Aerated concrete blocks or foam concrete blocks, which is better. What is the best to use for construction. Consider the advantages and disadvantages of each of the materials
V recent times aerated concrete is increasingly chosen as a material for building a house - artificial construction material with a porous structure, one of the varieties of lightweight concrete. They build from this material both cottages and apartment buildings... Moreover, such buildings are distinguished by better thermal insulation characteristics in comparison with brick ones and are much stronger than those in the construction of which a cinder block was used.
Due to their shape and small deviation in size, aerated concrete blocks can be laid not on cement mortar, which is a kind of cold bridge in the finished wall, but on special glue, which significantly reduces the heat transfer of the walls.
There are three methods of porosity of such concrete: foaming, gassing and aeration, due to which aerated aerated concrete and silicates are obtained.
A similar material began to be used for the construction of buildings back in the 19th century, when builders began to pour bovine blood to the cement-lime mortar, the protein of which, when reacted with the solution, formed a foam. Neither then, nor in the 30s of the last century, cellular concrete did not become widespread and began to gain popularity relatively recently, as a lighter and more inexpensive building material in comparison with brick. It is quite durable, retains heat better and easily removes excess moisture from the room to the outside.
Today, it is quite possible to build houses with a height of up to three floors from high-density foam concrete blocks. If the construction of the house involves the construction of a reinforced concrete supporting frame, then buildings of any number of storeys can be erected from foam blocks.
There are several types of foam concrete blocks, different in density, thermal conductivity and frost resistance.
To obtain aerated concrete, special substances are introduced into the cement slurry that emit gas and provide a more even porous structure than in the production of foam concrete.
Features of the production of foam blocks and gas blocks
Foam concrete is obtained by simply mixing pre-prepared foam with a concrete mixture. Such production is much simpler and cheaper than the production of aerated concrete and it can be organized, in fact, at any construction site, while reducing transportation costs to zero. The relative simplicity of the production of the foam block is very similar to the cinder block, which can be made from cement, water and screening in any yard. However, it should be borne in mind that in this case, the quality of such foam blocks can be questioned.
Receive foam concrete blocks can be done in three ways.
First- the mixture for blocks is poured into cassette metal molds, where it hardens for about 10 hours. After that, the form is disassembled and ready-made foam blocks are taken out of it. At the same time, almost the only thing that distinguishes the cinder block is that pre-prepared foam is not added to the mixture for its production.

Second way involves pouring a large massif of foam concrete with a volume of 2-3 cubic meters. Such an array solidifies for about 14 hours after which the entire massif is cut into pieces on a special cutting machine. This method is better because you can get a foam concrete block of any size. In terms of cost, this method is more expensive than the first. In addition, with this method of producing foam blocks, about 0.5% of concrete is wasted when sawing.
With the third method of production, foam concrete is fed into special forms, which, after solidification of the mass, are taken to automatic stripping. The finished blocks are squeezed out of the molds onto a special pallet, and the block molds are automatically lubricated. The main disadvantage of this method is that such an installation cannot be reconfigured, it can produce foam blocks of only one shape and size.
Any Internet forum where construction issues are discussed is ready to offer a finished video of the production process of foam concrete blocks, as well as cinder blocks.
In the production of aerated concrete, not a previously prepared foam is added to the concrete mixture, but a foaming agent - an aqueous suspension of aluminum powder, which reacts with the fillers of the mixture. As a result, hydrogen bubbles up to 2 millimeters in diameter are formed in concrete, which are evenly distributed throughout the material. After preliminary hardening of the mixture, the mass is cut into blocks of equal size, which are heat treated in an autoclave.
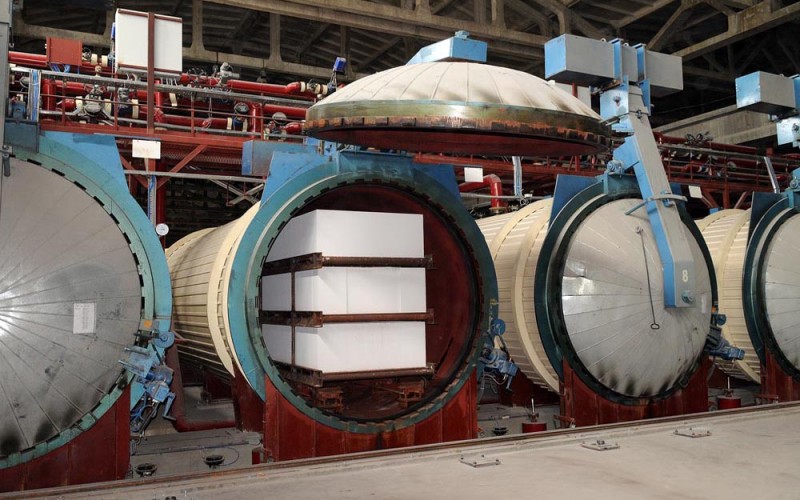
Professional skills are required to use such equipment. But the finished blocks are characterized by high frost resistance and resistance to cracking, they can be easily used in the construction of houses and other buildings.
