Types of basement floors and construction stages
The ground floor is a room in a building buried below ground level. It is used for arranging household premises, a garage and other purposes, such as a swimming pool, sauna. In some cases, building a basement is a cost-effective solution, especially if the terrain of the site is characterized by the presence of slopes. Due to the basement, the useful area of the entire building increases, so the basement in a private house is the right and thoughtful solution for any developer.
Ground floor: features and benefits
The underground level can serve as the foundation of the entire structure and living quarters. Features of construction in compliance with the requirements for strength, bearing capacity, dimensional space. The regulations show that the ceiling height cannot be less than 2.5 meters, however, sometimes the parameter is limited by the presence of a high occurrence of the ground aquifer, as a result of which it is allowed to build a basement floor above ground level. For example, if the level of the aquifer is only 1.5 m from the soil boundary, digging a foundation pit for construction is not recommended, in this case, backfilling the above-ground part of the basement with soil and artificially deepening the ground floor should be enough.
Advice! With proper construction, the basement can become not just a basement, but quite a living space with the proper level of comfort.
The basement is used for the following purposes:
- Storerooms;
- Garage;
- Premises for economic use (laundry, ironing, drying, furnace);
- Wine Vault;
- Living room;
- Game rooms;
- Pools;
- Bedrooms;
- Gym;
- Kitchen;
- Cinema.
There are no restrictions for private houses in using the ground floor, it all depends on the preferences of the owner, financial capabilities and practical application.
Plinth types
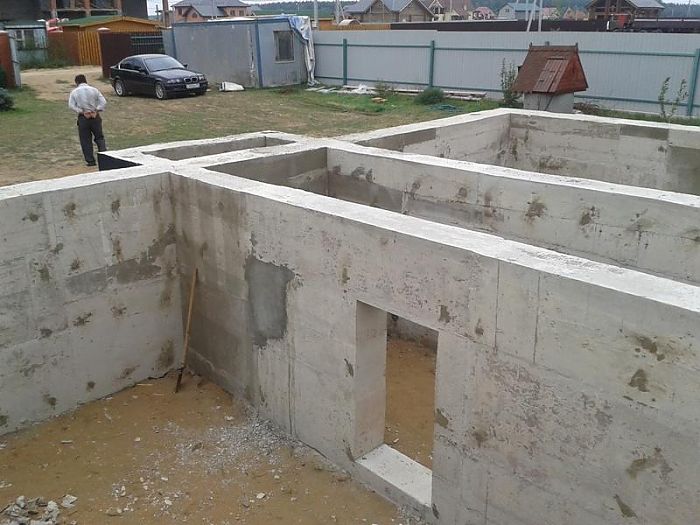
According to its design, the basement of the house differs in the following types:
- bulging. It is used in the case of too thin wall panels and for arranging rooms below ground level.
- Recessed. It is considered the most popular and has a practical application: drains from the facade prevent the formation of increased moisture in the house.
- Lined with wall panels. Experts sometimes do not consider it possible to use this option, since the very effect of the presence of the basement floor is lost, however, if the option of thorough waterproofing of the walls does not scare, the basement built in this way will fully meet all the requirements of comfort and practicality.
To make a plinth, it is necessary to take into account the thickness and material of the wall panels, as well as the strength characteristics of the soil, which are influenced not only by aquifers, but also by the climatic features of the region.
