Frame-panel houses: advantages and disadvantages, varieties, self-assembly, cost comparison. Set of frame house made of wooden I-beams
Our company offers everyone who wants to purchase a kit frame house for self-assembly according to the most affordable prices in the region. You can buy ready-made parts and elements of the future structure and carry out the construction work yourself, which will cost much less than hiring specialists.
Advantages
Our projects are very diverse, which will satisfy the needs of any buyer. We offer house kits for one-, one-and-a-half, two-story buildings with attics and terraces.
Thanks to our kits, everyone can independently build their own home, which will be warm, cozy and as economical as possible. The main advantages of buildings made from SIP panels include:
- reliability;
- quick and easy construction in any climatic conditions;
- strength;
- high rates of heat, noise and waterproofing;
- affordable price;
- easy transportation;
- efficiency;
- eco safety;
- no additional costs for labor and technology.
It is possible to build a frame house from SIP panels in a month and a half with the efforts of three people. With proper care and timely replacement of worn parts, the service life of a building can be increased from 70 years to infinity.
Equipment
In a house kit for independent construction work includes:
- frame;
- foundation devices;
- details of roofing, insulation, finishing;
- SIP panels for walls, ceiling, floor;
- metal corners;
- beams, strapping;
- fastenings, plates;
- complete project instructions.
All elements and parts are numbered, correctly sawn and processed for the convenience of the buyer. You do not have to use any additional tools to adjust the kit to the required dimensions. Everything is done for you in the factory by specialists using modern equipment.
By purchasing a kit, you save on excess material, cutting, and transportation.
We have thought through everything to facilitate the construction of a SIP house, the assembly of which takes place according to the designer’s diagram. All you need is your hands, head and time.
The house kit is assembled in stages. All elements are neatly connected and secured. If this is your first time building frame house, you should first carefully read the instructions and study the information on this matter on our website.
Buy from us
You can buy a frame house kit for self-assembly by phone or through our website. There is also a full opportunity to visit our office and place an order in person. To familiarize yourself with the projects, a catalog is provided on the website.
We offer:
- affordable prices;
- high quality;
- delivery and installation at the request of the client;
- convenient forms of payment;
- guarantees;
- a large assortment;
- possibility of adjustment;
- Wide choice of sizes and layouts.
If you are not confident in your abilities or trust only professionals, our specialists will help carry out construction in as soon as possible at prices below market prices.
Frame-panel technology – one of the promising areas in the construction of both residential buildings and industrial buildings. The availability of local raw materials, the simplicity of modern technological processes in manufacturing and assembly, the use of effective heat-saving materials are the reasons for its high popularity. Projects to help victims of natural disasters and the “Affordable Housing” program are based on the use of this technology.
Frame house kit - what is it?
Frame house kit – This is a set of components for assembling a building at the construction site. Each kit is accompanied by a specification with a detailed list of products, location, and type of part marking.
The accompanying documentation includes:
- Frame house project– assembly instructions, drawings and explanations for them, description of the materials used, type of foundation, type of finishing.
- Plans– location of structures, utilities.
- Blueprints– all diagrams of connections between individual structural parts from the foundation to the roof ridge.
- Estimate– quantity and cost of materials and equipment for the project.
Production of house kits for frame houses
Technological process of manufacturing modern frame-panel house based on the conveyor principle. To achieve high quality of all components, high-precision equipment is used. Specialized factories and workshops produce house kits.
The construction of houses using “Canadian” and “Finnish” technologies has become widespread. The modern technological process consists of the following operations.
"Canadian" house kit
House sets are produced using SIP panels. The panels have high rigidity, which makes it possible to do without a special frame.
- SIP panels are made by gluing two OSB panels– Oriented Strand Board, internal frame bars and insulation. Expanded polystyrene is widely used as insulation. Insulation thickness – from 150 mm. The thickness of the entire slab is from 170 mm. The rigidity of the slab is achieved by gluing wooden beams into it.
- The process of manufacturing a house kit takes place on high-tech equipment in a factory environment.
- All parts are cut from the slab according to the project drawings on special cutting equipment controlled by a computer.
- During cutting, openings for doors and windows are cut.
- At the ends of the parts and openings there is a groove into which blocks of wood are inserted.
- For convenience and accuracy of connecting panels at the ends, it is madetongue and groove lock.
