przyrząd (ryc. 76). Pomiędzy kołkami przewodzącymi umieszczone są płaskie elementy wzmacniające, które utrzymują je w żądanym położeniu. Kleszcze spawalnicze zawieszone są na obrotowej konsoli; Przewód wraz z osprzętem można przesuwać w górę i w dół za pomocą wciągarki. Niektóre elementy przewodnika są połączone ze sobą za pomocą śrub. Pozwala to na wykorzystanie tego samego szablonu do montażu różnych ram wzmacniających, zabezpieczając ich elementy zgodnie z rozmiarem montowanej ramy. W razie potrzeby (np. w przypadku płyt żebrowanych) siatki i ramy płaskie można wygiąć na wymiar na specjalnych giętarkach.
Wzmocnienie zestresowane
Przy wytwarzaniu wyrobów sprężonych konieczne jest wytworzenie wstępnego sprężania w betonie na całym przekroju lub tylko w strefie naprężeń rozciągających, których wartość przekracza naprężenia rozciągające występujące w betonie podczas eksploatacji. Stopień wstępnego zagęszczenia osiąga zwykle 50-60 kg/cm2, a przy produkcji żelbetowych rur ciśnieniowych - 100-120 kg/cm2. Zaciskanie betonu odbywa się za pomocą sił sprężystego efektu rozciąganego zbrojenia. Osiąga się to poprzez siły przyczepności zbrojenia do betonu lub za pomocą urządzeń kotwiących. Aby zapewnić ściskanie betonu, zastosowana stal zbrojeniowa musi mieścić się w granicach odkształcenia sprężystego i nie przekraczać 85-90% granicy plastyczności stali, a dla stali węglowych, które nie mają jasno określonej granicy plastyczności, 65-70 % wytrzymałości na rozciąganie.
Głównym zbrojeniem sprężającym jest stal zbrojeniowa z drutów i prętów o wysokiej wytrzymałości, stal zbrojeniowa walcowana na gorąco klasy A-IV oraz stal zbrojeniowa klasy A-H1v, wzmacniana metodą ciągnienia. Wybór rodzaju zbrojenia zależy od rodzaju produktu i rodzaju zbrojenia użytego do naprężenia zbrojenia. Jako pomocnicze zbrojenie nierozciągliwe, jeśli jest taka potrzeba w wyrobach sprężonych, stosuje się je, jak w przypadku zwykłego żelbetu, Spawana siatka i ramki.
W produkcji wyrobów sprężonych stosuje się jednoosiowe ściskanie betonu za pomocą pojedynczych prętów lub wiązek drutów umieszczonych w wyrobie wzdłuż jego osi podłużnej, a ściskanie dookólne zapewnia się przez nawijanie naprężonego drutu w dwóch lub więcej kierunkach. Drut można również nawinąć na gotowy produkt, a następnie zabezpieczyć zbrojenie warstwą betonu.
Elementy wzmacniające stosowane w konstrukcjach składają się z samego zbrojenia, urządzenia do jego mocowania podczas rozciągania oraz urządzeń elastycznych zapewniających projektowe rozmieszczenie poszczególnych prętów i drutów tworzących element wzmacniający.Projektowanie urządzeń do mocowania zbrojenia wiąże się z technologia wykonania elementu wzmacniającego, rodzaj maszyn i urządzeń napinających.Stosuje się dwa rodzaje takich urządzeń – zaciski i kotwy.Z kolei zaciski i kotwy dzielą się ze względu na sposób mocowania zbrojenia na klinowe, płaskie, stożkowe, faliste, hakowe, gwintowane, wpustowe i ślepe, w których końce wiązek zbrojeniowych wciskane są w klatkę ze stali miękkiej lub betonowane w miseczkach metalowych. Wszystkie te urządzenia, z wyjątkiem gwintowanych, służą do mocowania prętów obu profile okrągłe i okresowe.
Do chwytania i zabezpieczania zbrojenia prętów stosuje się końcówki gwintowane lub różne krakersy klinowe o profilu przeciwnym do profilu naprężonego zbrojenia. Postępową konstrukcją urządzeń zaciskowych są zaciski grupowe stosowane przy wstępnym, zmechanizowanym montażu wiązek przewodów. Każdy pręt, nitka drutu lub ich grupa jest zabezpieczona zaciskami.Kotwy do wiązek drutu wyróżniają się sposobem naprężenia i zabezpieczenia końców. Do mocowania belek stosuje się kotwy stożkowe z naprężeniem zbrojenia za pomocą podnośnika dwustronnego działania oraz kotwy tulejowe z naprężeniem zbrojenia za pomocą podnośnika prętowego.
Audycja naprężenie wstępne zbrojenie betonu odbywa się na trzy sposoby:
poprzez przyklejenie do betonu zbrojenia o średnicy 2,5-3 mm; przy większej średnicy zbrojenia przyczepność zapewnia się poprzez wykonanie wgnieceń na powierzchni drutu, skręcenie splotów 2-3 drutów lub zastosowanie okresowego wzmocnienia profilu;
poprzez przyczepność zbrojenia do betonu, dodatkowo zbrojonego urządzeniami kotwiącymi;
poprzez przeniesienie sił rozciągających na beton poprzez urządzenia kotwiące na końcach elementu wzmacniającego bez uwzględnienia przyczepności zbrojenia do betonu.
Zbrojenie jest naprężone różne sposoby: mechaniczne elektrotermiczne, ciągłe napięcie mechaniczne i elektromechaniczne, a także chemiczne przy zastosowaniu cementu pęczniejącego.
W przypadku mechanicznej metody rozciągania zbrojenie rozciąga się pod wpływem obciążenia osiowego wytwarzanego przez podnośniki lub inne maszyny napinające. Zbrojenie jest napinane w następującej kolejności. W pierwszej kolejności zbrojenie napręża się siłą równą 50% naprężenia obliczeniowego, sprawdzane są urządzenia zaciskowe i położenie zbrojenia. Następnie napięcie zbrojenia reguluje się do wartości przekraczającej napięcie obliczeniowe o 10%, ale nie więcej niż 0,75 wytrzymałości drutu na rozciąganie i utrzymuje się w tym stanie przez 5 minut, po czym napięcie zmniejsza się do wartość projektowa.
Zwolnienie naprężonego zbrojenia (zagęszczanie betonu) przeprowadza się po osiągnięciu przez beton wymaganej wytrzymałości produktu i sprawdzeniu, czy końce drutu są zakotwiczone w betonie. Rzeczywistą wytrzymałość betonu określa się poprzez badanie próbek kontrolnych. Wytrzymałość betonu w momencie zwolnienia zbrojenia wynosi zwykle 70% wytrzymałości projektowej. Odprężanie na stojakach odbywa się stopniowo w 2-3 etapach. Jeżeli nie jest możliwe stopniowe zwalnianie naprężenia, wówczas naprężone druty przecina się symetrycznie względem osi przekroju, a liczba jednocześnie ciętych drutów nie przekracza 10-15% całkowitej liczby.
Istotą metody napinania elektrotermicznego jest to, że wydłużenie zbrojenia uzyskuje się poprzez podgrzanie go elektrycznie do określonej temperatury, po czym nagrzany pręt jest obustronnie kotwiony w ogranicznikach formy lub stojaka, co zapobiega skróceniu pręta podczas to się ochładza. Po zabetonowaniu konstrukcji i utwardzeniu betonu następuje zwolnienie zbrojenia z ograniczników i przeniesienie siły rozciągającej zbrojenia na beton. Metoda ta w porównaniu z metodą energetyczną ma zalety zarówno pod względem prostoty sprzętu, jak i pracochłonności.
Elektrotermiczna metoda napinania zbrojenia nie wymaga drogiego sprzętu (podnośników) i jest mniej pracochłonna. Stosowany jest do naprężania prętów zbrojeniowych ze stali klasy A-IV, a także hartowanej stali ciągnionej klasy A-P1v, zbrojenia drutem i splotką z drutu stalowego o wysokiej wytrzymałości, ciągnionego na zimno, o profilu okresowym o średnicy 4- Splotki stalowe o średnicy 5 mm i siedmiu drutach. Do elektrotermicznego naprężania zbrojenia stosuje się instalacje z sekwencyjnym i jednoczesnym napinaniem kilku prętów. Dodatkowo instalacje można realizować z ogrzewaniem prętów na zewnątrz formy lub bezpośrednio w niej. Na ryc. Rysunek 77 przedstawia instalację do elektrycznego ogrzewania zbrojenia prętów na zewnątrz formy. Instalacja może jednocześnie podgrzewać 3-4 pręty zbrojeniowe o średnicy 12-14 mm, co odpowiada liczbie prętów w produkcie.