Construction calculations
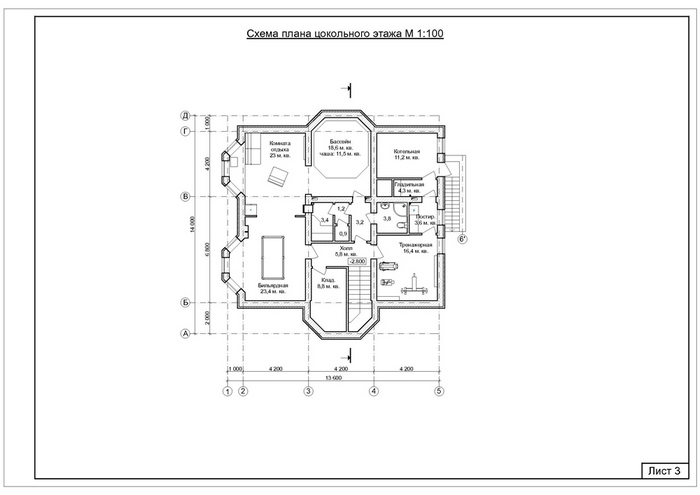
Determining the work on the construction of the ground floor, it is necessary to perform the following actions:
- Complete the design of the basement, taking into account the determination of the purpose of the premises;
- Calculate the load on the foundation and walls of the ground floor.
Advice! To be sure of the strength of the supporting base, it is recommended to add another 30% strength plus. In this case, the building will definitely withstand all the loads.
- Mark the construction site taking into account the basement.
- Outline the contours of wall panels and load-bearing partitions.
The last stages are difficult for an unprepared master to work independently, so it is best to seek help from a professional. The specialist will tell you exactly what size and format to equip the proposed basement floor so that it meets all the needs of the developer.
Foundation types
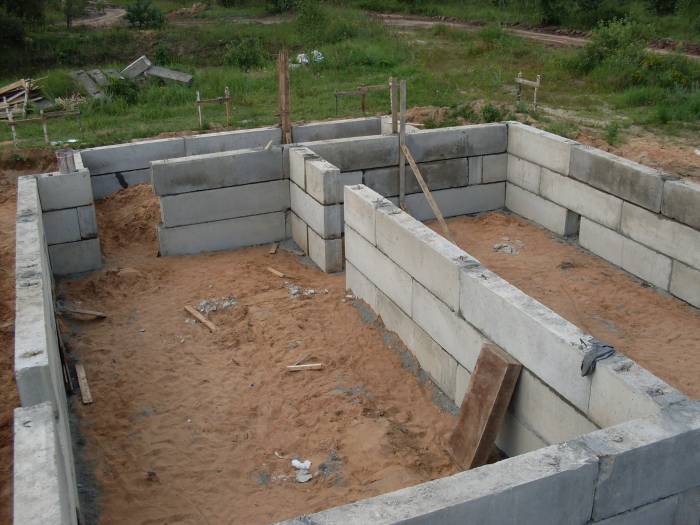
Sometimes the arrangement of the cellar is impossible due to the fact that the soil has a low bearing capacity. Therefore, it is worth knowing suitable for the basement:
- Pile base. Suitable for all types of soil except heavy. The operation of the ground floor is not difficult due to the special specifics of the structure of the entire building.
- slab foundation possible on weak soils with high water saturation. It is also possible to build a base in this case, but it will resemble a cube closed on all sides, on which the entire mass of the structure will lie.
- Strip foundation suitable for all types of soil, the construction of the base here also does not present any problems.
As for the width of the foundation, it depends on the characteristics of the wall panels of the house. Let's say this is a frame house with a basement floor, the dimensions are as follows:
- The pile base is 300-500 mm, while the thickness of the wall panels can be equal to the foundation. The construction does not have to be supplemented with ventilation holes, since the technology already implies these features.
- The slab base recommends the width of the foundation equal to the width of the walls of the basement.
- A shallow strip foundation is built along a width equal to the walls of the zero floor, but only if the zero level is not supplemented with a concrete screed.
As for waterproofing, it is recommended to perform at least 2 layers. In this case, coatings matter: it is necessary to cover all vertical and horizontal elements of the structure, as well as joints adjacent to the ground. For waterproofing, roofing material, roofing felt, mastics on bituminous bases are used.