With the non-autoclave method of aerated concrete production, the cut blocks are left to harden under natural conditions. This method of production is more economical due to reduced energy consumption, but it also has a significant drawback.
So, with the same material density, non-autoclave concrete shrinks by 2-3 millimeters, while during heat treatment the shrinkage does not exceed 0.3 mm.
In addition, with this method of production, the technology also involves an increased consumption of cement.
Thanks to this, it is the autoclaved aerated concrete block that has become more widespread.
Pros and cons of foam concrete and aerated concrete blocks
The advantages of foam concrete and aerated concrete over traditional, familiar building materials are similar. Aerated concrete and foam concrete blocks weigh less bricks and are more durable than cinder block, the very name of which, as some builders joke, speaks eloquently about the quality of this material. They are easier to transport and, thanks to their low weight, save at the very beginning of construction by laying a lightweight foundation in the base of the building. At the same time, the main differences between foam concrete, along with its lower cost, are its disadvantages. Aerated concrete is easy to process
Aerated concrete blocks of both types are easily assembled together. Therefore, the construction of walls of houses from such blocks requires a third less time than walls from ordinary brick, but at the same time, aerated concrete also lends itself much better to additional processing. What other stone, albeit artificial, can be cut with an ordinary hacksaw if necessary? Even cinder blocks are less pliable to cut.
Hygroscopicity and frost resistance
Both materials have low moisture resistance, so the walls of houses from them need additional processing with different compositions. Aerated concrete block absorbs moisture better due to the fact that the pores in it are not only closed, as in foam concrete, but also open. It removes excess moisture from the room and “breathes” much better due to its porosity. In conditions of high humidity, the facade of a building made of aerated concrete will need to be additionally protected from direct moisture penetration.
Due to its porous structure, there is always a reserve space inside the blocks for the movement of water when it freezes. Therefore, frost resistance of foam concrete ranges from F15 to F50.
Autoclaved aerated concrete, in turn, is able to withstand about 200 freezing cycles, which corresponds to approximately 500 years of wall service life. Moreover, GOST requires only 35 freezing cycles for this material.
Strength
Foam concrete and aerated concrete blocks can be manufactured with different material density: from 300 to 1200 kg / m3.
However, with equal density, the foam concrete block is noticeably inferior to autoclaved aerated concrete in strength, which largely depends on the quality of the foaming agents.
Since foam concrete can be made almost artisanally, many manufacturers instead of high-quality components of mixtures use their cheaper counterparts. At the same time, the cost price of foam concrete blocks decreases, but their quality as a building material does not get better.
Shrinkage
Autoclaved aerated concrete block masonry is less prone to cracking than a foam concrete wall. The shrinkage of autoclaved aerated concrete usually does not exceed 0.5 mm per 1 meter of masonry. At the same time, for foam concrete blocks, shrinkage can reach 3 mm / m.
Thermal insulation
The thermal conductivity of foam blocks is three times lower than that of ordinary bricks. What distinguishes them from aerated concrete blocks is that the pores inside the block are unevenly distributed and can vary greatly in size. Somewhere it turned out more, somewhere - less, and in some place it did not form at all. Because of this, it is difficult to argue that even one block of foam concrete is able to provide the same level of thermal conductivity throughout its entire volume.
The texture of aerated blocks has more pores and they penetrate the entire material evenly. Therefore, their thermal insulation qualities are better than that of foam blocks.
Only a cinder block can have a lower thermal conductivity than that of aerated concrete blocks. However, in his case, thermal conductivity largely depends on what material was used in its production.
Fire resistance
Due to its structure, aerated concrete does not support combustion and does not spread fire. By visiting any construction forum, you can be convinced that, according to reviews, a masonry of aerated concrete blocks with a thickness of only 20 cm is quite capable of stopping the spread of a fire.