Instalacja składa się z dwóch wsporników kontaktowych (stałego i ruchomego) oraz środkowego wspornika. Każdy styk posiada dwie szczęki – przewodzącą prąd i dociskową. Nagrzewanie prętów jest automatycznie kontrolowane poprzez ich wydłużenie. Podgrzane pręty są wyjmowane z instalacji i umieszczane w ogranicznikach form.
Ciągłe mechaniczne i elektromechaniczne napinanie zbrojenia. Istota zbrojenia naprężonego poprzez ciągłe nawijanie zbrojenia drutowego sprowadza się do tego, że drut wstępnie naprężony do zadanej wartości układany jest na tacy formierskiej zgodnie z przyjętym schematem zbrojenia. Rozciągnięty drut mocuje się poprzez owinięcie wokół kołków umieszczonych na obwodzie palety lub stojaka. Siła naprężenia zbrojenia jest przenoszona przez kołki na stojak lub formę, aż beton stwardnieje w produkcie. Po osiągnięciu przez beton wymaganej wytrzymałości drut zostaje przecięty, a siła rozciągająca zostaje przeniesiona ze zbrojenia na beton. Zbrojenie może być zlokalizowane w kierunku wzdłużnym lub poprzecznym względem osi produktu, poprzecznie lub ukośnie. Beton w produkcie poddawany jest wstępnemu ściskaniu dwu- i trójosiowemu, a nawet objętościowemu.
Zaletą zbrojenia ciągłego jest możliwość kompleksowej mechanizacji i automatyzacji procesu technologicznego. Ciągłe nawijanie i napinanie drutu odbywa się na kilku typach maszyn: z obrotową platformą stołową, z obrotową trawersą, z ruchem wzdłużno-poprzecznym wózka i nieruchomą paletą (obwodem), z ruchem posuwisto-zwrotnym wózka i obracający się rdzeń lub obwód. Podstawowymi elementami każdej z tych maszyn są: zespół odwijania cewek i podawania drutu o zadanym naprężeniu; jednostka do przesuwania palety lub rolki podającej; zespół do układania drutu na kołkach lub na rdzeniu według zadanego wzoru.
Na ryc. 78 przedstawia schemat maszyny DN-7 z ruchem wzdłużno-poprzecznym wózka do ciągłego nawijania zbrojenia z drutu podczas produkcji stanowiskowej konstrukcji wzmocnionych naprężeniami. Zbrojenie nawijane jest podczas ruchu posuwisto-zwrotnego zwijarki poruszającej się po torach szynowych stojaka wzdłuż linii formowania z prędkością 30-40 m/min oraz ruchu posuwisto-zwrotnego w kierunku poprzecznym do osi stojaka w przybliżeniu taką samą prędkość wózka z wrzecionem. Wrzeciono posiada na końcu pełnoobrotową pinolę, przez którą drut podawany jest na stojak. Naprężony drut kotwiony jest na kołkach umieszczonych na obwodzie stojaka (poza obszarem betonowania). W maszynach zwijających często dochodzi do pęknięć drutu na skutek sił rozciągających i aby zapobiec takim zjawiskom w określonym obszarze, drut jest podgrzewany prądem elektrycznym, dla którego maszyna jest wyposażona w transformator. To nie tylko zapobiega pękaniu drutu, ale także zmniejsza pracę wymaganą do naprężenia zbrojenia.
3. FORMOWANIE WYROBÓW ZBETONOWYCH
Ogólne problemy organizacja formowania
Zadaniem kompleksu technologicznego operacji formowania jest uzyskanie gęstych wyrobów o zadanych kształtach i rozmiarach. Zapewnia to zastosowanie odpowiednich form, a wysoką gęstość uzyskuje się poprzez zagęszczenie mieszanki betonowej. Operacje procesu formowania można podzielić na dwie grupy: pierwsza obejmuje operacje wytwarzania i przygotowania form (czyszczenie, smarowanie, montaż), druga - zagęszczanie wyrobów betonowych i uzyskanie ich pożądanego kształtu. Nie mniej ważne są operacje transportowe, których koszt w sumie może osiągnąć 10-15%. W niektórych przypadkach analiza techniczno-ekonomiczna operacji transportowych determinuje organizację procesu technologicznego jako całości. Najbardziej typowa pod tym względem jest produkcja wyrobów wielkogabarytowych, wyjątkowo ciężkich – belek, kratownic, przęseł mostów, gdy ze względu na znaczne koszty przeprowadzek produkcja wyrobów zorganizowana jest w jednym miejscu, tj. na stole przyjęty zostaje schemat organizacji procesu. W ogólnym kompleksie technologicznym produkcji wyrobów żelbetowych operacje formowania zajmują centralne i decydujące miejsce. Wszystkie pozostałe operacje – przygotowanie mieszanki betonowej, przygotowanie zbrojenia – mają w pewnym stopniu charakter przygotowawczy i mogą być wykonane poza terenem zakładu, w danym zakładzie wyrobów żelbetowych; mieszankę betonową można uzyskać centralnie z betoniarni, produkty zbrojeniowe - z centralnego warsztatu zbrojeniowego w regionie. Taka organizacja fabryki wyrobów żelbetowych jest niezwykle korzystna pod względem technicznym i ekonomicznym: koszt zarówno mieszanki betonowej, jak i zbrojenia jest znacznie niższy niż w przypadku ich produkcji w fabryce wyrobów żelbetowych, ponieważ wydajność mieszalni betonu i zbrojowni na cele scentralizowane jest wielokrotnie większa. wyższe niż te same warsztaty fabryki wyrobów żelbetowych. A jeśli moc jest wyższa, organizacja procesu technologicznego może być bardziej zaawansowana: korzystne okazuje się stosowanie linii automatycznych i sprzętu o wysokiej wydajności, które znacznie zwiększają wydajność pracy, obniżają koszty produktów i poprawiają ich jakość . Jednak zdecydowana większość fabryk wyrobów żelbetowych odmawia tak racjonalnej organizacji procesu technologicznego, ponieważ możliwe są zakłócenia w dostawie niezbędnych półproduktów; jest to tym ważniejsze, jeśli weźmie się pod uwagę, że nie jest możliwe wytworzenie zapasu mieszanki betonowej na dłużej niż 1,5-2 godziny pracy linii formierskich - mieszanina zacznie twardnieć.
Formy i smary
Do produkcji wyrobów żelbetowych stosuje się formy drewniane, stalowe i żelbetowe, a czasem z betonu zbrojonego metalem. Należy zaznaczyć, że kwestia wyboru materiału na formę jest bardzo istotna zarówno pod względem technicznym, jak i ekonomicznym. Zapotrzebowanie na prefabrykaty betoniarskie jest ogromne. Objętość pleśni w większości fabryk powinna być nie mniejsza niż objętość produktów wytwarzanych przez roślinę w ciągu dnia przy sztucznym utwardzaniu i 5-7 razy większa przy naturalnym dojrzewaniu. W wielu przypadkach zapotrzebowanie na formy determinuje całkowitą intensywność produkcji metalu (waga jednostki metalu na jednostkę produkcji), co znacząco wpływa na wskaźniki techniczne i ekonomiczne całego przedsiębiorstwa. Należy również wziąć pod uwagę, że formy pracują w najtrudniejszych warunkach: są systematycznie poddawane montażowi i demontażowi, oczyszczaniu przylegającego do nich betonu, obciążeniom dynamicznym podczas zagęszczania mieszanki betonowej i transportu oraz narażeniu na działanie wilgoci ( para wodna) w okresie utwardzania produktów. Wszystko to nieuchronnie wpływa na czas ich obsługi i wymaga systematycznego uzupełniania zapasów formularzy.