- All elements of the house are made from panels:
- Exterior walls.
- Floor panels.
- Ceilings.
- Roof panels.
- Interior partitions.
SIP panels are manufactured with the following characteristics:
- Floor panels – 1250 * 3200 * 200 mm.
- Wall panels – 1250 * 2500 * 160 mm.
- For individual projects, thickness dimensions may vary.
- The maximum axial load on a wall made of SIP panels ranges from 3160 to 4080 kg/m2, with a wall height of 2500 mm.
- The deflection load for a panel length from 240 to 360 mm and a total span length from 4000 to 5500 mm ranges from 95 to 454 kg/m2.
- Thermal conductivity – 0.05 W/m.K.
- Density – 15−17m/m3.
- Sound absorption –74 dB.
Foam plastic of various thicknesses can be used as insulation.
Other parts of the house are made from softwood timber in sizes according to the accepted design. All moldings are planed, dry and sawn to size. Windows can be of any design, both wood and PVC frames. All parts of the house are treated with special compounds against fungus and mold, as well as fire-retardant impregnation.
"Finnish" house kit
Traditionally Finnish technology implies high quality products using natural, environmentally friendly materials. Panels and panels are made from wood, basalt insulation or ecowool for the inner layers of the panel. Expanded polystyrene can be used for the outer layer of insulation.
A standard wall panel is arranged according to the following scheme:
- External plate− made of OSB − Oriented – Chip OSB boards-3. Thickness −15 mm. The board has good rigidity and moisture resistance. Well processed.
- Basalt insulation– IsoBox-Inside. Layer thickness −150 mm. Basalt insulation is non-toxic, durable, and has good sound-proofing and heat-insulating properties. Does not burn.
- Vapor barrier membrane− Tyvek is intended for wind protection, vapor barrier and waterproofing of walls and roofs. Prevents condensation from accumulating.
- Inner plate– gypsum particle board with a thickness of −10 mm. Consists of 15% wood chips, 2% water and 83% gypsum.
- Frame stand– made of dry planed board 45 * 145 mm. Attached between the inner and external panels in increments of 400−500 mm. Serves to give rigidity to the frame.
- End beam– all panels around the perimeter are covered with timber. Bars are also placed in the openings of windows and doors at the ends for attaching mating parts to them.
To enhance thermal protection and decorative finishing, To external wall sheet expanded polystyrene PSB-25F can be attached. On top of it is decorative facade plaster. A vertical lathing is installed between the façade sheet and the insulation for façade ventilation.
- Internal partition panels have a similar structure, but the thickness of the sealant layer is 100 mm. There is no vapor barrier membrane.
- Plinth panels Covered on both sides with a cement-bonded particle board with a thickness of –16 mm. The stove is environmentally friendly, does not burn, and has low sound conductivity. Has high strength.
- Seal layer thickness−200 mm.
- Floor panels– both sides are made of cement bonded particle board with a thickness of –20 mm. Insulation thickness–100 mm.
- Roof panel– has a more complex structure:
- Inner plate– gypsum-bonded, 10 mm thick.
- Vapor barrier membrane.
- Rafters.
- Lathing- made of wooden beams.
- Basalt insulation−200 mm.
- Waterproofing membrane.
- – from timber 40*40 mm.
- Roofing covering.
All elements of the house kit are manufactured at the factory exactly according to the project drawings. Unlike Canadian technology, in Finnish there are no adhesive joints. All layers of panels are sewn together with galvanized nails and staples. The panels contain steam and waterproofing. Wooden parts are treated with antiseptics and fire retardants.
House kits for frame houses for self-assembly
Any house kit, except a large-panel one, can be assembled independently, following the instructions. Self-assembly will take more time and effort. Factories and woodworking shops produce kits for customers who want to build a house on their own. You can order a set of different contents of elements.
A typical kit includes:
- Bottom frame beam– grooves are selected in it for installing vertical and horizontal tongue and groove parts.
- Top frame beam with technological notches tongue and groove.
- Vertical strapping beam with tongue and groove locks.
- Upper and lower floor joists.
- Rafters.
- Lumber for making panels– made to size according to the project. You can order ready-made panels with or without insulation.
- Lumber for the bottom and ceiling– according to the size according to the project.
- Roof sheathing elements.