Foam concrete also belongs to non-combustible materials and is able to withstand one-sided exposure to fire for 5-7 hours.
Price
Aerated concrete, especially autoclaved concrete, is significantly more expensive than foam concrete or cinder block. This happens for the simple reason that was already mentioned earlier - foam concrete can be produced almost everywhere. You can even make it just by reading reviews and visiting the construction forum, where they will not only help you understand the production technology. Videos of the production process can also be offered by people visiting such a forum, and with practical advice, if anything, they will help.
Equipment for the production of autoclaved aerated concrete is expensive; only large enterprises can afford it. Therefore, this material is significantly more expensive.
Dimensions (edit)

Only one foam or gas block can replace 15–20 bricks in the masonry.
Moreover, the wall of the house made of these materials will be much lighter. The concrete blocks themselves can be produced in various sizes. It all depends on the equipment on which this building material is produced.
Houses made of foam and aerated blocks compare favorably with brick houses, primarily in their lower cost. When building them, the foundation and masonry and the material itself are cheaper. Among other things, such houses will be cheaper to maintain. It is much easier to heat a room with aerated concrete walls.
What's the best for building?
Any forum where the subtleties of construction are discussed can accommodate enough supporters and opponents of the use of both materials. Some prefer the availability, simplicity and low cost of production. The second nicer is the good old brick and cinder block. Others believe that the quality of construction can be guaranteed only if materials produced in large-scale production with expensive equipment are used. Both the foam and the gas block deserve both negative and laudatory reviews. Each of the materials is distinguished by its undoubted advantages and disadvantages.

In addition to the production process, using the video, you can appreciate the simplicity and subtleties of the masonry of walls made of foam concrete and aerated concrete. The simplicity and convenience of this process play an important role.
The choice of material for construction can be influenced by many factors. The price consists of the cost of the material itself, the cost of its installation, operational characteristics, availability, the purpose of the building being erected, and much more.
The construction of a residential building is a special process that does not tolerate errors, especially in terms of durability and comfort. Especially in our latitudes, where the temperature regime can vary significantly, as well as weather conditions. The choice of quality material in this case is an important mission, and one who knows what he is looking for can cope with it. Today we consider two materials widely used in modern housing construction - aerated concrete and foam concrete, compare them and assess each material according to several characteristics.
Foam concrete is essentially cement, sand and a foaming agent. All this is mixed, poured into molds and left alone until completely solidified. That is, the process can be carried out directly at the construction site.
Foam block and gas block - appearance
But aerated concrete requires a high temperature and a humid environment. It is composed of lime, cement, water and sand. Aluminum powder in this composition acts as a blowing agent. The resulting mixture is cut into blocks with strings and poured into an autoclave. There, under the influence of high pressure, the material acquires its final appearance and its best qualities - resistance to mechanical stress, durability, fire resistance and pliability to processing.
It turns out that both materials are lightweight concrete, only the method of obtaining air bubbles in them is different.
Both materials are manufactured according to the same GOST, which means they meet the same requirements. Their physical and technical characteristics almost repeat each other. But this does not mean the complete identity of aerated concrete and foam concrete.
Aerated concrete in its heat treatment has some advantages, but it is not necessary to claim that it is superior to foam concrete. Nevertheless, it is the quality of the cement and its density that determine the degree of quality and reliability of the product. The laying of these two materials is also different: aerated concrete blocks are placed on glue, and aerated concrete blocks on ordinary cement mortar. It is cheaper than glue, but practice shows that much more of it is required, and it is more difficult to work with it.
It turns out a curious thing - aerated concrete together with glue are more expensive than foam concrete with cement mortar, but at the same time, the cost is almost the same. In addition, the glue does not allow cold bridges to arise, which means that it will be easier to warm the interior, which will have a positive effect on cost savings.
Another difference between materials is the degree of accuracy in block sizes. Still, the dimensions are respected much more accurately at the factory than at the construction site. Therefore, aerated concrete is easier and more pleasant to lay.
Comparative table of characteristics of foam concrete and aerated concrete
Advantages and disadvantages
If we talk about the production of materials, then foam concrete from the point of view of the complexity of the process looks preferable. For aerated concrete, it is necessary to build a workshop, conduct a powerful electrical network, a gas pipeline. The foam block is easy to make on portable equipment, which is easy to find - there are enough modifications of them on sale. Another thing is that simplified way production often attracts illiterate manufacturers who do not pursue the accuracy of linear dimensions, compliance with the level of thermal conductivity, density and strength. You can avoid encountering low-quality products by finding a competent manufacturer who has all the necessary quality certificates in his hands and periodically tests his products for compliance with the requirements of modern standards.