Jeśli weźmiemy pod uwagę jednorazowe koszty zorganizowania fabryki wyrobów żelbetowych, wówczas formy drewniane okazują się najbardziej opłacalne, ale ich żywotność i jakość produktów uzyskanych w takich formach są niskie: obrót drewnianymi formy w produkcji nie przekraczają dziesięciu, po czym formy tracą niezbędną sztywność, naruszane są ich wymiary i konfiguracja pojemnika formierskiego. Żywotność form metalowych jest kilkukrotnie dłuższa niż form drewnianych, przez co koszty eksploatacji form metalowych są ostatecznie niższe niż form drewnianych, choć koszty początkowe były wysokie. Dotyczy to jednak organizacji masowej produkcji tego samego rodzaju wyrobów żelbetowych. Przy wytwarzaniu wyrobów o tym samym standardowym rozmiarze w małych ilościach wskazane może być zastosowanie form drewnianych, gdyż są one tańsze: można je wyprodukować bezpośrednio w zakładzie wyrobów żelbetowych. Zatem w tym przypadku konieczna jest analiza techniczno-ekonomiczna produkcji, której wyniki pozwolą na wybór racjonalnego rozwiązania.
Formy metalowe najczęściej spotykane są w specjalistycznych zakładach prefabrykacji betonowej. Trwałość, długotrwałe zachowanie wymiarów, łatwość montażu i demontażu, duża sztywność, która zapobiega odkształcaniu się wyrobów podczas produkcji i transportu – to zalety form metalowych, które zdecydowały o ich powszechnym zastosowaniu. Wady form metalowych polegają na tym, że znacznie zwiększają zużycie metalu w przedsiębiorstwie, pogarszając w ten sposób wskaźniki techniczne i ekonomiczne projektu.
Specyficzne zużycie metalu w formach zależy od rodzaju formowanych w nich wyrobów oraz organizacji procesu formowania. Najniższe zużycie metalu metodą laboratoryjną. Przy formowaniu wyrobów na stojakach płaskich jednostkowe zużycie metalu wynosi 300-500 kg masy metalu formy na każdy 1 m3 objętości produktu. Przy wytwarzaniu wyrobów w formach ruchomych w technologii kruszywa przepływowego zużycie metalu wynosi średnio 1000 kg/m3 dla wyrobów płaskich (panele, podłogi) i 2000-3000 kg/m3 dla wyrobów o złożonym profilu (biegi schodów i podestów, belki i płatwie o przekroju teowym, panele żebrowane). Największe zużycie metalu w formach charakteryzuje się formowaniem za pomocą systemu transportowego, gdy produkty formowane są na paletach wózkowych: sięga 7000-8000 kg metalu na każdy 1 m uformowanego w nich produktu, czyli masa formy wynosi 3-krotność lub więcej masy produktu w formie. Ten wskaźnik techniczno-ekonomiczny był powodem odmowy dalszego rozwoju technologii przenośników i zaprzestania budowy fabryk o takim schemacie technologicznym.
Formy z betonu zbrojonego metalem, które wciąż nie są zbyt powszechne, zajmują pośrednie miejsce we wskaźnikach technicznych i ekonomicznych: początkowe koszty ich produkcji nie są niższe niż metalowe, ale są 1,5-2 razy cięższe, co wpływa na koszty transportu. Zaletą form z betonu zbrojonego metalem jest to, że umożliwiają one 2-3-krotne obniżenie kosztów metalu przy produkcji formy: metal jest wydawany tylko na boczne wyposażenie formy, natomiast paleta, która ma najwyższą zużycie metalu (musi mieć wysoką sztywność), jest wykonane z żelbetu.
Niezależnie od materiału, wobec form obowiązują następujące ogólne wymagania:
nadanie produktom niezbędnych kształtów i. rozmiary i utrzymanie ich podczas wszystkich operacji technologicznych;
minimalna waga w stosunku do masy jednostkowej produktu, którą osiąga się poprzez racjonalne projektowanie form;
prostota i minimalna pracochłonność montażu i demontażu form;
Szczególne znaczenie dla jakości produktów i zachowania kształtów mają
jakość i właściwy wybór przeznaczone smary
zapobiegają przyleganiu betonu do materiału formy. Smarowanie powinno
dobrze trzyma się powierzchni formy podczas wszystkich procesów technologicznych
logiczne operacje, zapewniają możliwość ich zmechanizowania
aplikacja (natrysk) całkowicie eliminuje przyczepność wyrobów betonowych
z kształtem i nie psuć wyglądu produktów. Te wymagania
smary o następujących składach są w dużej mierze spełnione
emulsje olejowe z dodatkiem sody kalcynowanej;
smary olejowe - mieszanina olejów słonecznych (75%) i wrzecionowych (25%) lub 50% oleju maszynowego i 50% nafty;
mydłoglina, mydłocement i inne wodne zawiesiny drobnych materiałów, takich jak kreda, grafit.
Cechy formowania i wytwarzania produktów na różne sposoby
Metoda stojaka. Formowanie wyrobów metodą stołową, czyli w formach nieruchomych, odbywa się na stojakach płaskich, w matrycach oraz w kasetach.
Formowanie na płaskich ławkach. Stojak płaski to gładka, polerowana betonowa platforma, podzielona na: oddzielne linie formierskie. Urządzenia grzewcze umieszcza się w betonowym korpusie obiektu w postaci rur, przez które przepuszcza się parę, spala się gorącą wodę lub umieszcza się w nich wężownice elektryczne. Przed przystąpieniem do formowania na stanowisku montowane są formy przenośne, do których po nasmarowaniu umieszczane jest zbrojenie i podawanie mieszanki betonowej z betoniarki poruszającej się po szynach nad każdą linią. Ze względu na sposób organizacji pracy stojaki płaskie dzielą się na długie, wsadowe i krótkie.
Stojaki stretch otrzymały tę nazwę, ponieważ drut stalowy odwinięty ze zwojów znajdujących się na końcu stojaka, za pomocą dźwigu lub specjalnego wózka, przeciągany jest wzdłuż linii formowania na przeciwległy koniec stojaka, gdzie jest mocowany do ograniczników (ryc. 79). Stanowiska te wykorzystywane są do produkcji wyrobów długich o dużych przekrojach i wysokościach, a także do produkcji wyrobów wzmocnionych prętami zbrojeniowymi. Obecnie najbardziej zmechanizowanym stanowiskiem jest stanowisko typu GSI (6242), umieszczone w płytkiej tacy. Produkty na tym stoisku produkowane są w następujący sposób. Wiązki z drutem umieszczane są w osi wyprasek, a końce drutów zabezpieczane są za pomocą klinów w chwytakach zamontowanych na specjalnych wózkach. Następnie za pomocą dźwigu lub wciągarki zamontowanej na przeciwległym końcu stojaka wózek przesuwa się, niosąc ze sobą drut odwijany ze szpuli. Na końcu stojaka uchwyt wraz z drutami wzmacniającymi jest zdejmowany i mocowany do ograniczników. Naprężanie zbrojenia (od 2 do 10 drutów jednocześnie) odbywa się za pomocą podnośników, po czym układa się i zagęszcza mieszankę betonową. Sposób zagęszczania dobiera się w zależności od rodzaju formowanych wyrobów – wibratory powierzchniowe, głębokie i zawieszane. Po zagęszczeniu mieszanki betonowej wyrób przykrywa się, podaje parę wodną i przeprowadza obróbkę cieplno-wilgotnościową według zadanego reżimu.
Stanowiska wsadowe (ryc. 80) różnią się od przeciąganych tym, że zbrojenie drutowe gromadzone jest w workach (wiązkach) na specjalnych stołach wsadowych lub instalacjach. Po złożeniu paczki z wymaganej ilości drutów, które są zabezpieczone na końcach specjalnymi zaciskami, paczka jest przenoszona na linię stojaka i mocowana do ograniczników. Dalsze operacje wytwarzania wyrobów na stanowiskach wsadowych są takie same, jak na stanowiskach przeciągania. Stojaki opakowaniowe służą do produkcji wyrobów o małym przekroju, a także wyrobów wykonanych z pojedynczych elementów z późniejszym naprężeniem zbrojenia na stwardniałym betonie.