- Fasteners
- Project documentation with drawings, diagrams and methods of fastening, detailed instructions on assembly.
All parts of the kit must be clearly marked. The specification reflects the location of the parts.
Selection of materials for ceiling and floor coverings, roofing materials, interior and exterior finishing provided to the developer.
The disadvantages of this construction method are:
- Long construction times.
- Great labor intensity.
- Dependence on weather conditions.
pros – low-budget design and construction. House kits of other types can also be assembled on your own and save on a team of builders.
How to choose the right home kit
When choosing a design and materials for a frame house, you must consider:
- Weather and climatic conditions of the place of residence– the choice of wall material, insulation, wall thickness, and the need for increased waterproofing depend on this.
- Seismic activity– use of reinforced structures and type of foundation.
- Soil type– depends on the type of foundation.
- Bedding level groundwater – the possibility of arranging basements, the need for waterproofing, the type of foundation.
- Personal requirements for design and interior– selection of the complexity of the building structure, materials for interior and exterior decoration.
- Objective positive or negative reviews people living in such houses. Their recommendations.
- Personal skills in construction and finishing works ah – when choosing a kit for self-assembly.
Manufacturers offer, as a rule, four types of house kits.
They differ in configuration:
- Low budget– the kit includes only the essentials necessary for the construction of a supporting frame. In the strapping and load-bearing parts, tongue-and-groove type locks are made. The moldings are cut to size from atmospheric drying lumber. There are no insulation or finishing materials.
- Economy– the kit includes all structural parts, wall panels with insulation. Panels in a wooden frame. Timber floors. Internal walls – wooden frame without cladding or insulation. There are no external and interior decoration.
- Standard– a complete set of all parts for building a house, including materials for interior and exterior finishing.
- Lux– a complete set of parts in a modular design. Floors made of panels with filling. Increased rigidity, moisture protection. External and internal finishing materials, drainage and utilities elements are supplied.
At the request of the customer, the equipment can be combined. According to manufacturing technology, the production of frame-panel houses is divided into:
- Small panel– all elements of the kit are made of such a size and weight that they can be moved and installed by two or three people.
- Large panel– building elements are made in large blocks, which significantly increases the speed of installation. The number of joints between panels is reduced, but the use of lifting mechanisms is required.
After deciding to purchase a house kit, you need to visit the manufacturer. Get advice from specialists on manufacturing, delivery, installation. Check the quality of the materials used. See the technological process in action. Order a house project.
Where to order or buy a frame house kit. Price.
In any region there are several enterprises engaged in house construction. The choice of manufacturer depends on factors:
- Distance of the plant from the construction site. The cost of shipping a home kit can be expensive.
- What type of house kits produced by the enterprise.
- What materials used in production and their quality.
- What equipment workshops are equipped.
- By what technology the plant is working.
- Availability of design documentation.
- Availability of warranty obligations to the customer. House kits are supplied in packages protected from precipitation with moisture-proof film. Manufacturing defects may be discovered during installation.
- Availability of visiting specialists for installation or consultation on the construction site.
- Price of the house kit and cost of services.
Price of house kits frame houses varies in regions. It depends on many factors:
- Availability of own raw materials for production.
- Use of imported materials in production.
- Availability of our own technological developments and production.
On average, the price for a frame house kit without finishing the interior and exterior is:
- "Low budget"– from 2000 to 4000 rubles per 1m2.
- "Economy"− from 4500 to 7000 rubles per 1 m2.
- "Standard"− from 7500 to 12000 rubles per 1 m2.
- "Lux"− from 13,500 to 28,000 rubles per 1 m
For an individual project of a house kit, the price may increase by 25%.
The cost of installation by a mobile team increases the cost by 30%.
Departure of a specialist to assist in the installation of a house - up to 7% of the cost of the house kit.
Assembling a frame house kit with your own hands. Step-by-step instruction
When placing an order for the production of a house kit, you must receive a copy of the drawings and a detailed plan for the placement of premises. Check the plan for all dimensions of the external perimeter and distances between internal walls. This data is needed for arranging the foundation.
Construction standard house of ready-made panels consists of the following stages:
- Foundation construction. Lightweight types of foundations are used for a frame house - shallow strip, columnar, pile. The foundation is made strictly according to the project drawings. It is necessary to bring the surface strictly horizontally. Check all angles and parallelism of walls. Leave several technological openings for access to the floors from below. Lay waterproofing material.