Blocks of aerated concrete and aerated concrete are easy to install, and due to their size, they save glue or cement mortar
Foam concrete can be toxic - since it is not autoclaved, chemical processes are used to create it. This also affects the strength of the product. With the same density index, the degree of strength of aerated concrete and foam concrete is different. Take, for example, a density of 500 units. Aerated concrete with this indicator copes well with loads, while foam concrete cannot boast of high strength and is used only as insulation.
Water absorption and frost resistance are two important indicators for a material.
The gas block is able to absorb more water than the foam block, but at the same time it is less resistant to low temperatures. True, during the construction residential buildings their outer side is covered with a protective layer in the form of plaster, tiles, siding and other materials, which means that the gas block will be protected from water.
Video: characteristics of gas and foam blocks
Home construction
Houses built with these materials will cost less than brick ones. And there are reasons for this. Firstly, aerated concrete and foam concrete are lightweight materials, which does not oblige the builder to build a massive foundation. A light version of it is enough. Secondly, the heat and sound insulation of both materials is at the same level, which allows you to subsequently save money. And not only in the future. During the construction process, walls can be erected with a smaller thickness, which means savings on materials. Thirdly, the savings in materials also apply to glue with cement, which, with large volumes of blocks, will not be required so much.
Houses made of foam blocks and gas blocks are very reliable, because these materials are durable and non-combustible. They do not rot and are not susceptible to attacks by rodents and insect pests.
If you will be laying intra-house structures, such walls will be easy to gouge. And, finally, the most important thing is that these walls "breathe", which creates a comfortable living environment in the house.
The total purchase cost of aerated concrete with cement mortar and aerated concrete with glue is approximately the same
Photo gallery: aerated concrete in construction
Walls made of gas and foam blocks 'breathe' and provide comfort in rooms
Aerated concrete houses are easy and quick to build
Gas and foam concrete are economical materials that provide the required wall thickness at a relatively lower consumption
Gas blocks have high thermal conductivity
It turns out that no one material has a clear advantage over the other. Each has its own set of advantages and disadvantages, which means that before deciding on any of them, you need to carefully analyze their features and choose for yourself what you think is best suited for building a future home.
When there is talk about aerated concrete and foam concrete blocks, you can often come across the fact that not everyone understands well what kind of materials they are and what is the difference between them. Aerated concrete and aerated concrete are united by the fact that they belong to aerated concrete, i.e. have a porous structure. This provides them with high performance in terms of thermal insulation properties, ease of processing and use, good strength and reliability, and, most importantly, a relatively low price - after all, a brick wall will cost much more. But aerated concrete and foam concrete also differ from each other, which is due to some differences in their manufacture, hence the difference in some technical properties. It is impossible to say exactly which material is better, but we hope that after reading this material you will form the correct conclusion for yourself.
Features of the production of foam concrete blocks
The most important the differences between foam concrete and aerated concrete should be sought in the technology of their production.
So, foam concrete blocks are obtained by adding special foaming additives of organic or synthetic origin to an ordinary cement mortar. The foam is formed on the basis of water, and the water itself evaporates naturally during the drying process. Foaming additives foam the concrete, thereby filling it with air bubbles. Such bubbles are distributed throughout the entire volume of concrete, and after hardening, they make it much easier, adding heat-insulating and sound-insulating properties.
Such a process can be carried out directly at the construction site, since special and high-tech equipment is unnecessary. Due to the shapes used in the manufacture of the foam block, finished products may differ in size, sometimes by 10-20 mm.
Features of the production of aerated concrete blocks
To obtain aerated concrete, you need quartz sand, lime, cement and water, as well as a special component - aluminum powder, due to which bubbles are formed that fill aerated concrete. The mixture hardening process takes place in autoclaves at a sufficiently high temperature and high pressure, and not under natural conditions, as is the case with foam concrete. And since special equipment is used for production, all the characteristics of the future aerated concrete block can be controlled, making them the same throughout the volume. This cannot be said about foam concrete, which, when frozen on the street, can have a slightly heterogeneous and unequal structure and properties. And the shape of the gas blocks produced in this way is ideal, has minimal deviations from each other, which cannot be said about foam concrete, for which shapes are often used that are not able to ensure accuracy and evenness.