Stanowisko krótkie składa się z odrębnych stacjonarnych stanowisk formierskich w postaci form nośnych (rys. 81), przeznaczonych do wykonywania kratownic, belek i innych konstrukcji żelbetowych sprężonych budownictwo przemysłowe. Stojaki mogą być jednopoziomowe, gdy produkty są ułożone w jednym rzędzie na wysokość, oraz wielopoziomowe (pakowane), gdy produkty są ułożone w kilku rzędach na wysokość. Cała technologia wytwarzania wyrobów – przygotowanie stojaka, napinanie zbrojenia, układanie i zagęszczanie mieszanki betonowej, obróbka cieplna i wreszcie rozbieranie wyrobów – odbywa się tymi samymi metodami, co przy wytwarzaniu wyrobów na długich stojakach. Jednak zaletą krótkiego stanowiska wsadowego w porównaniu do długiego jest pełniejsze wykorzystanie powierzchni produkcyjnej warsztatu.
Formowanie w kasetach. Metodą kasetową formowanie i utwardzanie wyrobów odbywa się w stacjonarnej pionowej formie kasetowej (ryc. 82). Kaseta to szereg przegród utworzonych przez pionowe ściany stalowe lub żelbetowe, w każdej z nich formowany jest jeden produkt. Zatem liczba produktów jednocześnie uformowanych w kasecie odpowiada liczbie przegródek. Znacząco zwiększa to wydajność pracy, a wytwarzanie wyrobów w pozycji pionowej radykalnie zmniejsza przestrzeń produkcyjną, co jest najważniejszą zaletą metody kasetowej. Mieszanka betonowa dostarczana jest do instalacji kasetowej za pomocą pompy poprzez betonowy rurociąg, a następnie poprzez przepustnicę poprzez elastyczny wąż dostaje się do przedziału, w którym wstępnie montowane jest zbrojenie. Mieszankę zagęszcza się za pomocą wibratorów zawieszanych i głębokich. Kaseta posiada specjalne płaszcze parowe służące do podgrzewania produktów podczas ich obróbki temperaturowo-wilgotnościowej. W tym celu można wykorzystać oddzielne przegródki, a także elektryczne ogrzewanie produktów. Po osiągnięciu przez beton określonej wytrzymałości ścianki przedziałów kaset są lekko rozsuwane za pomocą mechanizmu, a produkt jest wyjmowany z kasety za pomocą dźwigu.
W metodzie przepływowo-kruszywowej umieszczanie mieszanki zbrojeniowo-betonowej w formie i zagęszczanie mieszanki odbywa się na jednym stanowisku technologicznym, a utwardzanie wyrobów odbywa się w specjalnej aparacie termicznym (komory parowe lub autoklawy), tj. Cały proces technologiczny dzieli się na operacje (Rys. 83). Zmontowaną i nasmarowaną formę wraz z ułożonym w niej zbrojeniem instaluje się na platformie wibracyjnej, kostkę betonową wypełnia się mieszanką betonową i włącza platformę wibracyjną. Uformowany wyrób wraz z formą przenoszony jest dźwigiem do komory parowania, a następnie po kontroli przez dział kontroli jakości wywożony na wózku do magazynu. Mieszanka betonowa z betoniarni dostarczana jest do betoniarek poprzez wiadukt. Każda linia posiada dodatkowo stanowiska do wykańczania wyrobów, układania zbrojenia, rozbierania form, ich czyszczenia i smarowania. Oddzielne słupki można łączyć, a słupek na produkty wykończeniowe można przesuwać w miejsce rozbiórki.
Metoda przenośnikowa różni się od metody przepływowo-agregacyjnej dużym podziałem operacji technologicznych na osobne wyspecjalizowane stanowiska. Na linii przenośnika znajduje się aż dziewięć takich stanowisk: rozbiórka wyrobów, czyszczenie i smarowanie form, kontrola form, układanie zbrojenia i osadzonych części, układanie mieszanki betonowej, zagęszczanie mieszanki betonowej, przetrzymywanie wyrobów przed obróbką cieplną (ryc. 84). Produkty formowane są na paletach wózkowych wyposażonych w specjalny sprzęt tworzący ścianki formy. Wymiary palety to 7x4,5 m, co pozwala na jednoczesne formowanie jednego produktu o powierzchni 6,8x4,4 m lub kilku produktów o jednakowej powierzchni w przypadku zamontowania na palecie elementów oddzielających. W czasie pracy kompleksu formierskiego wózek przemieszczany jest za pomocą popychacza rytmicznie co 12-15 minut od słupa do słupa po specjalnie ułożonych torach. Uformowany produkt jest następnie poddawany działaniu pary w ciągłej komorze o kilku poziomach wysokości. Podnoszenie wyprasek na górne kondygnacje i opuszczanie ich po zakończeniu obróbki cieplnej odbywa się za pomocą specjalnych podnośników (reduktorów) zainstalowanych po stronie załadunku i rozładunku komór. Ruchem wózków sterowany jest zdalnie przez operatora z panelu sterowania. Metoda ta zapewnia również, że większość operacji formowania jest wykonywana i kontrolowana zdalnie. W tym celu proces formowania jest w miarę możliwości dzielony na osobne operacje i organizowane są odpowiednie stanowiska specjalistyczne, co jest niezbędnym czynnikiem w automatyzacji produkcji.
Metoda ciągłego formowania realizowana jest na walcarce wibracyjnej (ryc. 85). Posiada stale poruszający się pas składający się z indywidualnych wolumetrycznych lub płaskie talerze; te pierwsze zapewniają żebrowaną powierzchnię paneli, natomiast te drugie zapewniają gładką powierzchnię. Na początku młyna układane jest zbrojenie na poruszającej się ciągle taśmie, następnie w kolejnej sekcji mieszanka betonowa jest dostarczana i zagęszczana wibracją oraz częściowo walcowana przez walce kalibrujące; te ostatnie umożliwiają uzyskanie wyrobów o ściśle stałej grubości i gładkiej powierzchni. Uformowany produkt w miarę ruchu taśmy trafia do strefy obróbki cieplno-wilgotnościowej i po dwóch godzinach gotowania na parze opuszcza taśmę w gotowej formie i wysyłany jest do magazynu. Prędkość taśmy młyna wynosi do 25 m/h. Przy największej szerokości produktu wynoszącej 3,2 m wydajność sięga 80 m2/h. Jest to najbardziej produktywna i zautomatyzowana metoda produkcji paneli.
4. HARTOWANIE WYROBÓW ZBETONOWYCH
Utwardzanie wyrobów formowanych jest końcową operacją technologii prefabrykatów betonowych, kiedy wyroby uzyskują wymaganą wytrzymałość. Ten ostatni może być równy klasie betonu w przypadku niektórych produktów lub niższy w przypadku innych. Zatem wytrzymałość wyrobów betonowych dostarczonych do konsumenta musi być równa: co najmniej 70% wytrzymałości markowej (28-dniowej) dla wyrobów betonowych wykonanych z cementu portlandzkiego lub jego odmian oraz 100% dla wyrobów wykonanych z krzemianu (wapna) -piasek) lub beton komórkowy. Jednakże w przypadku niektórych wyrobów z betonu cementowego portlandzkiego wytrzymałość na odpuszczanie musi przekraczać 70%. Przykładowo wytrzymałość betonowych podkładów kolejowych musi być równa stopniowi przęseł mostów – co najmniej 80% tego stopnia. Dopuszczalne zmniejszenie siły sprzedaży produktów zależy wyłącznie od względów ekonomicznych, ponieważ w tym przypadku czas trwania cyklu produkcyjnego ulega skróceniu i odpowiednio wzrasta obrót środków. W tym przypadku oznacza to, że produkty zyskają wytrzymałość, której brakuje sile marki w procesie transportu i montażu, a do czasu obciążenia eksploatacyjnego ich wytrzymałość nie będzie niższa niż projektowana (siła marki).
W zależności od temperatury otoczenia wyróżnia się następujące trzy zasadniczo różne sposoby utwardzania produktów:
normalna - temperatura 15-20° C;
obróbka cieplna w temperaturach do 100°C pod normalnym ciśnieniem;
obróbka w autoklawie – parowanie pod wysokim ciśnieniem pary i temperaturze otoczenia powyżej 100°C.
Niezależnie od trybu utwardzania wilgotność względna otoczenia musi być bliska 100%, w przeciwnym razie produkty wysychają, co prowadzi do spowolnienia lub zaprzestania wzrostu ich wytrzymałości, ponieważ utwardzanie betonu to przede wszystkim uwodnienie cement, czyli oddziaływanie cementu z wodą.