- Warehousing delivered house kit. Laying is done on a flat surface through spacers. All elements must be freely accessible. Rafter systems are folded in a vertical position.
- House installation. After the foundation is completely ready, the installation of the house begins. All materials used are included in the package. All joints are sealed polyurethane foam or tape jute insulation. Installation sequence:
- Floor panels are being laid. Additional waterproofing can be done with mastics. Polyurethane foam or jute insulation is applied to the tongue-and-groove lock. The panels are fastened together with anodized screws on both sides of the panel. Strapping beams are placed at the ends of the panels to provide rigidity.
- Installation of the lower beam of the trim. The accuracy of the marking is checked. The timber is laid according to the wall panel template and secured to the floor in a checkerboard pattern with self-tapping screws. Fastening pitch 400 mm. Holes are drilled through the timber, floor panel, into the foundation in 1 meter increments. Anchor bolts are installed. The structure is tightening.
- Installation of wall panels. Starts with a corner panel. The panel is placed vertically along a plumb line on the strapping beam. A second corner panel is installed. The joint is sealed and the panels are attached to bottom harness and each other with self-tapping screws of the required length. The following panels are installed in the same way. Temporary stops can be used during the assembly process.
- Installation of internal panel partitions. They are installed like wall ones. Partitions frame type They are attached to wall panels and to each other using metal perforated plates and brackets.
- Interfloor floor beams. If there is a second residential floor, floor beams are installed. They increase the strength and rigidity of the structure. Beams can be made of profiled timber or prefabricated. Installed according to project drawings using perforated plates.
- Installation of ceiling slabs. Ceiling or interfloor covering is established in the same way as the sexual one. For greater rigidity, floor slabs are attached to floor beams or partitions.
- Installation of gable panels. The ends of the ceiling are covered with timber. The strapping beam is installed. The joint is sealed and the panels are put in place. Attached to the strapping beam.
- Installation of ridge beams. The ridge beam is attached to the gable panels and several vertical timber supports. Fastening occurs using metal perforated plates.
- Intermediate support beams. They cut into the gable panels parallel to the ridge beam. Serve to prevent sagging of roof panels. They are attached to gable panels and several timber supports.
The ridge beam and support beams are the load-bearing elements of the roof.
- Installation of roof panels. The ends of the gable panels are sealed and covered with timber. The roof panels are laid with sealed joints and attached to the gable panels, ridge beams, and support beams with self-tapping screws. The ends of the outer panels are glued with polyurethane foam and sewn up with timber.
- Installation of window and door blocks. Produced using standard technology.
- Installation of roofing. Rating: 4.5 2 votes
House kit - a set of wooden elements of the power structure of a house: wooden I-beams for floors, external wall studs, internal partitions, rafter system, brackets. Floor beams and racks are cut to size. Some elements are supplied 6 meters long - if the rafter system is design features The project is made from dry planed timber. InterCity is developing Constructive decisions projects and prepares house kits based on them for self-assembly or assembly by a hired team.
Frame house kit for assembly:
Why do you need a frame house kit made from I-beams?
For 5 years we have been working with lumber, processing it for our needs: making blanks from it for I-beams, used for the construction of frame houses. We dry, plan the boards ourselves, and impregnate them with Neomid bioprotection to avoid problems with low-quality wood. 50% of the material brought from timber suppliers, as a rule, does not comply with GOST: the material is not completely dried, and after lying in a warm room for a couple of days, it becomes twisted; “screws” are formed due to the internal tension of the not-dry forest; the board becomes moldy already in the structure. Torsion of floor joists, deformation under load in design position cause squeaks, sagging and vibrations.
We guarantee protection against such problems: the lumber prepared by us in a special drying chamber meets the necessary standards and GOSTs.
Developing each individual project house kit, we calculate the loads, select beam sections, think through key solutions with special care: it is important that even a person far from construction can read and understand the project. The use of I-beams in the project allows us to reduce the use of simple lumber, thus we guarantee a reliable house design and durability.
Today, frame-panel construction projects are extremely popular among Russians. And there is nothing surprising here: the technology for constructing such buildings, one might say, has been brought to perfection. And the assembly of the panels itself is easy, even with your own hands, without the involvement of specialists and without paying for their expensive services.