Such processing allows aerated concrete blocks to have a number of other advantages over foam concrete, which will be discussed below.
Advantages of aerated concrete over foam concrete
Advantages of foam concrete over aerated concrete

conclusions
From everything written above, it follows that in some characteristics, foam concrete and aerated concrete blocks are similar, while foam concrete is cheaper. Thus, foam concrete can be suitable for a certain type of construction, where some of its disadvantages will not fail. Aerated concrete, on the other hand, has more attractive properties in comparison with foam concrete: largely due to the production technology. And besides, if you count all the waste on installation, then building from aerated concrete blocks may not be more expensive than building from foam concrete blocks. Everyone should make the final choice before starting construction, but in most cases, the use of aerated concrete blocks remains justified.
Both foam concrete and aerated concrete belong to the class of lightweight concrete, that is, they are related materials. The main difference between aerated concrete and aerated concrete is the way air bubbles form inside these materials. But this, at first glance, a slight difference ultimately leads to the production of two different materials, markedly different in their characteristics.
Despite the similar appearance, foam concrete and aerated concrete have a number of significant differences.
Differences in the production of aerated concrete and aerated concrete
For the manufacture of aerated concrete, a mixture of lime, sand, cement, water is used. Aluminum powder is added to this mixture as a blowing agent. This mixture, cut into blocks, is loaded into an autoclave, where, under the influence of high humidity, high temperature and high pressure, it undergoes a long processing. The result is a wonderful building material, non-combustible, strong enough and easy to process.
For the manufacture of foam concrete, a cement-sand mixture is used, additionally adding a foaming agent to it. The mixture is thoroughly mixed and poured into forms, in which the formation of foam blocks occurs naturally. This technology allows them to be made directly at the construction site.
Despite the fact that both materials are manufactured according to the same GOST and have very similar physical and technical characteristics, gas blocks and foam blocks still have noticeable differences between themselves, primarily in price. Foam concrete is not only easier to manufacture, but also much cheaper than aerated concrete produced exclusively in the factory. In addition, gas blocks are laid on special glue, and foam blocks - on ordinary cement mortar, which is also much cheaper than glue.
Differences in respect of the dimensions between foam concrete and aerated concrete are also possible. This happens again, because the gas block is manufactured in the factory and the proportions of its blocks are observed much more accurately than that of foam concrete created mainly by artisanal or, at best, semi-artisanal method.
But it is still impossible to say unequivocally that a house built of foam concrete will cost less than a house of the same size made of aerated concrete. The amount of glue used for laying gas blocks is much less than the amount of solution for laying foam blocks, so it turns out that laying gas blocks is much cheaper than foam blocks. It should also be borne in mind that due to fluctuations in the size of the foam blocks, the consumption of the solution for laying them increases even more.
Back to the table of contents
Differences in the technical characteristics of materials
Despite the fact that aerated concrete and aerated concrete are similar, there are still significant differences in their technological characteristics:
- by strength;
- by the structure of porosity;
- thermal conductivity;
- by hygroscopicity.
The difference between aerated concrete and its counterpart in strength is most striking. With the same density of blocks, aerated concrete is 3-3.5 times stronger. For example, with a density of D500, the strength of aerated concrete is 30-34 kg / cm², and foam concrete is only 9 kg / cm². In practice, this means that the foam blocks will float on the surface of the water, and the gas blocks will be submerged in the water. But the statement that the gas block is drowning in water, found in some sources, does not correspond to reality. It does not sink, but it is immersed in water, depending on the density, by 1/3, 1/2 or 2/3 of its volume.
With the same porosity, aerated concrete has an open pore structure, and aerated concrete has a closed one, i.e. the bubbles inside the material are isolated from each other. In practice, this means that foam concrete walls do not breathe well. But at the same time, this allows the foam concrete to release less heat through the walls of the house and let in less cold.
For a wall made of aerated concrete, water ingress is unacceptable, therefore, it can be used in a humid climate only simultaneously with a reliable waterproofing device. Foam concrete is much less afraid of water, therefore, a layer of insulation is enough to protect it from moisture.
Back to the table of contents
Aerated concrete or foam concrete: which is better?