Normalne warunki utwardzania osiąga się w warunkach naturalnych, bez użycia jakiejkolwiek aparatury termicznej i doprowadzenia ciepła. To najważniejsza zaleta techniczna i ekonomiczna naturalny sposób hartowanie, charakteryzujące się łatwością organizacji i minimalnymi kosztami kapitałowymi. Jednocześnie metoda ta może być ekonomicznie uzasadniona tylko w wyjątkowych przypadkach. W warunkach naturalnych produkty osiągają 70% wytrzymałości marki w ciągu 7-10 dni, natomiast przy sztucznym utwardzaniu (parowanie lub obróbka w autoklawie) wytrzymałość tę osiąga się 15-20 razy szybciej - w ciągu 10-16 godzin.W związku z tym zapotrzebowanie na przestrzeń produkcyjną i zmniejsza się wielkość zapasów form i skraca się czas obrotu kapitałem. To jest powód stosowania sztucznego hartowania w większości roślin.
Jednocześnie chęć porzucenia tego ostatniego jest aktualnym problemem współczesnej technologii betonu. Istnieją już betony, które w ciągu 1 dnia. normalne warunki hartowanie uzyskuje do 40-50% siły marki. Osiąga się to poprzez stosowanie wysokiej jakości cementów szybkotwardniejących, sztywnych mieszanek betonowych, intensywne zagęszczanie wibracyjne z dodatkowym obciążeniem, stosowanie dodatków - przyspieszaczy twardnienia, aktywację wibracyjną mieszanki betonowej przed formowaniem oraz stosowanie gorących mieszanek betonowych. Dalszy rozwój prac w tym kierunku najwyraźniej umożliwi w nadchodzących latach rezygnację z sztucznego utwardzania w wielu przypadkach. Jednak obecnie sztuczna metoda utwardzania produktów przewyższa metodę naturalną pod względem wskaźników technicznych i ekonomicznych.
Obróbka cieplna pod normalnym ciśnieniem. Istnieje kilka metod obróbki cieplnej wyrobów żelbetowych pod ciśnieniem normalnym: parowanie w komorach, ogrzewanie elektryczne, ogrzewanie kontaktowe, przetrzymywanie w basenach cieplnych (w gorącej wodzie). Przewaga techniczna i ekonomiczna nadal pozostaje w przypadku parowania w komorach i metoda ta jest stosowana w zdecydowanej większości przedsiębiorstw produkujących prefabrykaty betonowe.
Parowanie odbywa się w komorach okresowych i ciągłych. W tym ostatnim przypadku świeżo uformowane produkty w sposób ciągły wchodzą do Eagonettes, a gotowe produkty również w sposób ciągły wychodzą z przeciwnego końca tunelu komorowego. Podczas procesu utwardzania produktu komora podlega strefom ogrzewania, ogrzewania izotermicznego (ze stałą maksymalną temperaturą parowania) i chłodzenia. W zasadzie komory ciągłe, jak ogólnie każdy sprzęt pracujący w sposób ciągły, zapewniają najwyższą wydajność usuwania produktu na jednostkę objętości. Jednak w tym przypadku konieczność stosowania wózków i mechanizmów do przemieszczania produktu, a także szereg trudności konstrukcyjnych i problemów w inżynierii cieplnej komór tunelowych, nie pozwalają na powszechne stosowanie tego typu komór parowych. Są używane tylko przy metodzie produkcji przenośników i jest mało prawdopodobne, że zostaną odebrane dalszy rozwój. Obiecujące są pionowe kamery ciągłe.
Wśród komór okresowych głównym zastosowaniem są komory wgłębne (ryc. 86), o głębokości około 2 m i wystające 0,5-0,7 m ponad poziom posadzki warsztatu. Wielkość komory w planie odpowiada wielkości produktów lub jest ich wielokrotnością. Najkorzystniejszy jest rozmiar komory odpowiadający wielkości jednego produktu w planie, ponieważ ładowność komory jest najmniejsza, a bezproduktywny czas przestoju komory pod załadunkiem jest minimalny. Zwiększa się jednak liczba kamer. Analiza techniczno-ekonomiczna tych dwóch wskaźników (dodatniego i negatywnego) wykazała, że najkorzystniejsza jest wielkość komory w planie odpowiadająca wielkości obu produktów.
Tryb parowania w komorach charakteryzuje się czasem narastania temperatury, utrzymywaniem temperatury maksymalnej i czasem chłodzenia, a także najwyższą temperaturą w okresie ogrzewania izotermicznego. Stosuje się szeroką gamę trybów utwardzania w zależności od właściwości cementu i jego rodzaju, właściwości mieszanki betonowej (sztywny lub elastyczny), rodzaju betonu (ciężki lub lekki) i wielkości produktów (cienkie lub masywne ). Jako średnią można podać następujący tryb: wzrost temperatury w tempie 25-35 stopni/h, spadek temperatury w tempie 30-40 stopni/h, ekspozycja izotermiczna przez 6-8 n i maksymalna temperatura ogrzewania 80 -90° C. Zatem całkowity czas parowania produktów przy użyciu zwykłego cementu portlandzkiego wynosi średnio 12-15 h. Jak widać, utwardzanie produktów jest najdłuższą operacją, kilkadziesiąt razy dłuższą niż wszystkie inne (np. formowanie podłoga wytrzymuje 12-15 minut, a panel ścienny z warstwą wykończeniową nie przekracza 20-25 minut). Powoduje to konieczność znalezienia sposobów na skrócenie czasu gotowania na parze, dla czego konieczna jest znajomość czynników, które to determinują.
Cementy wolnotwardniejące (pucolanowe i żużlowe portlandzkie) wymagają dłuższego przetrzymywania izotermicznego (do 10-14 godzin) i wyższych temperatur ogrzewania izotermicznego (do 95-100°C) oraz całkowitego czasu parowania wyrobów wykonanych z betonu przy użyciu tych cementów wynosi 16-20 h. Zastosowanie sztywnych mieszanek betonowych o niskiej początkowej zawartości wody pozwala skrócić czas parowania o 15-20%. Jeśli weźmiemy pod uwagę, że dodatkowe koszty energii i pracy związane z tworzeniem sztywnych mieszanek nie przekraczają 10-15% i są kompensowane przez zmniejszenie zużycia cementu, wówczas ekonomiczna wykonalność stosowania sztywnych mieszanek staje się w tym przypadku oczywista. Produkty wykonane z betonu lekkiego, ponieważ ze względu na zwiększone właściwości termoizolacyjne nagrzewają się powoli, wymagają również dłuższego reżimu obróbki cieplnej.
Wraz z wyżej wymienionymi sposobami przyspieszenia utwardzania betonu
podczas gotowania na parze stosunkowo niedawno zaproponowano inną metodę -
stosować do formowania podgrzanego do 75-85°C
ton mieszanek. Ogrzewa się je prądem elektrycznym przez 8-12 minut.
Metoda ta nazywa się formowaniem na gorąco. Zatem produkty
wejść do komory w postaci podgrzanej i nie wymagają czasu
podgrzewanie do maksymalnej temperatury parowania. Metoda Preusa
matrirovatsya ogólnie odmowa gotowania na parze i świeżo uformowany smutek
które produkty są objęte ochroną przed utratą ciepła (metoda termiczna
mosa) i pozostawić w tej formie na 4-6 godzin; w tym czasie beton
zyskuje niezbędną siłę. .
Elektryczne ogrzewanie produktów. Pod względem technologii oraz warunków sanitarno-higienicznych produkcji elektryczne podgrzewanie produktów ma nieporównywalną przewagę nad wszystkimi innymi metodami podgrzewania. Jej rozwój utrudnia brak i wciąż wysokie koszty energii elektrycznej: zużycie energii elektrycznej podczas elektrotermicznej obróbki betonu wynosi średnio 80-100 kWh na 1 m2 wyrobów.
Ogrzewanie kontaktowe produktów uzyskuje się poprzez bezpośredni kontakt z urządzeniami grzewczymi, np. podgrzewanymi ściankami formy lub podstawą stojaka.