Stages of building a basement
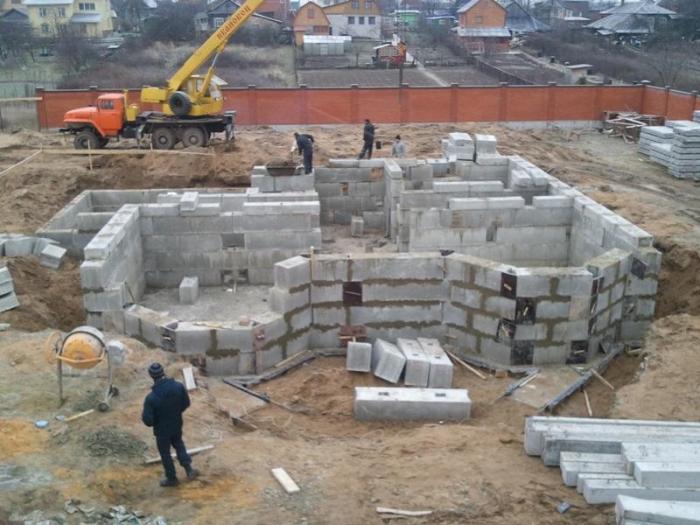
Step-by-step instructions will tell you how to make a basement, and photo and video materials will give answers to all questions. It’s worth starting with processes, the implementation of which is mandatory, regardless of the foundation and type of structure:
- Foundation laying;
- Filling works;
- Waterproofing, insulation;
- Facing;
- Installation of floors, ceilings.
So, how to build a ground floor or cellar in your own house.
Foundation laying, pouring

- Mark the site, dig a pit at least 500-600 mm deeper than the underground part of the bearing base;
- Perform backfilling of gravel, sand with a thickness of 100 mm or more;
- Tamp the bedding, spill it with water and then the base is poured with concrete mix (M100 grade). Filling thickness not less than 5 cm;
- After the mixture has dried, waterproofing is laid (in 2 layers), a concrete floor slab is poured;
- An external formwork is being constructed, for which shields or boards are used;
- Be sure to make a reinforcing frame inserted inside the formwork;
- In places where wall panels are erected, a reinforcing bar is installed;
- Filling is carried out with concrete grade M250, M300 and higher;
- Plate thickness from 200 mm;
- Tamping is carried out around the entire perimeter of the fill;
- The drying process lasts 4-5 weeks;
- At the same time, it is possible to start the construction of formwork for wall panels and reinforce the walls longitudinally with reinforcement bars, which are tied up with the previously set bars in a vertical position;
- Be sure to provide openings for doors;
- Communications are then mounted in pre-laid metal pipes;
- The walls are poured both in layers and at the same time. When pouring in layers, each layer is compacted, while the next layer can be poured immediately, without waiting for the previous one to dry.
Important! The whole structure gains strength only after 28-30 days!
Waterproofing, insulation works
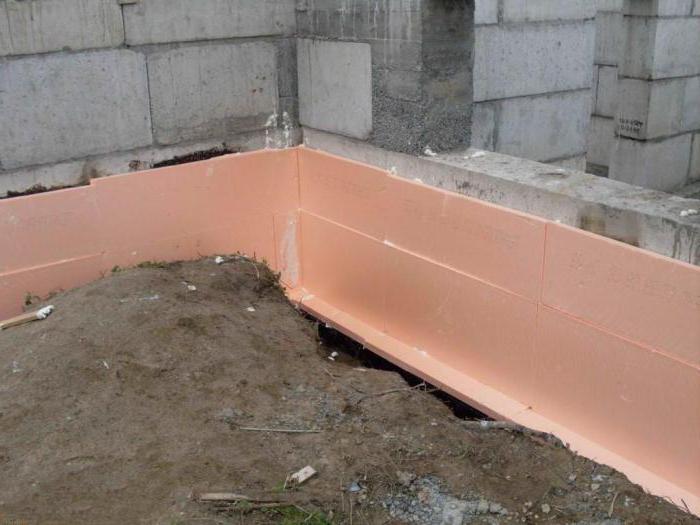
To see how to make the basement of the house warm and protected, watch the video. For waterproofing, adhesive-type compositions are used, but waterproofing should be done with penetrating materials that do not violate steam exchange processes and increase the strength of the structure.