Building a house from these lightweight concrete will, in any case, be much cheaper than using traditional materials. Firstly, it is precisely because of the lightness of the materials that such houses do not need massive foundations. Secondly, both of these concretes have much better heat and sound insulation than traditional materials, therefore, this allows you to reduce the thickness of the walls. Thirdly, the blocks are much larger than bricks, which allows you to significantly speed up the construction of a house.
Both aerated concrete and aerated concrete are non-combustible materials. Both materials are of no interest to rodents or insect pests, and in addition they are not susceptible to decay. Both materials, albeit to varying degrees, are breathable, which has a beneficial effect on the microclimate inside the house.
No one will give an unequivocal answer to the question of which is better. In some cases, it is better to use gas blocks for construction, in others - foam blocks.
But still, in most cases, aerated concrete is preferable.
For example, it is better not to use foam concrete for construction. load-bearing walls, and the strength of aerated concrete allows it to be used in construction load-bearing structures but limits their height to a maximum of 2 floors.
Aerated concrete in its environmental friendliness ranks second after wood. The chemical additives used for the preparation of foam concrete cause certain concerns among environmentalists. Although there is still no specific information about the dangers of foam concrete for human health.
Also, during construction, it should be borne in mind that autoclaved aerated concrete practically does not shrink, but foam concrete made by natural hardening in this respect is by no means perfect. In practice, this means that in a wall made of foam concrete there is always a risk of cracks due to shrinkage that have occurred.
In places with a humid climate, it is definitely better to use foam concrete for construction. But the statement that foam concrete better retains heat inside the house is not confirmed in practice. The wall laid out of gas blocks planted on glue has practically no cold bridges, which cannot be said about the wall laid out of foam blocks planted on mortar. With the same wall thickness, due to the greater strength of the material, a house from gas blocks often turns out to be even warmer than from foam blocks.
The high hygroscopicity of aerated concrete is the main reason for its low frost resistance. But in practice, during the construction of residential buildings, this drawback turns out to be not so great, since the walls of both materials need finishing. It can be plaster, facing tiles, siding. In any case, the finishing protects the wall material from moisture, therefore, the difference in frost resistance can be ignored.
In the same case, if it is planned to build outbuildings for which frost resistance does not matter, it is better to build them from gas blocks. And if we are talking about small buildings for pets, then for them it is still better to use foam concrete.
The choice between aerated concrete and aerated concrete is really not easy. Manufacturers of both materials extol their merits and prefer not to mention their demerits. Therefore, before choosing, you need to carefully weigh the pros and cons, and not act impulsively. Only in this case your choice will be thoughtful, logical and the only correct one.
Increasingly, bricks are being replaced with foam concrete and aerated concrete, since building from these materials is faster and cheaper. Unlike heavy concrete, cellular concrete has pores, so the blocks weigh less and retain heat well. The price of a foam block is lower than that of a gas block, but reviews about its quality are scary. But if you choose aerated concrete, will it be safe? Decide on the basis of objective facts, there is a difference between the materials, we will consider it in this review.
What is the difference between a gas block and a foam block?
- Production technology.
Foam concrete is made from M500 cement, sand, water and foaming additives. The mixture is poured into molds and left to stand for 12 hours. For full readiness, the blocks are stored in special rooms for 28 days so that they gain brand strength.
The composition of aerated concrete includes sand, cement, lime, water and aluminum powder or paste, which provides the porous structure of the material. Aerated concrete made in high-pressure furnaces is called autoclave. Non-autoclave gas blocks must be matured in rooms with a specific temperature and high humidity.
- Strength and density.
High-quality foam and aerated concrete has the same density, it is designated by the letter "D". But due to the peculiarities of the production of foam concrete and non-autoclaved aerated concrete, it has a heterogeneous structure. Even a slight violation of the technology for 28 days of ripening leads to a lower density, which means that the strength decreases. Unscrupulous companies sometimes sell blocks ahead of time their readiness, so always ask for documents where the date of preparation of the mixture is indicated. If you have to buy material from an unknown company, it is better to leave the blocks indoors for a couple of weeks or outdoors under plastic. And construction from autoclaved aerated concrete can be started right away.
Autoclaved aerated concrete is much better than foam blocks, since its structure is homogeneous, which means that it will not crack, and its characteristics will correspond to the marking. For the construction of external walls, aerated concrete D400 ‒ D500 is suitable, and aerated concrete must be bought from D800, or the walls should be made thicker.
- Frost resistance and moisture resistance.