Ściany komory wykonane są z cegły lub betonu. Góra komory zamknięta jest masywną pokrywą z warstwą termoizolacyjną, która zapobiega utracie ciepła. Aby zapobiec wybijaniu pary, na ścianach komory znajduje się rowek wypełniony piaskiem lub wodą, w który pasują odpowiednie występy na pokrywie komory. Tworzy to uszczelnienie, które zapobiega ulatnianiu się pary z komory. Produkty ładowane są do komory od góry za pomocą dźwigu w kilku rzędach na wysokość. Jeśli produkty są ładowane do formy, każdy górny rząd jest instalowany na ścianach podstawowej formy (przez drewniane dystanse). Jeśli produkty są formowane z częściowym natychmiastowym rozbiórką, wówczas wchodzą do komory tylko na palecie. W tym przypadku paletę z produktem montuje się na specjalnych składanych półkach znajdujących się na ścianach komory.
Tryb parowania w komorach charakteryzuje się czasem narastania temperatury, utrzymywaniem temperatury maksymalnej i czasem chłodzenia, a także najwyższą temperaturą w okresie ogrzewania izotermicznego. Stosuje się szeroką gamę trybów utwardzania w zależności od właściwości cementu i jego rodzaju, właściwości mieszanki betonowej (sztywny lub elastyczny), rodzaju betonu (ciężki lub lekki) i wielkości produktów (cienkie lub masywne ). Jako średnią można podać następujący tryb: wzrost temperatury w tempie 25-35 stopni na godzinę, spadek temperatury w tempie 30-40 stopni na godzinę, ekspozycja izotermiczna przez 6-8 godzin i maksymalna temperatura ogrzewania 80 -90° C. Zatem całkowity czas parowania produktów przy użyciu zwykłego cementu portlandzkiego wynosi średnio 12-15 h. Jak widać, utwardzanie produktów jest najdłuższą operacją, kilkadziesiąt razy dłuższą niż wszystkie inne (np. formowanie podłoga wytrzymuje 12-15 minut, a panel ścienny z warstwą wykończeniową nie przekracza 20-25 minut). Powoduje to konieczność znalezienia sposobów na skrócenie czasu gotowania na parze, dla czego konieczna jest znajomość czynników, które to determinują.
Przede wszystkim na tryb utwardzania wpływa rodzaj cementu. Zastosowanie cementów szybkotwardniejących (cementów portlandzkich alitowych i alitoglinianowych) pozwala na około 2-krotne skrócenie czasu ekspozycji izotermicznej. Dodatkowo optymalna temperatura nagrzewania wyrobów wykorzystujących te cementy mieści się w granicach 70-80°C, co również znacząco skraca czas potrzebny na nagrzanie i schłodzenie. W sumie całkowity czas obróbki cieplnej produktów przy użyciu szybko utwardzających się cementów portlandzkich alitowych i alitoglinianowych skraca się do 8-10 godzin, a wytrzymałość betonu osiąga 70-80% markowego.
Cementy wolnotwardniejące (pucolanowe i żużlowe portlandzkie) wymagają dłuższego przetrzymywania izotermicznego (do 10-14 godzin) i wyższych temperatur ogrzewania izotermicznego (do 95-100°C) oraz całkowitego czasu parowania wyrobów wykonanych z betonu przy użyciu tych cementów wynosi 16-20 h. Zastosowanie sztywnych mieszanek betonowych o niskiej początkowej zawartości wody pozwala skrócić czas parowania o 15-20%. Jeśli weźmiemy pod uwagę, że dodatkowe koszty energii i pracy związane z tworzeniem sztywnych mieszanek nie przekraczają 10-15% i są kompensowane przez zmniejszenie zużycia cementu, wówczas ekonomiczna wykonalność stosowania sztywnych mieszanek staje się w tym przypadku oczywista. Produkty wykonane z betonu lekkiego, ponieważ ze względu na zwiększone właściwości termoizolacyjne nagrzewają się powoli, wymagają również dłuższego reżimu obróbki cieplnej.
Oprócz wyżej wymienionych sposobów przyspieszania twardnienia betonu podczas parowania, stosunkowo niedawno zaproponowano inną metodę - wykorzystanie do formowania mieszanek betonowych podgrzanych do temperatury 75-85 ° C. Ogrzewa się je prądem elektrycznym przez 8-12 minut. Metoda ta nazywa się formowaniem na gorąco. Dzięki temu produkty wchodzą do komory w postaci podgrzanej i nie wymagają czasu na podgrzanie ich do maksymalnej temperatury parowania. Metoda polega na całkowitym wyeliminowaniu parowania, a świeżo uformowane gorące produkty przykrywa się, aby zapobiec utracie ciepła (metoda termosu) i pozostawia w tej formie na 4-6 godzin; W tym czasie beton zyskuje niezbędną wytrzymałość.
Elektryczne ogrzewanie produktów. Pod względem technologii oraz warunków sanitarno-higienicznych produkcji elektryczne podgrzewanie produktów ma nieporównywalną przewagę nad wszystkimi innymi metodami podgrzewania. Jej rozwój utrudnia brak i wciąż wysokie koszty energii elektrycznej: zużycie energii elektrycznej podczas elektrotermicznej obróbki betonu wynosi średnio 80-100 kW"H na 1 m3 wyrobów.
Elektryczne ogrzewanie produktów osiąga się poprzez przepuszczanie prądu przemiennego
prąd przez beton. Ten ostatni ma opór elektryczny
większy niż elektrody dostarczające do niego prąd, ale jednocześnie
posiadające pewną przewodność elektryczną, w rezultacie nagrzewają się
zamiana energii elektrycznej na ciepło. Ilość ciepła,
uwalniany w betonie pod wpływem przepływu prądu elektrycznego
prąd, zgodnie z prawem Joule’a-Lenza, jest wprost proporcjonalny
ale energia zużywana w jednostce czasu (czas przejścia
prąd) i cieplny równoważnik pracy.
Produkty masywne poddawane są ogrzewaniu elektrycznemu w formach otwartych, ponieważ produkty cienkościenne (przegrody cienkościenne, panele) mogą wysychać i zaleca się ich podgrzewanie prądem elektrycznym w kasetach. Przyjmuje się, że napięcie prądu na początku ogrzewania elektrycznego wynosi 65–90, a na końcu – do 150–220 V. W miarę utwardzania betonu przewodność elektryczna betonu maleje i do przepuszczania prądu elektrycznego wymagane jest większe napięcie.
Ogrzewanie kontaktowe produktów uzyskuje się poprzez bezpośredni kontakt z urządzeniami grzewczymi, na przykład podgrzewanymi ściankami formy, podstawy lub stojaka. W takim przypadku produkt jest szczelnie przykryty, aby zapobiec utracie wilgoci wyparowującej z niego do otoczenia. Wymaganą wilgotność wokół produktu uzyskuje się dzięki nadmiarowi wody wprowadzonej do betonu, czyli większej niż wymagana do stwardnienia cementu; jest on zawsze obecny w betonie i jest wprowadzany, jak wspomniano wcześniej, w celu uzyskania urabialnej mieszaniny. Jako czynniki chłodzące stosuje się parę wodną, gorącą wodę i podgrzany olej. Najbardziej efektywne zastosowanie ogrzewania kontaktowego polega na obróbce cieplnej cienkościennych produktów, gdy są one odpowiednio uszczelnione, np. w kasetach, w których produkt jest zamknięty w wąskich, ale głębokich przegródkach.<В этом случае возможен очень быстрый подъем температуры до максимальной (за 15-30 мин) без нарушения структуры бетона. Кроме того, образуется насыщенная паровая среда с давлением пара, несколько большим, чем атмосферное, что весьма благоприятно сказывается на процессах твердения бетона.
Obróbkę temperaturową w basenach termalnych stosuje się, gdy konieczne jest uzyskanie produktu o dużej gęstości i wodoodporności (rury, pokrycia dachowe). Hartowanie w gorącej wodzie stwarza najkorzystniejsze warunki. Wstępnie utwardzone produkty umieszcza się w basenie z gorącą wodą i trzyma w nim do momentu uzyskania wymaganej wytrzymałości. Pod względem wskaźników technicznych i ekonomicznych metoda ta ma wiele zalet: niskie zużycie ciepła zapewnia najkorzystniejsze warunki utwardzania betonu. Jednak bardzo istotna wada tej metody - konieczność późniejszego suszenia produktów - jest przyczyną praktycznej odmowy przetwarzania produktów w basenach termalnych.