Advantages and disadvantages of frame-panel construction
The main advantage of panel houses is their low cost and high construction speed.
A frame house does not imply shrinkage after commissioning.
Of course, such buildings also have their drawbacks:
- Fragility. In general, the minimum service life of a frame house in the absence of proper care is 30 years, but manufacturers provide a guarantee of 75 years (it is clear that in this case the structure must be maintained for the highest level). If you carry out scheduled repairs of panel buildings as required by engineering instructions, then for such a house 100 years of impeccable service is not the limit;
- Limitation on the number of floors. Basically, all such structures are one-story, rarely seen two-story houses frame type. Projects cannot provide for a larger number of floors, since the construction technology itself assumes that a lightweight strip (and often even columnar) foundation will be used.
Types of panel houses
All panel residential buildings can be divided into 3 large groups:
- Platform house (so-called “Finnish houses”);
- House kit;
- Conveyor houses.
Platform houses are panel houses residential buildings first generation, they were actively built back in Soviet times. First, the foundation was poured (for example, if it was planned to build 25 houses in the village, that is how many foundations were poured at once), and only then the houses began to be built.
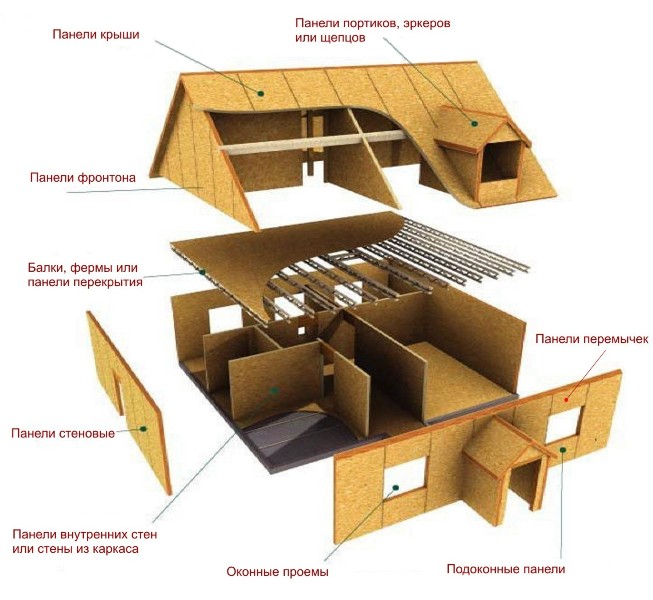
In essence, this is the same conveyor construction, it’s just that switchboard equipment has become much more convenient and technologically advanced. With house kits everything is clear: a kit consisting of necessary materials, and the owner of the site can only connect all parts of the house, having previously arranged the foundation.
True, assemble it with your own hands panel house is not as simple as it might seem at first glance. The main problem in this case is the presence of really large parts (for example, part load-bearing wall). Therefore, the assembly of such panels, its technology itself, may require the use of tower cranes.
But in general, significant savings can be made on construction. And this is the main point. For example, the cost of a turnkey panel house will be 3-5 times less than brick house similar area. As for conveyor houses, their main difference is that the projects for their construction involve the use of sandwich panels.
Currently, there are even special 3D printers that “print” such panels. The construction period for such a building, provided there is a team of workers and special equipment, is 1, maximum 2-3 days. But this does not take into account interior and exterior finishing work, of course.
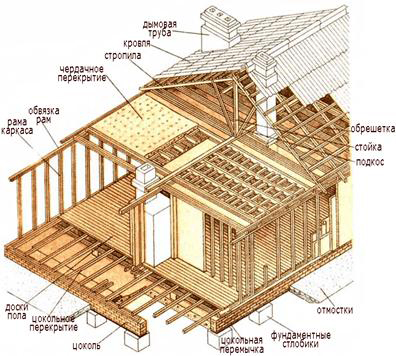
The cost of a frame-panel house is at least 3 times less than a brick house of similar area.
Do-it-yourself assembly of a panel house from factory panels
The design of ready-made panel SIP panels assumes that they will simultaneously serve as the walls of the house and the insulation, so there is no need to worry about additional insulation. The most ordinary foundation for such a house is suitable: even a basic columnar one, as in ordinary village houses.