Since the production technologies are different, the cavities in the foam concrete are not interconnected, and in the aerated concrete there are channels between them. The moisture resistance of high-quality foam blocks is higher, but they conduct heat worse. It is not recommended to build baths or walls and partitions in toilets and bathrooms from gas blocks. Whatever material you use, you will still have to additionally isolate cellular concrete from moisture if you want to live well and comfortably in the house.
- Security.
High-quality building materials will always be safe, and blocks made incorrectly turn out to be non-environmentally friendly. Sometimes slag is added to the mixture, and if it is not kept for several months, then it begins to emit harmful substances.
Lime, which is used for aerated concrete, is not harmful, since its molecular structure changes when the blocks are prepared in an autoclave.
- Shrinkage.
Aerated concrete is characterized by less shrinkage. It changes dimensions to 0.5 mm / m, and foam concrete - from 1 to 3 mm / m, so if you are building from foam blocks, be prepared for this. A reliable foundation will reduce the settlement of the structure, which means that the blocks will not crack. Buy ready-made foam concrete from trusted manufacturers, as the greatest shrinkage occurs due to improper storage conditions while the mixture hardens, or due to excess water.
- Geometry.
Differences in block sizes come from the cutting method. An autoclave gas block is more equal, since in a large production it is cut with special strings. Cheap foam concrete is made in small enterprises and cut by hand or on old equipment, because of this, the edges of the blocks do not match, because of this, more mortar is consumed, and the finished surface is primed to hide irregularities.
- Heat resistance.
Foam concrete retains heat well, but it is less durable, so the walls are made thicker. If you build from aerated concrete, you need a smaller wall thickness, which means you will save on material.
- Masonry process.
It is easier to work with foam and gas blocks than with bricks, since they are larger in size. To cut them, you do not need special equipment; this is done with a well-sharpened hacksaw. The only drawback is fragility, if the block falls, a crack or chip will most likely appear on it, so transport this material carefully.
Price
The difference in price between materials is palpable. Foam concrete is 20 - 30%, and they put it on a cement mortar, which costs less than glue for aerated blocks, so I want to choose it. But it is difficult to find high-quality foam blocks on the market, and having bought a dubious product, you will have to spend money on a primer, insulation or repair of blocks that are cracked.
One of the advantages of foam concrete, you can make it yourself and pour it into the formwork or make ready-made blocks for your size. Buying equipment is cheaper than transporting finished blocks. But the manufacturing process itself cannot be disturbed, do not violate the recipe of the mixture and prepare a warm and dry place for the ripening of the blocks within 28 days.
Home construction
Aerated concrete from D500 is best used for building a house. The grades below are used for the construction of partitions or for thermal insulation. High-quality foam concrete is suitable for small buildings. If you are building from monolithic foam concrete, it is important to withstand the structure or elements for 28 days, otherwise cracks will appear on the walls due to the foundation settlement.
Recently, tongue-and-groove aerated concrete blocks have appeared on the market. It is convenient to work with them, the masonry is stronger and smoother, and less glue is used. The masonry technology differs from manufacturer to manufacturer. For some, it is not necessary to apply adhesive to vertical edges. Before choosing, find out the features of working with the material, the composition of the mixture differs in different factories.
What blocks are best for building a bath?
Aerated concrete absorbs water more strongly, unlike foam concrete. However, a bath made of any material must be protected from moisture with a coating compound or roll insulation. But for the construction of a bath, foam concrete will be better only if you are sure of its quality.
- Partition solution.
For interior partitions, foam blocks from D600 are suitable. If you want good sound insulation, you can choose the brand above. Aerated concrete from D400 is also used to divide a room into parts, but it quickly absorbs moisture; builders do not recommend using it in wet rooms.
Before purchasing, check that the blocks are even in relation to each other, which makes it easier to finish the surface. To fix the cabinets on the walls, use a special screw questionnaire or screw the samozers into plastic dowels.
The main difference between the gas block and the foam block is the production technology. Often, autoclaved aerated concrete is of better quality, since it is made in large factories, but it also costs more. It is easier to make foam concrete, therefore, the percentage of questionable products is much higher here. And to a buyer who does not know the difference, you can sell any fake with a beautiful name. Because of such manufacturers, there are negative reviews on the network. Before choosing, calculate not only the price of the blocks themselves, but also add materials for thermal and waterproofing and finishing to them. Buy goods of the desired brand from well-known manufacturers and lay blocks according to technology, then a house made of any blocks will stand for a long time.