Obróbka w autoklawie. Szybkość większości reakcji chemicznych, w tym interakcji cementu z wodą, która zapewnia twardnienie betonu, wzrasta wraz ze wzrostem temperatury iw większym stopniu wraz z wyższą temperaturą; Ponadto beton wymaga wilgotnego środowiska do stwardnienia. Połączenie tych dwóch czynników z powodzeniem osiąga się przy przetwarzaniu produktów parą pod wysokim ciśnieniem. Wraz ze wzrostem ciśnienia wzrasta odpowiednio temperatura pary nasyconej. Przy ciśnieniu normalnym nie można uzyskać temperatury pary nasyconej (100% wilgotności względnej) powyżej 100°C. Powyżej tej temperatury wilgotność względna otoczenia będzie mniejsza niż 100% i umieszczone w nim wyroby betonowe zaczną wysychać. Najpopularniejszym trybem obróbki w autoklawie jest ciśnienie pary 8-12 atm. Temperatura pary nasyconej wynosi około 170-200°C. W tej temperaturze wyroby o markowej wytrzymałości betonu uzyskuje się w ciągu 8-10 godzin, co daje świetny efekt techniczny i ekonomiczny.
Ważną zaletą autoklawowej obróbki betonu jest to, że w tak wysokiej temperaturze piasek, który jest obojętny w normalnej temperaturze i na parze, staje się aktywny, energicznie oddziałując z wapnem i zapewnia wytworzenie betonu o wytrzymałości 200 kg/cm2 lub więcej. Pozwala to na powszechne zastosowanie taniego bezcementowego betonu wapienno-piaskowego do wytwarzania mocnych, wodoodpornych i trwałych produktów w procesie obróbki w autoklawie. Sprzęt służący do tego celu nie odbiega od tego omówionego w rozdziale V – jednostką główną jest autoklaw.
Przy stosowaniu cementów portlandzkich zwykle stosuje się cementy wolnotwardniejące. Ich zaletą w tym przypadku jest nie tylko nieznacznie obniżony koszt, ale także duży wzrost wytrzymałości uzyskiwanej podczas obróbki w autoklawie w porównaniu do innych rodzajów cementu portlandzkiego. Dodatkowo w autoklawizowanym betonie portlandzkim część cementu (do 30-40%) można z powodzeniem zastąpić mielonym piaskiem. Jednocześnie wytrzymałość betonu nie tylko nie spada, ale obserwuje się nawet wzrost jego właściwości fizyko-mechanicznych, co ma ogromne znaczenie techniczne i ekonomiczne.
5. WYKOŃCZENIE POWIERZCHNI WYROBÓW ZBETONOWYCH
Sposób wykończenia powierzchni wyrobów żelbetowych należy wybrać, biorąc pod uwagę szereg wymagań, które mogą być podyktowane warunkami klimatycznymi, architektonicznymi i innymi warunkami jego obsługi. Wykończenie musi być trwałe i chronić produkt betonowy przed wpływami atmosferycznymi i agresywnymi, a także spełniać wymagania architektoniczne i dekoracyjne.
Obecnie powierzchnie można wykańczać masami malarskimi, materiałami elewacyjnymi i kolorowym betonem. Masy malarskie muszą być wodoodporne, trwałe i odporne na blaknięcie. Są to farby silikatowe, cementowe i polimerowe. Farby silikatowe wytwarza się z płynnego szkła, barwników mineralnych (pigmentów) i wypełniaczy, farby cementowe wytwarza się z białego cementu z barwnikami mineralnymi, farby perchlorowinylowe (polimerowe) wytwarza się z barwników mineralnych rozcieńczonych lakierem perchlorowinylowym. Farby nanosi się na powierzchnię wyrobów żelbetowych za pomocą pistoletu natryskowego w 2 lub 3 etapach, w zależności od koloru użytego barwnika i konsystencji roztworu. Powierzchnie należy malować w dodatnich temperaturach.
Materiały elewacyjne przeznaczone do wykańczania wyrobów betonowych i żelbetowych wraz z wymaganiami architektonicznymi i dekoracyjnymi podlegają wymaganiom dużej wytrzymałości i trwałości w warunkach zmiennych wpływów atmosferycznych. Obecnie jako materiały okładzinowe stosuje się płytki z kamienia naturalnego, ceramiki, azbestowo-cementu, szkła, płyt i bloków z kolorowego betonu oraz falistych blach aluminiowych.
Płytki wykonane z materiałów z kamienia naturalnego są najtrwalszym materiałem, zapewniającym różnorodną gamę kolorystyczną, uzyskiwaną poprzez piłowanie marmuru, granitu, labradorptytu, kwarcytu, wapienia i innych kolorowych skał. Płytki betonowe powstają przy użyciu specjalnych pras hydraulicznych z kolorowego betonu. Ceramiczne płytki elewacyjne, które mają wysokie właściwości dekoracyjne, stały się powszechne przy wykańczaniu paneli żelbetowych; ponadto dobrze przylegają do betonu i wyróżniają się produkcją przemysłową. Płytki dostępne są w różnych rozmiarach: dużym (10X10 i 10XX20 cm) i małym (dywan, 48X48 mm). Przy produkcji wielkogabarytowych płyt żelbetowych okładzina z płytek dywanowych jest mniej pracochłonna i bardziej produktywna niż okładzina z płytek wielkoformatowych układanych ręcznie. W Leningradzie DSK-2 do przykrycia paneli stosuje się szklane płytki elewacyjne o wymiarach 2 (2 cm), które przykleja się do tektury o podanych wymiarach. Aby zwiększyć przyczepność szklanej powierzchni płytki do zaprawy lub betonu, jej tył powierzchnia pokryta jest związkami krzemoorganicznymi typu VN-30, które charakteryzują się dobrą przyczepnością do szkła. Płytki szklane dostępne są w różnych kolorach - od białego do czarnego.
Kolorowe płytki cementowe i blachy aluminiowe można również stosować jako materiały okładzinowe do wykańczania żelbetowych paneli ściennych, które charakteryzują się dużą odpornością na warunki atmosferyczne i wytrzymałością oraz dobrymi właściwościami architektonicznymi i dekoracyjnymi. Do tych samych celów nadaje się również kolorowy beton. Do jego produkcji stosuje się nieorganiczne farby mineralne, które charakteryzują się wysoką odpornością na alkalia i warunki atmosferyczne. Kolory czerwone, żółte i brązowe betonu uzyskuje się przez dodanie pigmentów z tlenków żelaza, zielone - przez dodanie zielonego tlenku lub wodorotlenku chromu.
6. ODBIÓR I BADANIA WYROBÓW ZBETONOWYCH
Wyroby żelbetowe przyjmowane są w partiach składających się z
podobnych produktów wytwarzanych przy użyciu tej samej technologii przez pewien okres czasu
ponad 10 dni.
Podczas procesu odbioru wygląd produktów jest sprawdzany poprzez kontrolę zewnętrzną, stwierdza się obecność pęknięć, ubytków i innych wad. Następnie za pomocą linijek i szablonów miarowych sprawdza się prawidłowy kształt i wymiary gabarytowe wyrobów. Jeżeli pomiary kontrolne produktu wykażą odchylenia w długości lub szerokości przekraczające dopuszczalne granice, produkt zostanie odrzucony.
Przy odbiorze wyrobów określa się także wytrzymałość betonu, którą ustala się na podstawie wyników badań próbek kontrolnych i wyrobów gotowych. Próbki kontrolne o krawędziach 10, 15 i 20 cm należy wykonać w metalowych formach dzielonych w ilości co najmniej 3 sztuk. co najmniej raz na zmianę, a także dla każdego nowego składu mieszanki betonowej.
Mieszankę betonową w próbkach zagęszcza się na standardowej platformie wibracyjnej z amplitudą 0,35 mm i częstotliwością 3000 impulsów/min. Próbki muszą twardnieć w takich samych warunkach jak produkty. Wytrzymałość betonu na rozciąganie określa się po badaniu próbek na prasach hydraulicznych i oblicza jako średnią arytmetyczną wyników badań trzech próbek.
Badanie gotowych wyrobów żelbetowych pod kątem wytrzymałości, sztywności i odporności na pękanie przeprowadza się zgodnie z GOST i specyfikacjami technicznymi. Do badania wybiera się produkty w ilości 1% z każdej partii, jednak nie mniej niż 2 sztuki, jeżeli w partii jest mniej niż 200 sztuk. produkty. Badanie przeprowadza się na specjalnych stanowiskach badawczych, obciążając konstrukcję za pomocą podnośników hydraulicznych, odważników lub urządzeń dźwigniowych. Kryterium wytrzymałościowe jest obciążenie, przy którym wyrób traci swoją nośność (zapada się). Ostatnio do określania wytrzymałości betonu w konstrukcjach stosuje się metody fizyczne i mechaniczne, które nie niszczą produktu.