The SIP panel itself is sheathed on both sides with OSB boards, which have several layers:
- vapor barrier;
- windproof;
- a layer of wind connection (needed for better air exchange, this is the so-called ventilated facade technology);
- The famous expanded polystyrene is usually used as insulation on the panel parts, which is glued there under enormous pressure, which ensures its long service life.
Floor preparation
The surface of the foundation must be covered with a layer of waterproofing film. You can immediately lay the logs of the future floor on it, for which experts recommend using a regular beam measuring either 40x50 mm or 40x60 mm.
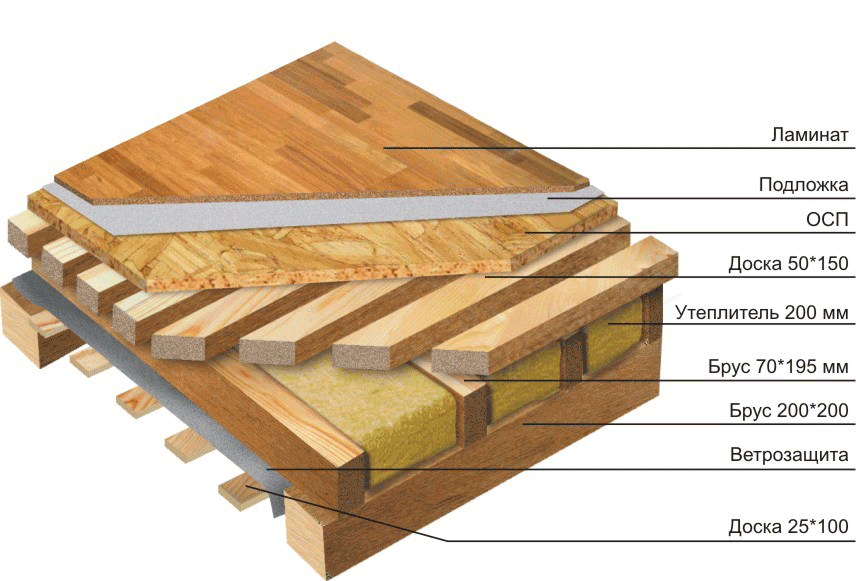
The step between the lags should be exactly 50 centimeters. The wooden floor is laid on the joists.
Wall assembly
All work begins precisely from the corner of the future building. The first element of the entire structure is installed vertically (the lower beam is in the lowest recess). During installation, the panel must be additionally supported by a 3-meter board.
Why 3-meter is difficult to say, but this is what experts recommend. The subsequent ones are attached to the first panel, fastening them together with galvanized metal corners. A beam from the previous one is inserted into each subsequent panel; in some ways, this technology is reminiscent of a children's Lego construction set.
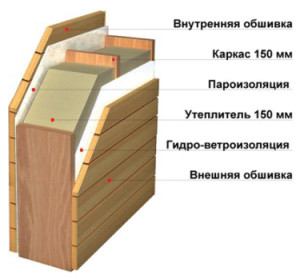
To completely seal the joints before directly connecting different parts of the structure, all openings must be filled with polyurethane foam. During work, it is necessary to check the evenness of the vertical panels with a building level.
Roof installation
After installing all the walls, the top frame is made using timber and the installation of the roof begins. For rafters, ordinary timber is used, which has dimensions of 100x200 mm and 120x50 mm.