In this case, the foundation frame should also be isolated, for example, with polystyrene foam plates, the fastening of which is carried out with a conventional adhesive solution. All that remains is to fill in the soil around the entire perimeter of the building and you will get a warm ground floor. Backfilling is carried out either with soil or sand, if the soil masses are large and hard.
Wall cladding, floor and ceiling installation
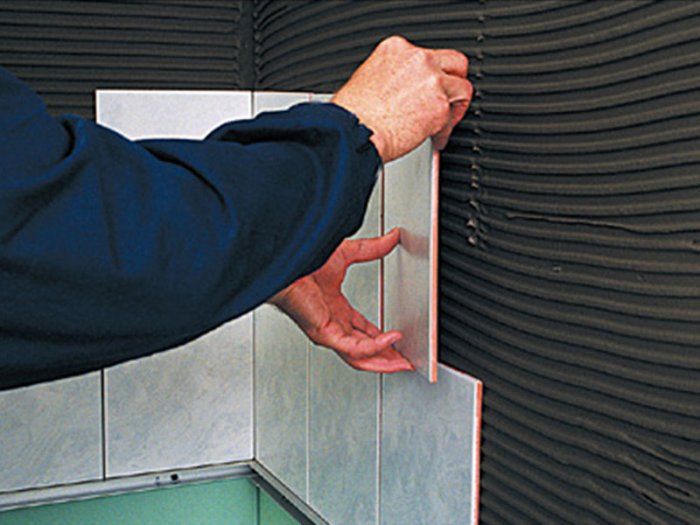
As for facing works, they are carried out with materials chosen by the developer. Natural stone, styrofoam-based slabs perform well, or you can choose siding. Interior decoration is also simple, depending on the purpose of the premises. Do not forget about communications, heating and additional thermal insulation of wall panels. Material for interior decoration is preferable with good moisture resistant qualities.
To begin with, the floors should be insulated with a sand cushion, then a roofing material should be laid, a reinforced grate on it, followed by pouring concrete mixture (M400 grade). Insulation with a “warm floor” system is allowed, on top of which a concrete screed is already mounted.
Overlappings are made depending on the chosen technology:
- Monolithic reinforced concrete slab;
- Prefabricated monolithic slab;
- Lumber cover.
For heavy slab elements, it is necessary to build a formwork, then fix the structural posts in 100 cm increments, make a reinforcing belt and install it, then pour a 200 mm thick concrete slab. Be sure to wait for the overlap to dry, and then proceed to the next stages of work.
Block plinth construction
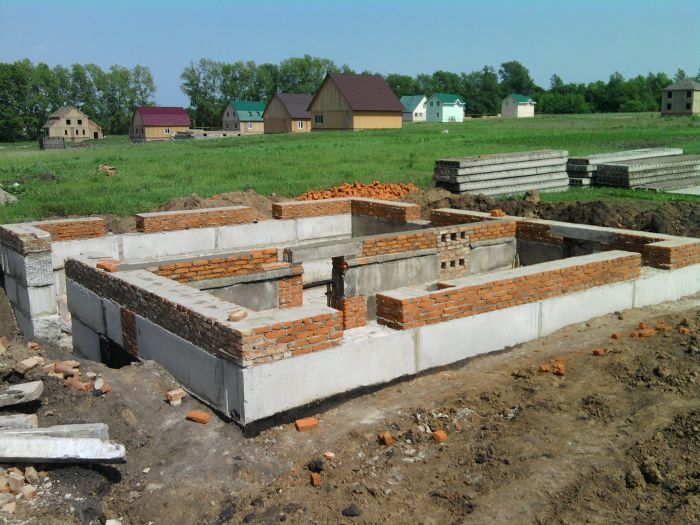
The construction of houses with a basement ground floor can be made from any material, so you should take into account different technologies for arranging the basement. For example, a concrete block is suitable. Possessing strength, non-susceptibility to decay, the material copes well with loads and at the same time the cost of the project is significantly reduced in price.