Metody fizyczne obejmują ultradźwiękowe i radiometryczne. Metody mechaniczne opierają się na określeniu wielkości odkształcenia sprężystego lub plastycznego. Urządzenia do tych metod dzielą się na urządzenia działające na zasadzie sprężystego odbicia oraz urządzenia oparte na zasadzie wnikania końcówki w beton. W pierwszym przypadku wytrzymałość betonu ocenia się na podstawie wielkości odbicia sprężystego wybijaka od powierzchni betonu, w drugim charakteryzuje się ona wielkością odcisku na powierzchni betonu. Urządzenia tej grupy znajdują szerokie zastosowanie w budownictwie.
7. SPOSOBY DALSZEJ PRODUKCJI PREFABETONÓW
W ostatnim czasie szczególnie szybko rośnie produkcja prefabrykatów żelbetowych w ZSRR. W 1970 r. jej produkcja wyniosła 85 mln m3, czyli o 70% więcej niż w 1964 r. W obecnym pięcioleciu następuje dalszy rozwój prefabrykatów żelbetowych, będących podstawą industrializacji budownictwa. W sumie na rozwój produkcji prefabrykatów żelbetowych przeznaczono ponad 800 milionów rubli. i bardzo ważne jest, aby właściwie wykorzystać te duże środki przy projektowaniu nowych i przebudowie istniejących przedsiębiorstw. Niezwykle duże znaczenie w tym przypadku ma wybór racjonalnego schematu technologicznego wytwarzania wyrobów żelbetowych, w zależności od wydajności projektowanego zakładu, asortymentu wyrobów, rodzaju zbrojenia, wymiarów wyrobów i innych czynników .
Wybierając schemat technologiczny produkcji warsztatu formierskiego i parowego, należy wziąć pod uwagę zakres wytwarzanych produktów i wielkości produkcji, określone przez racjonalny promień transportu gotowych produktów. W przypadku produkcji wyrobów żelbetowych na małą skalę w fabrykach o małej i średniej wydajności najbardziej opłacalna jest metoda produkcji kruszywa. Przy prostym wyposażeniu technologicznym, małych powierzchniach produkcyjnych i niskich kosztach budowy, metoda ta pozwala na uzyskanie wysokiego uzysku gotowych wyrobów z 1 m2 warsztatowej powierzchni produkcyjnej. Metoda pozwala również na szybką zmianę sprzętu i przejście od formowania jednego rodzaju produktu do drugiego bez znacznych kosztów. Wydajność jednostki formierskiej uzależniona jest od rodzaju i wielkości formowanych wyrobów i zmienia się przy takim przejściu, co spowodowane jest zmianą czasu trwania cyklu formowania wyrobu, który może wahać się w szerokim zakresie – 5-40 minut .
Metoda kruszywa przepływowego jest najczęstszą metodą we współczesnej technologii prefabrykatów betonowych.
Pod względem kosztów kapitałowych przewaga pozostaje w przypadku ławki
metoda formowania produktów na stojakach poziomych. Tylko
ten sprzęt, jego znikome zużycie energii, możliwość
którzy przechodzą na produkcję wyrobów o szerokiej gamie standardowych rozmiarów,
minimalna liczba operacji transportowych - podstawowa godna
właściwości tej metody. Jednakże podczas poziomego formowania produktu
na stoiskach istnieje duże zapotrzebowanie na produkcję
kwadraty. Niski poziom mechanizacji powoduje dużą pracę
pracochłonność, 2-3 razy większa niż np. pracochłonność produktu
wytwarzanie wyrobów w technologii kruszywa przepływowego. Aplikacja jest niewielka
Do zagęszczania betonu możliwe są mocne wibratory przenośne
mieszanki o dużej mobilności, co powoduje nadmierne zużycie cementu. Wszystko
czynniki te wykluczały możliwość organizacji produkcji
produkty produkowane masowo (płyty i panele podłogowe, panele i bloki
ściany, bloki fundamentowe i płyty) w technologii ławkowej. Jeden
Jednak przy małej średniej rocznej wielkości takich produktów produkcja na skalę laboratoryjną
Szloch może okazać się najbardziej racjonalny; wskazane jest również kiedy
organizacja produkcji wyrobów żelbetowych w trybie tymczasowym
instalacje ligonowe.
Racjonalność stosowania metody ławkowej wzrasta wraz ze wzrostem masy i wymiarów wyrobów, których przemieszczanie przez oddzielne stanowiska technologiczne wiąże się z dużymi kosztami lub jest praktycznie trudne do zrealizowania. Dotyczy to kratownic i belek o długości 18 m i większej, przęseł mostów o masie do 100 ton i więcej, łuków i innych unikalnych prefabrykatów betonowych o znacznej masie. To decyduje o technicznych i ekonomicznych zaletach metody laboratoryjnej w wytwarzaniu tych wyrobów. Technologię ławkową najczęściej stosuje się na składowiskach otwartych o wydajności do 10-15 tys. m3/rok. Ważne jest, aby metodą produkcji ławkowej sprzęt można było łatwo zdemontować i równie łatwo zmontować na każdej budowie. Wydajność stojaka zależy od czasu przechowywania produktu. W zależności od rodzaju produktu czas utrzymania produktu na stoisku waha się od 20 godzin do 5 dni.
Metoda przenośnikowa do produkcji wyrobów żelbetowych umożliwia osiągnięcie kompleksowej mechanizacji i automatyzacji procesów technologicznych ich produkcji. Organizacja produkcji metodą przenośnikową zapewnia znaczny wzrost wydajności pracy i wzrost wydajności gotowych produktów przy najbardziej kompletnym i efektywnym wykorzystaniu sprzętu technologicznego. Należy jednak zaznaczyć, że technologia przenośników wymaga dużych inwestycji kapitałowych. Jego zastosowanie jest racjonalne w fabrykach o masowej produkcji wyrobów według ograniczonego asortymentu i minimalnej liczby standardowych rozmiarów.
Wyroby w kasetach produkowane są w pozycji pionowej (na krawędzi), co okazuje się bardzo wskazane przy wytwarzaniu cienkich wyrobów płaskich o dużej powierzchni (przegrody ścienne, panele podłogowe). Specyficzne zapotrzebowanie na powierzchnię warsztatu produkcyjnego metodą kasetową jest minimalne i na niewielkiej powierzchni zajmowanej przez kasetę formuje się jednocześnie aż 12 produktów o powierzchni do 12 m2 każdy. Istotną zaletą tej metody jest brak platform wibracyjnych i komór odtwarzających. A mimo to ma bardzo istotne braki. Tylko dostatecznie mobilna mieszanka może zostać skutecznie zagęszczona w kasecie z głębokimi przegrodami, a osiąga się to poprzez uzyskanie betonu o danej wytrzymałości przy zwiększonym zużyciu cementu. Wadą metody kasetowej jest również ograniczony asortyment produktów: w kasetach o konstrukcji wielosekcyjnej można formować wyłącznie produkty płaskie o pełnym przekroju. Sposób wytwarzania wyrobów za pomocą walcarki wibracyjnej ma podobne zalety i wady: charakteryzuje się wysokim stopniem mechanizacji procesu technologicznego, ale wymaga bardzo dużych nakładów inwestycyjnych.
O wyborze schematu technologicznego i organizacji formowania wyrobów decyduje wiele czynników, z których najważniejszymi są możliwości produkcyjne przedsiębiorstwa, rodzaj i wielkość wyrobu, wykonalność techniczna i ekonomiczna mechanizacji i automatyzacji procesów, charakter mieszanek betonowych stosowanych w danej metodzie. Prawidłowa ocena wymienionych czynników ostatecznie determinuje racjonalną technologię, która jest najkorzystniejsza w danych warunkach. Budując wytwórnie prefabrykatów betonowych należy dążyć do jak największej koncentracji produkcji, gdyż pozwala to na większą specjalizację poszczególnych linii produkcyjnych i zapewnia najlepsze wykorzystanie inwestycji kapitałowych.