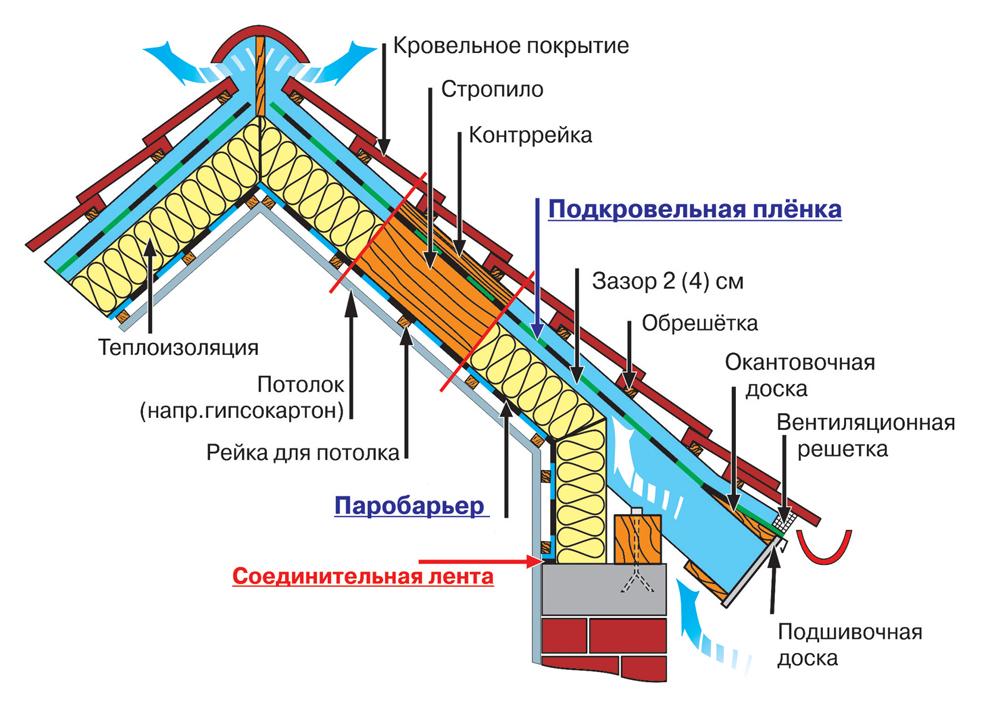
Metal tiles are usually used as roofing. Slate will cost too much, and real clay tiles will simply create a colossal load on the floors of an already very light structure, which is undesirable.
The best roofing option for a frame house is metal tiles.
An example of calculating the cost of a panel house
Despite the fact that many construction companies They offer standard building designs, but these projects can still differ significantly from each other, depending on what equipment is included in these projects.
For example, the cost of building one square meter of housing one-story house with an attic area of up to 100 square meters, in the Moscow region will be approximately 7,000 rubles, a house larger area will cost 500-700 rubles cheaper based on the cost of one square meter.
Houses with availability attic floor will cost slightly less, depending on their area, their price will range from 5,500 to 6,000 rubles per square meter.
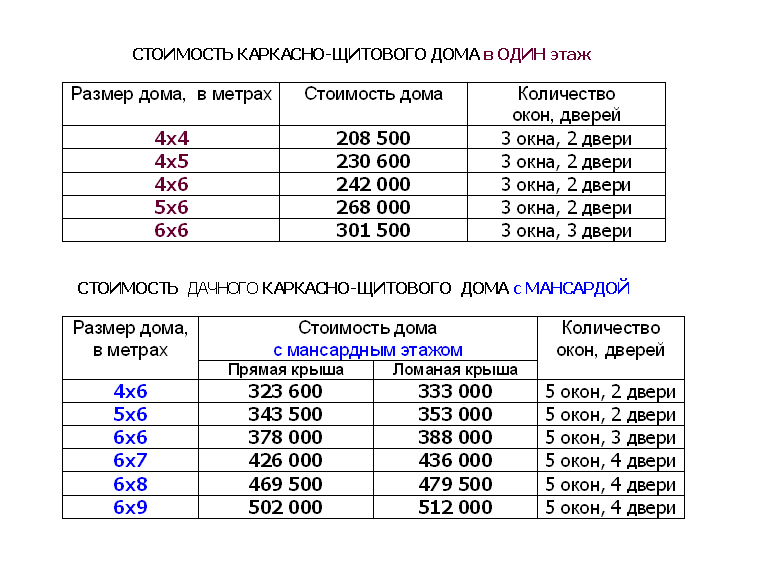
What will approximately be included in such a house:
- foundation (either columnar or on screw piles);
- strapping and frame made of ordinary wooden beams;
- finishing with OSB boards;
- Mineral wool is used as insulation.
Additional equipment may include the following:
- veranda (terrace);
- interior partitions;
- fine finishing.
In general, you can build a solid and large turnkey panel house for a price ranging from 350,000 to 1,000,000 rubles. This is very little money. True, we must take into account that in the same Moscow region or in Leningrad region near St. Petersburg cost land plot can be tens of times higher than the cost of building the house itself.
But nothing can be done here: these are market laws. However, panel houses are usually built in remote regions, where they are used as summer cottages.
Video
You can watch a video that describes how a frame-panel house is assembled using Scandinavian technology.